Thermocouple manufacturer TE Wire & Cable and Internet of Things (IoT) software company Plataine are offering manufacturers a joint, RFID-based IoT solution. The system utilizes artificial intelligence (AI) software to track the location and usage-based status of its temperature-monitoring products.
By employing the RFID capabilities of the new Smart Thermocouples, TE Wire & Cable’s manufacturing customers can identify exactly when a thermocouple needs to be replaced, without having to manually record data, and then quickly find that device within their facility. The technology also offers real-time alerts and recommendations for thermocouple calibration, says Joseph Ugalde, TE Wire & Cable’s marketing business analyst.
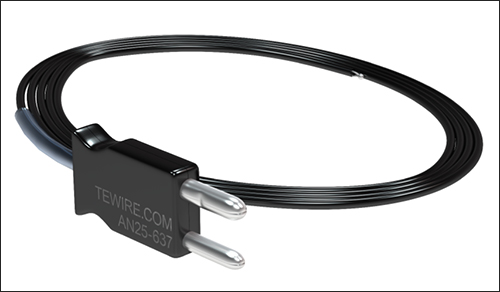
This solution, TE Wire & Cable reports, may be the first to leverage RFID for this purpose in its industry. The company developed the system together with Plataine, following requests from some of its customers that use the products to track temperatures in their autoclaves when making aircraft parts.
TE Wire & Cable, a Marmon Wire & Cable/Berkshire Hathaway company, sells thermocouple assemblies used in the making of composite aircraft parts. The manufacturing of such parts requires that autoclaves apply heat and pressure to the material within a very specific temperature range, in order to ensure the parts’ integrity. The thermocouple, a thermoelectric assembly for measuring temperatures, is connected to a jack panel within the autoclave, where the respective temperature data is run through and then fed into a data logger. When manufacturers create a new part, they typically embed the thermocouples into a “layup” before it enters the autoclave.
When the part is then rolled into the autoclave, thermocouples are automatically connected to the autoclave jack panel to which they will be attached. Since thermocouples have a limited life span, companies must closely monitor how often each unit is being used. This is usually accomplished simply by filling out paperwork and counting usage events. That becomes even more complicated when hundreds of thermocouples, or batches of them, are in use. “Aerospace companies use a plethora of these devices,” Ugalde explains, adding that “there could be hundreds of thermocouples” at a typical site.
Not only is usage history difficult to track for hundreds of thermocouple assemblies, but they can be hard to find as well. When a company determines that thermocouples need to be removed from service and replaced, an employee often must spend a considerable amount of time tracking them down. That’s especially true at the large assembly sites where most aerospace products are built.
TE Wire & Cable teamed with Plataine to develop a solution that consists of Smart Thermocouples with RFID tags embedded in them. The companies provide RFID readers to capture transmissions from the tags, along with Plataine’s IoT AI-based software. Plataine already offers a variety of RFID- and IoT-based solutions for asset or tool tracking in industrial environments, explains Amir Ben-Assa, Plataine’s chief marketing officer.
“We began to work with TE Wire around 12 months ago,” Ben-Assa recalls. “During this period, we defined and tested our joint Smart Thermocouple solution enabling manufacturers to extract additional value from their thermocouples and enter the era of Industry 4.0.”
The Smart Thermocouple is the same as its predecessor products from TE Wire & Cable, the company reports, but will include a passive UHF RFID chip placed in an indentation on the device. The chip will store a unique ID number linked to a specific product’s serial number on Plataine’s cloud-based software. Those using the Smart Thermocouples would require fixed RFID readers to capture the tag transmissions. For this purpose, Ugalde says, TE Wire & Cable will work with customers to identify and install the best reader for each particular facility and use case.
With the initial plans for the system, as an autoclaving process begins, equipment is rolled into the area and will pass through a fixed reader portal, where the unique ID number on each thermocouple will be captured. The reader will then forward that data to the software, which will update the thermocouple’s location based on the reader portal that has captured the ID number. The software will also change the status to indicate that the thermocouple is being used. Once the thermocouple leaves the area, that event is captured by the portal reader.
As the device is repeatedly used, the software tracks the number of uses and can issue an alert at pre-determined points, such as after the 15th use for a thermocouple intended for only 20 uses. Employees can view the device’s most recent location and replace it when necessary. This saves them considerable time they would otherwise have to spend walking around the facility looking for the thermocouple, Ugalde explains.
By no longer having to rely on paper and pen, Ugalde notes, users could also prevent unintended overuse of a product. “Even if you have a meticulous process of record,” he adds, mistakes could happen and the device could be used past its expected lifetime. An overused thermocouple may not provide an accurate reading.
The system is currently undergoing the testing process at Plataine’s lab, after which some of TE Wire & Cable’s customers intend to begin testing the technology at their own facilities. Plataine’s IoT solutions use RFID and other factory-floor sensors to collect real-time information about material, work-in-progress, assets and tools, and to extract real-time alerts and information about the manufacturing process. “We serve a variety of advanced manufacturing sectors,” Ben-Assa explains, “such as aerospace and defense, automotive, renewable energy, heavy industry and medical devices.”