Finnish technologies company Valmet Technologies is launching a radio frequency identification system to track the use and replacement of cloth filters for its customers, including mining, paper and energy companies. The solution, which includes tags attached to filter cloths and readers mounted on a framework that holds the filters, tracks when each filter is installed, when it was replaced and why this was necessary. In this way, the technology provides analytics that help customers monitor the replacement of cloth filters, enabling them to better schedule future filter changes. The system will also help Valmet improve its products, by allowing it to view how well they perform in specific environments and under certain conditions.
Valmet makes a wide variety of textile-based filters for various industries. The filters are designed to separate solids from liquids or gasses. Organizations such as mining firms, paper producers and energy companies use such filters to remove solids for numerous purposes. Over time, the cloth can become clogged (a process also known as “blinded”) or break, requiring that it be replaced by a new, clean filter. These cloths, provided by Valmet, vary in size from 50 square centimeters (7.5 square inches) to large pieces that can measure as much as 100 meters (328 feet) in length and require a crane for installation or removal.
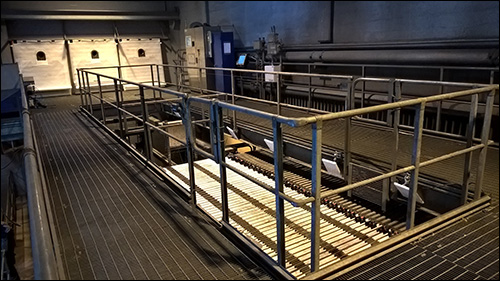
Traditionally, says Sanna Uusitalo, Valmet’s product manager, customers must track their own filter cloth consumption. Some cloths need to be replaced every few weeks, she explains, while others could last for more than a year, depending on the application. Determining when a filter will need to be replaced has been an imperfect science—some users try to manually monitor the filters via paper and pen, whereas others simply end up replacing filters when they fail (if they break during the filtering process, for example). The latter method can lead to unnecessary delays in the operations of equipment, which can be costly. On the other hand, companies that simply replace filter cloths on a predetermined schedule could end up replacing them prematurely, resulting in an extra expense.
Uusitalo says her company has been considering an RFID solution for some time. Not only would the technology benefit customers by ensuring that their filter cloths were replaced at the appropriate time, she adds, but it would also create a digital record that would help users determine how well the cloths are working in their equipment. In addition, the system would provide Valmet with information that it could use to improve its products’ robustness for specific applications.
Valmet tested ultrahigh-frequency (UHF) RFID technology throughout the past 12 months at a Finnish mining company. The firm had a single filtering system in place, consisting of 108 cloths to separate solids from liquids. Valmet installed nine MTI circular RFID reader antennas with a single Impinj Speedway Revolution reader inside the filter system above the cloths, and embedded Smartrac DogBone UHF RFID tags in the filter cloths themselves. During the embedding process, Valmet encodes each tag with a unique ID number, which is stored in the company’s software and linked to that customer, along with a date and time stamp.
When the cloths are installed in the filter system, the readers capture each tag’s ID and forward that data to a cloud-based server managed by Valmet. The system then knows which filter cloths are installed in a given filter unit. Each time a cloth is removed, the reader ceases receiving transmissions from that cloth’s tag, and the software thus knows it has been removed. Valmet wanted to enable users to also input the reason for replacement (blinding or breakage, for instance) into the Valmet software, so it provided its customer with a handheld RFID reader. When the cloth is removed, an operator interrogates the RFID tag on that cloth using the handheld, and Valmet software prompts him or her to input the reason for the cloth change.
With this technology, Uusitalo reports, users do not have to record when they install each filter cloth. “The system automatically gives time stamps for the installation and starts to count the life time,” she says. “It gives us an accurate understanding of how long [the products] work.” Since Valmet knows the sort of application in which the cloth is being used, it can test ways in which to increase the lifespan of its cloths.
The mining company can use the collected data to better forecast when a filter cloth requires replacement, as well as determine cloth lifespans at each location within a filtration system, under specific conditions. In this way, it can identify any problems involving the equipment or its use that might be damaging the cloths.
The mining company concluded the pilot this fall, Uusitalo says, and plans to continue using the system in the future. In addition, another customer has begun installing the technology at its own mining operation, with seven filter systems in a single operation, using 700 filter cloths at once. That installation is slated to be taken live in April 2017.
“One benefit of the technology is we have real accurate information about the breaking of cloths,” Uusitalo says. “We know where it occurs and can see patterns. That helps us improve our product.”
For users, employees no longer need to write down when filter cloths were installed or removed. Instead, they can now begin to create an accurate schedule related to replacing cloths before they fail.
Uusitalo says the RFID-enabled cloths are now being offered to all of Valmet’s customers. She expects the system will be most advantageous to those that use many cloths in their operations, or that have high filter cloth consumption rates.