For the past five years, the Pyhäsalmi mine in central Finland has been using passive high-frequency (HF) RFID tags to record when workers enter or leave a mine shaft, and thereby ensure their safety during controlled explosions and evacuations. Since that time, says Kimmo Luukkonen, the mine’s managing director, the technology has improved management’s visibility into who is underground and when, and hence has increased its safety program’s efficiency and accuracy. The company plans to expand that HF RFID solution to monitor who carries explosive detonators into the mine.
All of the RFID technology, including Idesco HF and ultrahigh-frequency (UHF) RFID readers, was provided by Identoi Oy, a software and mobile solutions firm based in the city of Oulu.
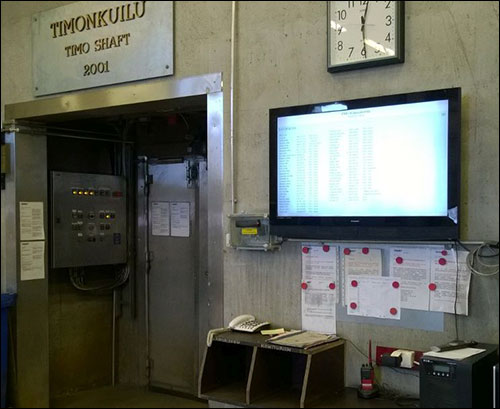
One of Europe’s deepest and oldest underground mines, Pyhäsalmi is owned by a Canadian corporation called First Quantum Minerals, and extracts underground copper and zinc 1,400 meters (4,600 feet) below the surface. The mine has two shafts: one for the elevator that transports miners down and brings ore up, the other extending down to that level via an approximately eight-mile-long spiral that vehicles can drive down and up.
In 2009, the mine’s managers began working with Identoi to implement a work-safety system that would automatically identify who is in the mineshaft at any given time. Knowing this information is important for two reasons: In the event of an emergency evacuation, the company needs to ensure that everyone has reported to an emergency shelter, and also needs to be able to identify any individuals who have not. In addition, the mine extracts metal by blasting rock in certain sections, and these controlled blasts require that the mine be entirely vacated.
Prior to installing the RFID-based solution, the company manually tracked who was in the mine. Each worker had a nameplate stored on the wall at the mine entrance. Upon entering, an employee took the plate and carried it around with him as he worked. Once he ended his shift, he replaced the plate as he left. As such, if the mine’s management needed to see who was inside, they could simply look at the entrance wall to determine which plates were missing. This system was error-prone, however, since workers might forget their plates, and it didn’t account for visitors, who were not issued nameplates.
The RFID solution consists of passive 13.56 MHz RFID tags compliant with the ISO 15693 standard, explains Sakari Vaara, Identoi’s CEO. Each tag, made in the form factor of a key fob, can be attached to a worker’s keys. All employees must carry their tags at all times while onsite. There are a total of 220 workers, 70 of whom are typically underground during their shift.
When entering the mineshaft, a worker taps his blue Idesco Sail Tag against an Idesco Access 7CE reader installed at the entrance. The reader captures the tag’s ID number and forwards that information to Identoi’s software via a cabled connection. The software then prompts that employee’s name to be displayed on a large screen mounted above the entrance. If an individual brings a guest, that person uses a touchscreen connected to the Idesco reader to indicate how many guests he is bringing with him. The software stores that individual’s ID so that management can view a real-time list of miners underground.
When leaving the mine, the worker must go through the same process. He places his tag near a second Idesco reader dedicated for outgoing foot traffic, and his name is then displayed on the same large screen, thereby indicating that he is leaving. This data is stored in the Identoi software so that the mine’s management can view, at any time, who is in the mine and who has left, as well as how many individuals are there altogether.
In the event of an emergency, workers are trained to report to one of 23 emergency shelters. At each shelter, the mine installed two Idesco HF readers, one that workers tap as they enter the shelter, and a second to be used as they exit. If miners who should be in an evacuation shelter are reported as not having tapped their tags at that location’s entrance, the mine can use its voice communications and begin searching for those individuals, including calling them individually by radio. According to Vaara, the system uses HF RFID technology for staff management due to its short read range. With UHF, it would be possible to capture stray reads of individuals walking around near the entrance or evacuation shelters without actually entering.
In 2012, the mine installed UHF RFID technology so that it could record which trucks, vans and cars had entered its aboveground operations area. To enter the site, vehicles must pass a gate where an Idesco EPC UHF reader is installed with two antennas—one dedicated to incoming traffic, the other allocated for outgoing vehicles. Each authorized vehicle has an EPC UHF RFID tag, from one of a variety of companies, mounted on its windshield. By using UHF RFID readers, the company can capture the ID number as soon as the vehicle approaches the gate, and can then identify that vehicle, authorize the gate to open and create a record of who has entered and left the site.
This year, the mine also intends to use passive HF RFID tags to track detonators. Workers employ specialized vehicles to inject explosive materials into holes, and then insert detonators. The detonator manufacturer prints an ID number on each product in the form of a QR code. When deploying a detonator, a miner utilizes a handheld reader to interrogate his HF tag, and then scans the QR code to link his ID with that of the detonator, which is saved in the mine’s enterprise resource planning (ERP) system. Later this year, the mine plans to attach an HF tag to each detonator, and a miner will uses a handheld unit to read both his own HF tag and that of the detonator.