Italian packaging-components manufacturer Coster Group has boosted its daily logistics operational efficiency by 1.5 hours per staff member, thanks to a radio frequency identification solution. The technology, provided by Aton, includes passive EPC Gen 2 ultrahigh-frequency (UHF) RFID tags, Aton’s onID software that interprets read data and forwards it to the company’s Oracle system, and a mix of handheld and fixed readers. Since the system’s installation at one of its plants, the company has reduced the amount of time employees spend managing the locations of goods at that site by 90 percent, according to Salvatore Ricca, Coster Group’s purchase and ICT (information and communication technology) director. The technology was tested from 2010 to 2011 on one production line, and was taken live in 2012 on 17 production lines. The company is now extending the solution to its other manufacturing and distribution facilities.
Coster maintains seven factories and three logistics facilities (distribution centers) worldwide. The sites produce components for the packaging of aerosol, spray and dispenser products used in consumer packaged goods, as well as pharmaceutical and medical supplies. To improve its production and logistics efficiency, the company adopted a group-wide Oracle enterprise resource planning (ERP) system from JD Edwards in 1998, and automated the production process at all of its facilities. The firm began working with Aton and software firm Atlantic Technologies to develop an automated solution for tracking goods from the point of manufacture until they were shipped, in order to make the logistics process more efficient within the plant, and to provide shipping data as goods are sent from the production facility to DCs and on to customers. The company wanted to know where each individual box of goods was located, as well as the product’s history—when the goods were manufactured, where they ended up after that point and when.
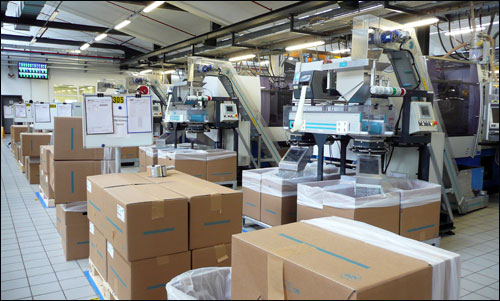
Prior to deploying RFID, the company’s operators had to input data in the system indicating which goods were being manufactured, what was being moved to storage, or being shipped, and when this occurred. The system was time-consuming for the operators, Ricca says, and prone to errors. “It just wasn’t their job,” he explains. The company wanted to free up operators to work on creating products, and to do so via automation.
Atlantic Technologies developed the management software that interfaced with the JD Edwards Oracle system. Aton served as the RFID systems integrator for the implementation, providing hardware, installation and the integration of RFID read data with the software via its onID middleware.
Coster chose to pilot the technology initially on one production line at its Coster Plant 1, located in Calceranica, Italy. The technology was installed to track a single product type: aerosol nozzles. That product line was selected, Ricca explains, because it was physically separated from the rest of the plant, and produced a limited volume of product—approximately 20 to 25 large containers, each containing 200,000 nozzles.
At the end of the production line, a Coster worker encodes an EPC Gen 2 passive UHF tag via a Datamax-O’Neil RFID printer-encoder. He or she then attaches the tag to a carton in which the products are loaded. The tag’s ID number is entered into the system using Aton’s onID middleware, which is integrated with the company’s existing Oracle JD Edwards OneWork ERP management system, says Germano Rizzo, Aton’s R&D architect of RFID systems.
A record of each carton and its products is then stored in the system, along with that tag’s unique ID. When the carton is placed on a pallet containing similar tagged boxes and moved into storage, a worker utilizes a handheld reader to indicate where the pallet of cartons was placed. Later, a staff member uses a pick list on an onboard forklift computer to identify which goods need to be picked, and where they were stored. The cartons then pass through an RFID reader portal en route to the dock doors, where they are loaded onto a truck. In the event of a discrepancy between what was ordered and what was being loaded, the Coster software issues an alert to authorized personnel, enabling them to correct the mistake before the truck leaves the plant. The software is then updated to indicate which items have been shipped, and to whom.
To date, the company has installed 17 tag printers at Plant 1, one at the end of each production line. The onID software launches the RFID tag writing and verification read of that tag, at the point at which the tag is encoded on a Datamax-O’Neil 4212 RFID printer-encoder.
The solution comprises a variety of handheld reader and tag makes and models, Rizzo says, which he declines to identify. “We tested different reading devices during the pilot and installation, and ended up with different viable solutions, all equally effective.”
According to Ricca, the system provides dramatic improvements in inventory time that personnel previously spent searching for products in order to determine where they were located, or if they had been shipped. Based on Plant 1’s efficiency improvements, the company is now expanding the system to its other plants, as well as three DCs, where employees equipped with handheld readers will also be able to interrogate tag IDs and indicate when goods were received and shipped from those locations.