Organizations are implementing Internet of Things (IoT) projects for many reasons—improved ROI, keeping up with digital transformation, innovation for competitive advantage and more. However, as they begin initiating these intricate applications involving multiple servers and sensors connected to the cloud, their initial concerns (determined in a recent study conducted by Altair and TDWI) of security, collecting real-time reliable data, hardware integration, cost and proving probable ROI often become challenging.
Radio frequency identification (RFID) technology, commonly used in manufacturing and supply chain logistics to track products, shipments and other assets, implemented with IoT applications, can solve these challenges for many use cases. For example, enabling data capture collected in real time, RFID can provide a more efficient and economical way to monitor assets when connected to the internet.
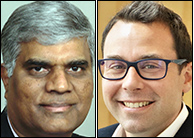
RFID systems can increase the reliability, accuracy and traceability of goods. The technology, integrated with the IoT, can help organizations drive the viability and potential of specific IoT projects. Although RFID on its own may seem like a simple solution that solves some of the IoT challenges businesses face, there are still a number of expenses and potential hiccups around prototyping and testing these projects. That’s why simulation is a critical piece of RFID innovation in IoT projects.
RFID and Simulation
Applying simulations during the RFID application design process can improve IoT projects significantly, as RFID manufacturers do not always consider specific use cases for the technology. Through RFID simulations using electromagnetic simulations to ensure the RFID reader and tag antenna are best optimized for performance, organizations can capitalize on the full promise of the IoT with a more efficient, higher-quality and lower-cost project implementation.
Faster
Efficiency in speed and impact is a critical factor in the world of the IoT. This is not just for end users, but for companies developing these projects who can’t afford to spend endless cycles before their IoT efforts even see the light of day. Once they’re up and running, they need a system that can quickly act on vast amounts of data in a business model that fits and scales for the long term.
RFID on its own delivers on many of these accounts. Whereas alternative IoT methods like barcodes would require an optical line of sight, RFID can read multiple tags at once to capture real-time data quickly and accurately. Add simulation and you up the ante even further. This increases efficiency by running through a vast number of scenarios before production begins, to speed up development and eliminate time usually spent on prototyping. With simulation, trial and error is minimized and the project is ultimately simplified before the pilot.
Take for instance, the case of a large tire manufacturer that uses RFID to track the lifecycle of its smart tires. Because tires receive a great deal of wear and tear, RFID tags can’t be placed on the outside of tires, and if they’re embedded within the tires, there is a risk of performance degradation. Electromagnetic simulations helped significantly reduce the time to production for the manufacturer by optimizing the RFID tag antenna design and location with fewer prototyping iterations.
Additionally, digital twin technology provided a platform to test the various scenarios of the tires, also supported by advanced analytics. Engineers were able to gauge the estimated lifespan of the tires and present a timetable for predicted maintenance. The end result is a finished product part of the connected car ecosystem, by which a driver receives alerts on a vehicle’s dashboard if a tire has an issue or has reached its capacity and needs to be replaced.
Smarter
An RFID tag is essentially a wireless device that can be attached to any object to make its usage smart. As part of the connected ecosystem, RFID readers can locate an object to obtain updates and perform relevant actions, like opening security gates or tracking location. A typical use case of an RFID system designates antennas to generate their own radio frequency field around specific targets, and data is captured by the RFID reader when the tag moves to different places. The reader is connected to the internet to complete and enrich the tracked objects’ available data based on their unique ID, and to help make relevant decisions.
Adding simulation to the mix and the project is even smarter. When planning an IoT project with RFID or any IoT technology, there are numerous details to consider. Finding the right solution for each of those details takes time, money and, in many cases, a lot of trial and error. Using digital twin technology as part of the simulation process enables engineers to run through infinite scenarios before production begins. This eliminates the need to go through the timely and costly process of testing multiple prototypes until performance optimization is achieved.
This was the case for a craft brewery in Europe that was looking to use RFID within its IoT supply chain application to track the lifecycle of its kegs. The information captured through RFID readings is timestamped to track the date on which a keg is filled, as well as its contents, shelf life and shipped date, and when it was received. The application can even show when the keg has been tapped. Because RFID can read multiple items at once, the data analysis shows how many kegs have been shipped, how many remain in the warehouse, how many are waiting in the empty kegs storage area and which ones are being filled or repaired.
What was most unique and challenging with this application was determining the placement of the RFID tag and the antenna design for the reader to capture this specific data. Since beer kegs are made of metal and undergo a wide range of temperatures, finding the ideal location could have taken many rounds of testing, trial and error, and prototyping.
Embedding the RFID tag in the wrong location could cause interference issues affecting performance and accuracy. Thanks to the simulation design process, including testing and predictive analytics, engineers were able to quickly test all relevant scenarios before even beginning production. This quickly determined the best placement for the antenna and tags to receive the most accurate data.
Cost-Effective
Although quality and efficiency are critical pieces of the puzzle, ultimately it boils down to total cost of ownership (TCO) and knowing what your TCO is throughout the life of an IoT project. When paired with the right use case, the deployment of passive RFID tags as IoT sensors can be cost-efficient. This can be seen in instances like minimizing recurrent costs in maintenance and communications.
For example, RFID sensors don’t require batteries like other IoT technologies do. Organizations can decrease costs simply by not having to replace the batteries on multiple sensors once a year. This is especially impactful if the project extends over a 10-year period. RFID technology can also help organizations quickly identify potential problems with kegs and/or possible fraud. If a keg had a leak, if some were not being handled correctly or if one were discarded, the system would quickly ID a problem and save the business money and time.
Using accurate simulations makes RFID even more cost-effective and avoids the expense of multiple prototypes. In the case of a tire company, if engineers did not conduct simulations at all, the manufacturer would have to physically test the product by placing an RFID tag in one place and run a test. It then would have to place it in another location and test again, continuing this process until the whole tire was tested. This cost would quickly add up.
A composite manufacturing site needed to track the full management cycle of carbon fiber parts, including movement to and from the cold room, ID specific rolls, which machine is using it, how much is left, what operator is handling it, and more. On top of the list of tracking that needed to happen, the parts must be stored at -18 degrees Celsius and cannot be used at an ambient temperature for a long period of time during the manufacturing process.
With RFID simulation, engineers were able to help identify the best placement for the antenna, tag type, shield effect and more. IoT technology helped to do the rest. Costs were kept significantly lower than with the traditional prototype process, which saved these businesses money.
As seen in these different use cases, RFID technology is a winning factor in relevant IoT applications. Whether or not you’re implementing RFID, including simulation design in your IoT process will be critical for optimization, determining proof of concept, and ultimately the project’s success. Having the ability to test various scenarios around the use case helps business cut down on additional costs. Leading to ROI, these IoT sensors, RFID tags and more can provide accurate and valuable insights using real-time data analytics.
Alvaro Everlet is the senior VP of IoT at Altair, where he works with customers to successfully build Internet of Things solutions and strategies that meet their technical and business goals on the road to digital transformation. You can reach him at [email protected], @aeverlet, or linkedin.com/in/alvaroeverlet. Dr. C.J. Reddy is Altair’s VP of business development for electromagnetics in the Americas. He is a Fellow of IEEE, ACES and AMTA, an associate editor for the newly introduced IEEE Open Journal of Antennas of Propagation, and a member of the AMTA Board of Directors. You can reach him at [email protected] or linkedin.com/in/cjreddy01.