Since launching an RFID solution to manage the helmets and jackets its contractors wear, Indonesian digital multi-service platform Gojek has produced 1.5 million of these products with built-in UHF RFID tags. Those tagged jackets and helmets can now be tracked as they move from production through distribution and sale to a contractor.
In that way, Gojek reports, it has reduced the number of man-hours required to manage the supply chain, while ensuring the right products are available for sale to contractors. The company can also use the RFID data to capture a record of who buys each item, so that it can be reminded when maintenance is due. The solution is provided by systems integrator Zulu, including an app to manage the goods, while PT Electrodata is selling the RFID hardware, which comes with UHF RFID tags from Confidex.
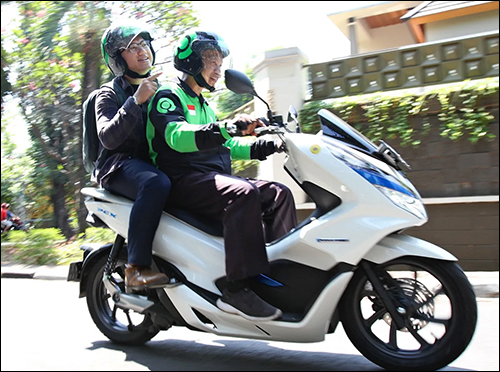
Gojek, which operates throughout Southeast Asia, launched in 2010 as a ride-hailing service, similar to U.S.-based Uber, but on scooters. The name “Gojek” is derived from the Indonesian word “ojek,” meaning “taxibike.” The company expanded five years later to three services: GoRide (for ride-sharing), GoSend (for couriers) and GoMart (for shopping assistance). At present, Gojek is valued at about $10 billion and offers what it calls a “Super App,” which provides more than 20 services ranging from scooter rides to house cleaning, car washing and massage.
As of 2018, Gojek had a fleet of one million drivers and 30,000 professionals for personal services. Customers can call upon these contract-based employees using the Super App. On both city and rural streets, they can be easily identified by their Gojek-branded helmets and jackets. The company has strict requirements that every contractor must wear such gear, and that these items must fit well and be in good working condition in order to maintain proper branding. Each rider must also carry a Gojek helmet for passengers.
Getting millions of these products into the hands of drivers and service providers proved challenging. The personal gear is made at Chinese factories and is sent to a main distribution center in Jakarta, and then to satellite DCs throughout Southeast Asia before a contractor can access and purchase them. Without the RFID-based solution, counting every carton of goods as it is received at the DC can be time-consuming—it could take 15 minutes or more per carton of 50 jackets for workers to scan the barcodes and ensure that the products are in the specified styles and sizes before they are re-routed to the appropriate location.
To make this process faster and fail-proof, Gojek began working with Zulu to provide wearable technology. Zulu designed a system that employs RFID tags built into the items at the factory. The tags can be read via a handheld reader, and Zulu’s app enables individuals to view data regarding the items using a smartphone. Confidex Carrier tags are sewn into the jackets, while Crosswave tags are built into the helmets. “Gojek needs to track the products from manufacture to distribution,” says Edward Lu, Confidex’s sales director for the Asia-Pacific region. The tag enables each item to be tracked from the production floor in China to the item’s sale and on to a contractor.
Zulu began working with Confidex on Gojek’s solution last year. As the product is made, the RFID tag’s unique ID number is stored along with the product details in Zulu’s app, which integrates with Gojek’s own app. The goods are next shipped to Gojek’s Jakarta distribution center. As items are received, warehouse personnel use a handheld RFID reader to capture data from the tags in each carton without opening it. The information is captured in the Zulu app, which updates details indicating which goods have been received.
In the past, manual checks of cartons and distribution required a clipboard and 15 minutes of employee labor, whereas now this can be accomplished using a handheld reader within approximately three seconds, without requiring that the box be opened. As the jackets and helmets are ordered for local DCs, the items can be read again via a handheld reader in order to confirm what is being shipped.
At the local site, staff members are equipped with handheld readers and they, too, capture the unique ID number encoded on each tag, enabling them to view what inventory is available onsite and thus avoiding out-of-stocks. Because Gojek creates a record of which product is sold, as well as when this occurs and to which contractor, the company can send a rider a reminder when a helmet needs to be checked for maintenance. That data can be sent via the Gojek app that the contractor utilizes to manage his or her work.
Initially, the solution is aimed at supply chain management, to ensure that the helmets and jackets are available at each distribution site, both in city and rural stores. But in the long term, Gojek could utilize the built-in RFID tags to track products even after they are purchased. Since the system was taken live, around 1.5 million items have been tagged as they were made, with expectations that about two million more will be tagged annually.
Confidex faced a challenge when it came to providing an RFID tag that would be reliable on both helmets and jackets, no matter what they might be exposed to. The Confidex Crosswave tag was selected for helmets, Lu says. “It’s a very tough environment for RFID,” he explains, “because of multiple materials in the helmet itself, so performance of the tag is really important. That’s where Confidex shines, with a dual antenna that thrives in tough environments.”
Gojek’s initial benefit, Lu says, is a fast and efficient supply chain, thanks to faster check-in and check-out processes. “The issue of getting the right size to the right people has also been addressed,” he reports, noting that a good fit and a clean, well-maintained helmet and jacket are important for the brand’s image.
For the next phase of the deployment, Gojek intends to begin tagging food-delivery containers. The company now enables customers to use its Super App to order food. Therefore, contractors are delivering meals to customers in reusable containers lined with aluminum. Confidex is currently in the process of designing a special tag for that application, which operates well when attached to a foil bag. In the long term, the technology could be used to track cleaning equipment and other assets used by the contractors.