Analyst firm IDC predicted that in 2022, worldwide spending on technologies that enable digital transformation will reach almost $2 trillion. According to the report, the manufacturing industry is forecasted to be responsible for a large portion of digital transformation spending in 2019. Streamlining production through automation technologies and optimizing a digital supply chain are key priorities for manufacturers.
Implementing RFID technology in production is a significant part of the automation and greater digital transformation process. However, automating data and workflow management is also critical to improving inventory management and increasing efficiency of RFID in the supply chain. This can enhance manufacturing and production line productivity, dictate warehouse and shipping movements, track logistics and inform smarter business decisions.
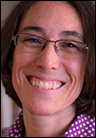
Traditional data- and content-management services—which aim to capture, manage and store all the information necessary for businesses to operate—can result in data that is siloed and incompatibility with other IT systems. This then leads to limited business processing and workflow capabilities.
At the same time, as technology continues to evolve, old data-management solutions are now interacting with a growing number of specialized technologies, including artificial intelligence (AI), RFID tags, optical character recognition (OCR) and natural language processing (NLP) tools. As a result, a unified data or content services platform is necessary to effectively manage the various technologies with a holistic, yet intelligent approach.
Combining data management with digital process automation (DPA) tools allows manufacturers to improve how different technologies, including RFID, interact with each other to improve operations. With low-code DPA tools, IT teams, different departments and customers can then access information across multiple platforms to achieve greater efficiency among complex operations.
Below are five benefits manufacturers that are leveraging RFID technology can obtain by integrating low-code DPA tools within their data-management solutions.
1. More intelligent content: The combination of low-code platforms with AI and machine-learning technologies enables businesses to add intelligence to their processing capabilities. For example, when these technologies are integrated with DPA tools and the data collected with RFID tags, the result is a smarter, more robust management of data that then leads to improved production, insight and operations. The ability to add intelligence into any area of the organization (i.e., checking an order’s delivery status, the status of payment processing, etc.), allows distributors or manufacturers to improve the efficiency and even the safety of operations through automation.
European manufacturing company Arntz Optibelt Group experienced this firsthand. With the help of low-code process-automation tools, the manufacturing company was able to automate its most critical paper-based approvals processes. Optibelt’s new applications have increased the speed of the time to market for new products by 75 percent, enhancing production-line agility and reducing approval times from 50 minutes to 30 seconds.
2. Centralized content and workflows: A low-code platform can act as the glue between separate systems, departments and locations. This could include technologies such as RFID and equipment in a production line, or data from content-management systems such as SharePoint, Google Drive and DropBox.
For example, Czech Republic furniture manufacturer TON’s absence of an automated content-management system was creating a loss in invoices, delayed approvals, siloed data and increased challenges in figuring out the status of any active contract. TON utilized DPA technology to build simplified and user-friendly solutions that have now centralized workflows, unified document storage, automated data mining and invoicing processing and reduced administrative burdens on their IT staff and infrastructure.
3. Increased collaboration and accessibility: Users often waste time looking for the right data that lives across multiple content-management systems. Connecting the systems allows for content to integrate across platforms, which directly results in improved collaboration and visibility within an organization.
Data from RFID tags (when connected with low-code DPA solutions) can be integrated with a data-management system in place to automate inventory management and improve customer service. Instead of manually searching for the status of an order, the connection of systems optimizes the ability to track and report the information to customers, which can also be accessed and updated in real time from any device.
4. Improved agility to adapt to business needs: Low-code DPA solutions also enable rapid workflow development and creation. Easy integration with all line-of-business systems such as this allows users to build specific content-centric applications that will meet customers’ needs, like RFID improvements. Manufacturers and distributors can quickly respond to changing business needs and evolving RFID solutions within their existing low-code development platform. This improved agility allows an IT department to test, learn and pivot where appropriate. Further, IT teams can create and deliver business solutions quickly, incorporating feedback from internal and external stakeholders.
5. New visibility and control: With the combination of low-code DPA with data management, organizations can see what happens to content, data and orders along every step of the way. Through the visibility provided from a low-code solution, organizations are then given a holistic view of how their content is performing within their business workflow and how to optimize applications more efficiently to drive ROI. This type of visibility results in manufacturers having improved control and the ability to make informed data-driven business decisions.
Such improved control and visibility can be seen in Kimberly-Clark’s digital transformation journey. Before integrating DPA, the multinational personal care corporation had manual processes in place that were slow and would often end up stuck on someone’s desk waiting for a signature. Because many of these processes were either paper-based or in closed systems, it was impossible to track down the roadblocks. Now, with more than 500 low-code partially automated processes in place, Kimberly-Clark’s operations are streamlined and visibility has dramatically improved. The corporation now has a tool it can consistently use to improve efficiency across its organization.
In conclusion, data and inventory management through DPA allows manufacturers to create solutions that better meet and anticipate customers’ changing needs, instead of operating in siloed and inefficient models. When a manufacturer combines data with automation technologies, this creates centralized applications that enable improved productivity, added intelligence and customized opportunities for new ways to collaborate within the global supply chain.
Holly Anderson is the senior director of product marketing at K2, where she leads product messaging, value proposition and customer communications. Holly has more than a decade of experience with K2, both in-house and as a consultant, since 2006.