I’m not sure if it’s just the positive news articles that have been written about radio frequency identification, or a natural process of evolution, but it’s clear to me that aerospace and defense companies that had previously been simply complying with requests from customers—namely, Airbus, Boeing and the U.S. Department of Defense (DOD)—by tagging shipments or parts are now beginning to use the technology for their own benefits. And this is the reason we are holding an RFID in Aerospace and Defense event in Long Beach, Calif., on Oct. 20 (with RFID certification training taking place on Oct. 19).
BAE Systems is a good example of a company that has gone beyond tagging for customers and is using the technology to achieve internal benefits. BAE’s Electronic Systems division, which supplies mission-critical electronic systems, including flight and engine controls, surveillance and reconnaissance sensors, and power- and energy-management systems, to commercial and defense companies, is using RFID to automate the tracking of tools and equipment. This reduces search times, streamlines equipment maintenance and improves equipment utilization. Joshua Landry, the company’s program-engineering manager, will be speaking at the event.
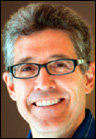
Orbital ATK is another company using RFID for its own benefit. Its Aircraft Commercial Center of Excellence (ACCE) manufactures composite structures for the Airbus A350 XWB and Boeing 787 Dreamliner programs. The ACCE has created a “visual factory,” in which each step of the composite-manufacturing process is monitored automatically, from raw material receipt through component production and eventual shipment to customers (see ATK Tracks Composite Airc). Jim Morgan, who helped set up the system for Orbital ATK, will speak at RFID in Aerospace and Defense to explain why RFID is a critical enabler for ramping up production for the company’s original equipment manufacturer (OEM) contracts.
It’s not just suppliers to Airbus, Boeing and the DOD that are taking advantage of RFID. Because planes are now being delivered with tags on some parts, customers are beginning to employ the technology as well. Delta Air Lines, which operates more than 5,000 flights daily across an extensive domestic and international network, is using RFID in its maintenance operations, tagging onboard aircraft equipment that must be managed for both presence and expiration date (see RFID Reduces Oxygen-Generator Waste for Delta Air Lines).
New aircraft come with tagged items, and Delta has installed more than 240,000 RFID tags on oxygen generators, life vests and cabin emergency equipment on all of its existing owned and leased aircraft. As a result, the airline can now check the expiration dates on oxygen generators aboard a 757 in less than two minutes, compared to approximately eight man-hours without RFID. Rick Lewis, a business analyst for aircraft maintenance at Delta, will speak at the event, explaining how this saves Delta money and helps it plan more effectively.
In addition to learning from these speakers and hearing other great case studies, event attendees will be able to meet the RFID companies that have developed solutions specifically designed for the aerospace and defense sectors. I hope to see you at the event on Oct. 20 in Long Beach.
Mark Roberti is the founder and editor of RFID Journal. If you would like to comment on this article, click on the link below. To read more of Mark’s opinions, visit the RFID Journal Blog, the Editor’s Note archive or RFID Connect.