In 2016, the Internet of Things went mainstream, but in 2017 we expect the Industrial Internet of Things (IIoT) to transform operations across numerous industries. Also known as the Industrial Internet, the IIoT enables machine-to-machine (M2M) communication of usage, performance and health metrics. There is quite a buzz around using this data, along with machine learning and other predictive algorithms, to help anticipate and eliminate potential causes of downtime.
Nowhere is this more evident than in the commercial asset service ecosystem. Trucking fleets, construction assets, agriculture and power-generation equipment are all susceptible to costly unscheduled downtime and generally long repair cycles.
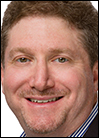
Making the Connection to Improve Transportation Fleet Service Events
Effectively leveraging the IIoT is critical to commercial assets, because it has the opportunity to introduce automation and efficiencies that currently have significant negative bottom-line impact. This is especially true in transportation, for which the average downtime for an asset is around four days but only around 10 percent of that time is attributable to actually fixing the issue. However, capturing machine data is just one piece of the process, especially when it requires multiple disconnected phone calls and emails to actually start to engage on a repair event.
To effectively manage the repair and maintenance process requires contextual access to asset diagnostics (including severity, likely cause and repair plans), along with service history, warranty coverage, maintenance status, build details, pending operations and service campaigns, and other information, which is typically scattered across multiple online and paper-based systems. To make matters worse, communications, updates and approvals are also challenged by manual-, phone- and paper-intensive processes. This all results in extended asset downtime, mountains of paperwork and a lack of transparency into the service supply chain.
Collecting IIoT-based information from these assets is a good starting point and can, over time, be used to improve the specificity and severity around certain types of fault codes, and eventually be used for predictive (or condition-based) maintenance. However, having access to this information alone is not enough—this data has more value when it’s part of a closed-loop service event management process that paints a bigger picture to help facilitate faster repairs, less downtime and better decision-making.
Getting More Value from IIoT Data
Service relationship management (SRM) is an approach that enables more efficient and effective management of service events by aggregating, in real time, all relevant data at the point of service, and by ensuring all parties in the service supply chain ecosystem can communicate and collaborate easily. Think of it as the glue that brings it all together.
This connected, closed-loop ecosystem can capture data from all required parties, including fleets, original equipment manufacturers (OEMs), service suppliers, and a multitude of third-party applications, such as telematics and diagnostic tools, shop and maintenance applications, and information providers.
Business rules can also be applied to IIoT data to automate notification and service case creation, in which technicians and others have direct access to fault data, as well as repair plans and diagrams. This significantly reduces triage time and overall downtime.
Data is then stored in a secure, one-stop portal that provides real-time information and dashboards to quickly identify potential issues, track and audit complex paper trails, and measure and monitor events based on industry best practices, standard repair times and estimated times of repair.
Plus, as more data is collected, connected fleets can find new ways to use that data and ensure it is actionable going forward. With data-powered business-intelligence insights, teams can detect problems earlier in the repair process, apply appropriate course corrections during an event, and drive continuous improvement of the process through tools that measure successes and failures once the repair has been completed.
A New Paradigm for Streamlining Service and Repairs
As the IIoT steps out of the shadows and sheds the chains that have kept data from being holistically actionable, we’re seeing the beginning of a new commercial asset-management paradigm. Powered by SRM, the entire service supply chain is connected from the beginning until the asset is back in service.
With new levels of visibility and transparency, and an actionable closed-loop process, SRM is quickly taking the headaches out of asset maintenance—reducing triage and downtime, driving greater fiscal accountability, and improving decision-making. It’s creating a more connected, intelligent, collaborative environment with minimal asset downtime, and is truly helping to deliver on the promise of the Industrial Internet of Things.
Michael Riemer is the VP of products and channel marketing at Decisiv.