German manufacturer Rehau is employing radio frequency identification technology to track the automotive bumpers it fabricates at its eight global facilities, thereby increasing the efficiency of its processes from injection molding to final fabrication, and to quickly identify any problems related to a particular customer’s order. The system tracks the parts through injection molding, painting and fabrication, in order to record each process completed for every bumper. In the long run, the company hopes to expand its use of the solution—which was provided by automatic-identification software firm noFilis AutoID—so that it can track the shipment of bumpers at all facilities. In addition, Rehau is urging its suppliers to begin tagging their own materials prior to shipping them to Rehau’s assembly facilities.
Rehau is a global manufacturer of polymer-based products for the automotive, industrial solutions, furniture and construction sectors. Among its products are painted bumper systems for automotive manufacturers. Approximately eight years ago, it began looking into solutions involving passive ultrahigh-frequency (UHF) RFID tags, to determine whether the technology could assist in monitoring the locations and status of bumpers during assembly at the company’s plant in Feuchtwangen. It started with a single assembly line for bumpers destined for one of its automotive customers, BMW. Rehau designed the solution, selected hardware and created its own software integrated into its own enterprise resource planning (ERP) system.
Because the RFID technology worked well, the company sought to expand the solution to all bumpers at that site, as well as to those made at its seven other locations around the globe. However, the company reports, the readers it had deployed were becoming obsolete, and integrating software related to disparate RFID systems would be a difficult task. Rehau required an innovative solution that could be integrated into its multiple sites, connect to various reader types, prefilter the captured data and be managed centrally as it expanded the system to its other plants. Therefore, says Marcel Munzert, Rehau’s corporate IS production logistics RFID expert, the company signed a contract with noFilis in early 2012, by which noFilis would provide Rehau with RFID hardware and software, as well as integration and support.
Prior to deploying RFID, the company had little means of tracking each bumper’s location as it moved through several phases of injection molding, painting and fabrication. When a new bumper being built arrived at each workstation, those working on the production floor had to determine that bumper’s type and to which station they should send it, based on its style and customer requirements. This was becoming increasingly difficult, the firm reports, as the facility’s production output—more than one million bumpers annually—was growing, and customers were requesting more varied styles.
First, the company installed a Bluhm label applicator employing a Sato RFID printer-encoder to create and automatically attach a label made with a UHF RFID Smartrac EPC Gen 2 passive Belt tag—with an NXP Semiconductors Ucode G2iL chip—to the inside face of each bumper, following the injection-molding process. As a pilot project with noFilis, Rehau installed a variety of RFID readers at the Feuchtwangen plant, at various points throughout the fabrication, molding and painting processes. The company used some of the plant’s existing readers, and also added Kathrein models.
Prior to the local rollout activities and physical implementation, Kathrein and noFilis conducted several read-point simulations and feasibility tests due to the site’s challenging conditions, which included the large quantity of read points that would be needed and the presence of a high volume of metal, which created the potential for RF interference since the metal could reflect the UHF signals transmitted by the readers. After the project’s successful implementation using noFilis’ middleware—known as CrossTalk—Rehau integrated its existing read points and deployed CrossTalk to other plants worldwide.
Once the system was installed, as each bumper moved through the various phases of fabrication and painting, the readers captured its tag ID number, which had been linked to the part type and serial number, along with customer information. Every time the tag was interrogated, the CrossTalk software filtered that data, and the bumper’s status was updated in Rehau’s software. The CrossTalk software provides several functions, says Patrick Hartmann, noFilis’ global sales director. First, it manages the devices and identifies whether they are operating properly, issuing alerts in the event of any problems. The CrossTalk Control Center resides on Rehau’s own servers at each site, providing several levels of response. In the event that the system identifies a problem involving a reader or other hardware, that issue can be first addressed by local IT or other support staff. If necessary, it can then be forwarded to a central second-level support department that has undergone CrossTalk training. Or, finally, noFilis personnel can respond to the problem.
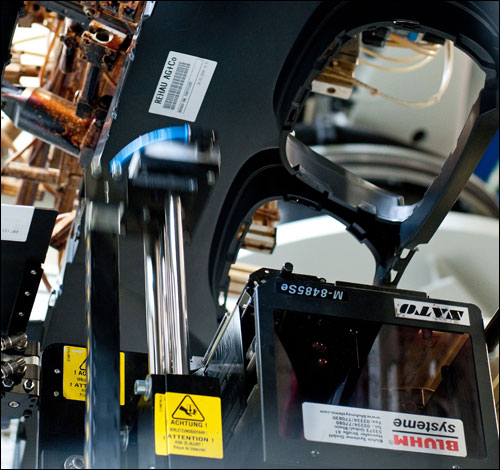
CrossTalk also provides a decentralized module, known as CrossTalk Agent—which consists of software running on a PC or the reader device itself at each read location—in order to provide local filtering of unwanted reads, as well as a view into the read events underway at that site. After filtering the raw read-point data and confirming a valid read event, the CrossTalk Agent module forwards that data to Rehau’s own management software.
The CrossTalk software is intended to remove the complexity from an RFID system, Hartmann says, by running in the background, feeding filtered data to Rehau’s own management software, and by managing and monitoring the reader hardware’s operation.
Once the system was in operation at the first plant, the company then expanded its use to bumper factories in Brake, Ingolstadt and Mosel, Germany; Györ, Hungary; Cullman, Ala., in the United States; and Port Elisabeth and East London, in South Africa.
At each of these locations, Munzert says, the installation is similar—tags are applied during the injection-molding stage, and readers are installed at each fabrication or paint station to monitor their movements. Altogether, the company has installed more than 300 readers at the eight plants. In Europe, the factories are employing Kathrein RRU4 readers, while in South Africa and the United States, they have installed Impinj Speedway Revolution readers.
With the RFID system in place, Munzert says, “daily business is much easier.” The company now knows where each item is located during the fabrication or painting process, and can thus prevent mistakes that could otherwise lead to a product for a specific order being fabricated incorrectly. “We now have transparency and can find bottlenecks,” he explains. For example, if certain bumpers are found to have scratches, Rehau’s software maintains a record regarding the stations through which those bumpers had passed. Because every worker inputs his or her own ID number upon starting each shift at a workstation, the system can also track which individuals worked on each bumper, as well as when. In that way, the company can provide further staff training, if necessary.
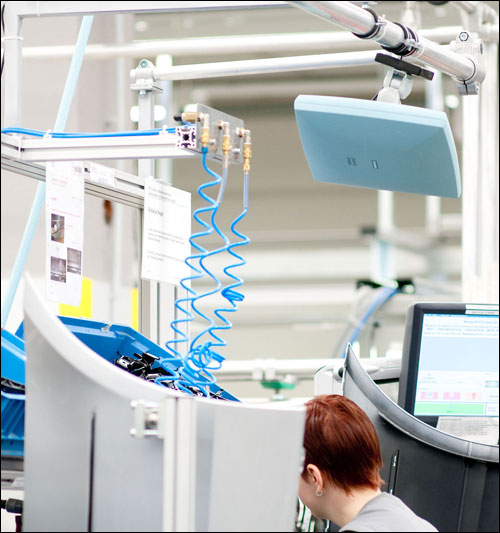
Additionally, the company is focusing on connecting Motorola Solutions Psion Workabout Pro and NordicID Merlin handheld RFID readers to the CrossTalk system, to enable data culled from those read events to be filtered by CrossTalk and forwarded to Rehau’s management software. The handhelds are being used to manage production exceptions, as well as to identify goods within the warehouse prior to their shipment to customers.
Many of Rehau’s automotive manufacturing customers are utilizing RFID technology to track their own work-in-progress (WIP), Munzert notes. As such, he says, the company is encouraging them to use the tags affixed to the bumpers for their own purposes, in order to track the receipt of goods and WIP at their own plants.