Carlo Nizam is head of the value chain visibility and auto-ID program for Airbus, one of the world’s largest aircraft manufacturers. He is also a waste-buster. And like many of his counterparts in retail, health care and other industries, Nizam has discovered that radio frequency identification is a powerful waste-fighting tool.
“To tackle waste, you need to be able to measure it; you need to know where it is,” Nizam says. “But that’s easier said than done because, in reality, people have, more often than not, little data or limited visibility of how their processes are performing, so they don’t necessarily know where the waste is.”
RFID provides the insight essential for spotting hidden pockets of waste lurking inside supply chains, production lines, inventories and other key areas. The technology also helps companies squeeze out waste by automating existing processes, so they run faster and more efficiently.
“If you want to really tackle waste, you really have to take a big-picture approach, because one of the things people need to realize is that waste doesn’t differentiate between company boundaries,” Nizam says. “It flows across boundaries, and across processes.” Airbus, which began using RFID in 2005, has taken an enterprisewide approach to RFID, using the technology in its supply chain, manufacturing, assembly and in-service operations.
For manufacturers, waste in any form hampers agility, cuts into profits and reduces a company’s ability to improve or maintain its market position. RFID is helping manufacturers trim several types of waste, says Michael Liard, RFID director at VDC Research. “Most importantly, RFID technology allows a manufacturer to reallocate resources or make sure that processes are optimized,” he says.
Retailers often operate on microscopically thin margins, so detecting and eradicating waste is essential to surviving in ultracompetitive markets. Cutting waste is primarily a matter of achieving and maintaining inventory visibility, says Justin Patton, director of the University of Arkansas’ RFID Research Center. “You might want to specifically reduce theft, or you might want to specifically reduce spoilage on a particular loading dock,” he says. “But always think of your plan in terms of how the technology is going to help make your inventory more accurate and how that more accurate number will affect everything else, such as ordering and forecasting.”
Facing near-runaway costs and increasingly stringent regulatory compliance mandates, health-care organizations have made finding ways to cut waste a top priority. For many years, hospitals have defined waste primarily in terms of lost physical assets, such as misplaced, misused or stolen equipment and supplies, says Mark Norris, president and CEO of Ekahau, an RFID solutions provider for the health-care industry. “Today,” he says, “that definition has expanded to include time spent on unnecessary manual or duplicate processes and procedures, time spent looking for lost items and time away from patient care.”
Here, then, is how RFID is eliminating waste at Airbus, Lemmi Fashion, the Eastern Maine Medical Center and other businesses.
Manufacturers Boost Productivity
RFID allows both automated and manual production lines and maintenance facilities to operate at peak efficiency levels, by ensuring that materials and components always arrive at the right place at the exact moment they are needed. RFID also helps manufacturers maximize workforce productivity by shifting employees away from routine, repetitive production tasks that could be handled less expensively and more efficiently by RFID-enabled automated systems. “RFID definitely brings a higher level of automation previously not seen in a manufacturing environment,” Liard says.
In addition, manufacturers use RFID to keep supply chains humming at optimal levels by feeding an array of highly accurate data into the enterprise resource planning and data warehouse systems that drive supply optimization systems. With RFID’s help, forecasting, master production scheduling and distribution requirements planning systems all are able to produce higher-quality reports—based on accurate inventory and/or material shipping data—that can help managers better detect time- and money-burning bottlenecks.
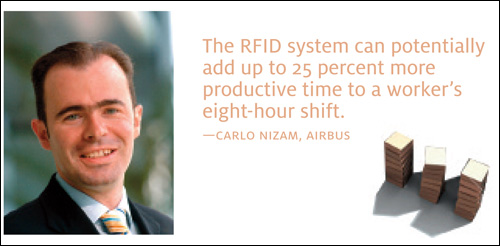
One way RFID helps Airbus reduce waste is by giving workers faster access to essential tools. At a U.K. plant that manufactures wing assemblies for A400M military transports, an RFID-based tool-management application replaced a manual system, eliminating most of the time workers once wasted standing in line simply to check out tools from a tool-storage area and return them at the end of the work shift. The RFID system can potentially add up to 25 percent more productive time to a worker’s eight-hour shift, Nizam notes. The system also automatically records the number of times each precision tool has been used, enabling management to accurately identify tools that are ready for recalibration or maintenance.
Airbus is also cutting wasted time at its Toulouse, France, assembly line, where RFID-tagged and tracked “logistics media units”—containers of various shapes and sizes—will be used to deliver components as needed to workers on the new A350 jetliner’s final assembly line. “We track when they leave the warehouse, track where they are on the final assembly line and then confirm delivery when they’re delivered to the right place,” Nizam says. The system will help ensure that production is never held up simply because a vital component hasn’t yet arrived.
In addition, RFID helps Airbus work faster and more efficiently by automating aircraft inspection and configuration-management processes. Airliners are delivered with seats and life vests installed in exact accordance with customer requirements. Just a couple of years ago, the final cabin inspection was a largely manual process, requiring clipboard-toting workers to walk along aisles, bend down to check serial numbers and write down the information—ideally, without any mistakes, Nizam says. “It used to take a person 14 hours to do that on what we call a long-range aircraft, which are our A330 and A340 families,” he says.
Now that Airbus has added RFID tags to the seats and life vests, just one person carrying a lightweight handheld reader can complete the cabin inspection for an entire airliner in approximately 26 minutes. The system automatically confirms the presence of each required item, verifies its location and then looks up critical data associated with the part, such as its “birth record” and expiration date. “This information can then be used to determine the aircraft configuration and also in-service later on, to prioritize maintenance planning for items due for inspection, overhaul or replacement,” Nizam says.
Unlike Airbus, Lemmi Fashion, in Fritzlar, Germany, doesn’t operate a series of massive manufacturing plants. The children’s clothing designer prefers to outsource production to Asian contract manufacturers. Yet, Lemmi still uses RFID to cut waste, relying on the technology to automatically check incoming shipments for correct quantities and styles.
Götz Pfeifferling, Lemmi’s CIO, says that prior to adopting RFID, the firm often found significant discrepancies between the number and types of garments that manufacturers claimed they had shipped and the items that actually arrived at the company’s distribution center, “especially when it came to the sizes and colors,” he says. “On a SKU basis, our data was very, very rough in relation to the shipments.”
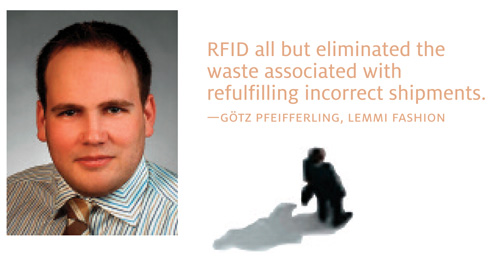
By requiring its manufacturers to tag their shipments, Lemmi was able to eliminate a tedious manual verification operation, reducing wasted time and allowing employees to focus on more productive tasks. “We also implemented packing tables and readers at our manufacturers, so when they packed the goods we would actually get a detailed inventory on each carton,” Pfeifferling says. The approach gave Lemmi a four-week heads-up on incoming shipments, allowing the firm to head off any problems and better coordinate deliveries to its retail customers.
At Lemmi’s warehouse, the tagged shipments eliminated a major source of wasted time. “Previously, we mostly had to do manual counting, then type the totals into a computer,” Pfeifferling says. “This process was slow, and it was very easy to make mistakes.” Accuracy rates under the manual system never surpassed 85 percent, and may have actually been worse, he notes.
The RFID system provides virtually perfect accuracy. “It streamlined our receiving process, making it much quicker to add items to our warehouse,” Pfeifferling says. The technology also assured that Lemmi retailers would always receive the exact garments they had ordered, all but eliminating the waste associated with refulfilling incorrect shipments.
Retailers Stay Competitive
Comprehensive RFID-driven inventory visibility and management capabilities help retailers maximize sales. “If a retailer loses sales due to an out-of-stock situation, that must be considered waste,” says Joerg Niederhuefner, director of business development for Intelligent Loss Prevention, a company that sells RFID-enabled merchandising systems. “False data can also create overstocking, which also must be defined as waste.”
Apparel retailers worldwide are employing RFID to slash waste attributable to inventory miscounts, stock shrinkage and other factors. Swiss fashion retailer Charles Vögele was an early adopter, deploying an RFID system in 2008 to track items from manufacture to its stores. The solution quickly justified its cost by generating a 70 percent or more time-savings when calculating store and warehouse inventories, as well as a 7 percent increase in the accuracy of picked orders in factories. It has resulted in increased sales, due to fewer out-of-stock items, and more accurate planning information.
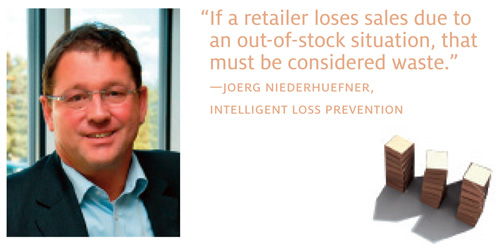
In 2011, Valdac Group, a São Paulo-based fashion retailer that operates more than 100 stores throughout Brazil, turned to RFID to trim waste. For its Memove chain, the firm created an RFID solution designed to save time at the distribution center and inside each store. It improves shipment verification, because employees know exactly what products, including which sizes and colors, are inside each of the boxes they receive. The solution also helps stock replenishments keep pace with sales, which increases revenue and prevents customer disappointment.
Jewelry retailers are also adopting RFID to improve inventory management. In 2009, Cleor, a French retail jewelry chain, began deploying RFID because its sales staff was spending more time on inventory than on sales and customer service. Today, the solution has been deployed at 50 retail locations. “The solution’s greatest value has been in improved accuracy,” says COO Aurélien Sénéchal. “It has reduced errors in shipping and receiving.” An inventory check that used to take several days now takes only a few hours, he says.
The RFID system that Borsheims, a Berkshire Hathaway-owned jewelry retailer in Omaha, Neb., deployed in 2012 has already paid for itself, says CFO Erin Limas. Tagging and tracking high-value jewelry reduces the amount of time required for inventory counts, eliminates shrinkage and provides better control over store inventory.
Supermarkets and other grocery-oriented merchants face a unique challenge among retailers: products with shelf lives that are measured in terms of days or weeks rather than months or years. Food retailers have an opportunity to use cold-chain monitoring and other types of RFID systems to ensure food quality and prevent spoilage. “Produce and meat are what generally draw people to stores and are what makes a good grocery store or a bad grocery store,” Patton says. “If you ask most grocers what their problems are with waste and loss, they’ll generally identify spoilage, damage in the back room and then theft.”
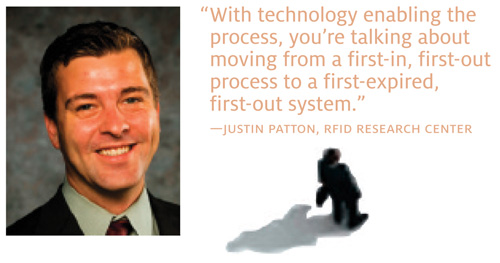
Inventory insight and seamless control are key to addressing all of these challenges, Patton says. “With technology enabling the process, you’re talking about moving from a first-in, first-out process to a first-expired, first-out system,” he notes. “Instead of just making decisions based on when the truck came and dropped this off, you’re now making decisions based on which of these shipments has the most time left before it spoils.”
For food merchants, waste reduction can also be turned into a powerful tool for building market share. “If you’re using RFID or some other type of supply-chain technology to ensure that you’re getting better quality, or to remove the bad-quality items, you’re potentially differentiating yourself from others in the space,” Patton says.
Hospitals Meet Health-Care Challenges
Time is an asset all health-care organizations strive to use more efficiently. “More time allows hospitals to elevate the patient experience, shift resources to innovative care-giving models and more effectively allocate staff time to impactful activities,” Ekahau‘s Norris says. While hospitals, clinics, emergency-care centers and long-term care facilities continue to consider real-time location system (RTLS) technology a way to help managers spot and eliminate the waste that occurs when assets go missing, new time-oriented applications are also appearing. “RTLS technology helps automate health-care delivery, and this leads to quicker feedback on procedures, admissions, discharges, room availability and asset inventory,” he says.
Slashing wasted time equals saving money, says Brenda Clements, manager of nursing services at Eastern Maine Medical Center’s Cancer Care department in Brewer, Maine. “Shuffling patients via paper is very inefficient, and there’s a good chance of losing that piece of paper and creating long patient delays,” she notes. The facility began using an RTLS for patient and employee tracking in 2009, and Clements says process improvements followed quickly. “We are able to expedite patient flow, lean processes, and improve patient and staff satisfaction,” she says. “Now, we’re able to see where all our patients and coworkers are at any given moment.”
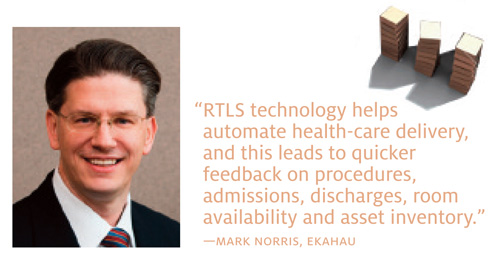
An RTLS can generate reports that help managers maintain close oversight over anything—or anyone—tagged within the hospital environment. “We can see where bottlenecks occur,” Clements says. “If I have complaints that patients have been kept waiting for a long period of time, I can track the patient flow—where they waited, how much time they spent there—and see if I can flush out process issues that created the patient delays.” The system has already saved the hospital time equivalent to that of three full-time employees as well as “miles of walking” for staff members, Clements notes. “Step minimization equals increased efficiency, dollar savings and more time spent with patients,” she says.
The RTLS also helps the hospital cut waste in other ways. “Maintaining multiple waiting areas where patients can sit can be a waste,” Clements adds. “Requiring extra resources to facilitate patient flow is a waste; patient delays that subsequently delay providers is a waste.”
Indeed, hospitals worldwide are deploying RTLS solutions to better manage patient care. England’s Royal Wolverhampton Hospitals NHS Trust, for example, deployed an RTLS solution to improve patient flow, as well as manage assets and ensure hand-hygiene compliance. India’s Fortis Escorts Heart Institute is using RFID to reduce wait times for the roughly 300 outpatients that visit the medical facility daily for testing. And at Malaysia’s Pantai Hospital Ipoh, which has a rapidly growing local population and a chronic skilled labor shortage, RFID automates routine tasks so nurses have more time to focus on patients.
In the United States, health-care facility waste and inefficiency can also negatively impact Medicare and Medicaid reimbursements. The federal government’s Centers for Medicare & Medicaid Services agency is now basing reimbursements partially on patient satisfaction, Clements says. “If we can be lean, and we can be efficient, and we can get our patients through services in a timely fashion, minimizing their wait time, they’re going to be happier,” she says.
No Opportunity Wasted
Manufacturers like Lemmi have succeeded in cutting waste by focusing on the processes that generate the most waste, Liard says. “Businesses really need to evaluate what their processes are, what costs are tied to these processes and how an automatic identification technology such as RFID can help alleviate some of these pain points,” he explains. “It starts with a review of one’s processes, and then moves to assets and then to people—they’re all intertwined within a manufacturing environment.”
Retailers, regardless of the market they serve, can build a waste-busting RFID system to achieve visibility and control, Niederhuefner says. “Make sure you have a good understanding of all the positive impacts RFID can have on your business model, but prioritize which segments of your business would benefit most from RFID deployment,” he says. “Define which level is most important and start there.”
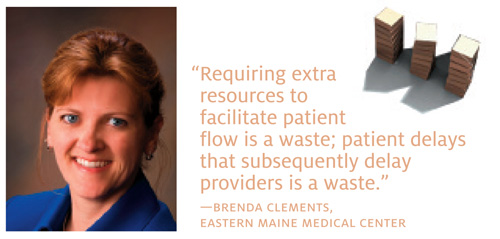
RTLS is becoming the go-to solution for health-care business intelligence, “providing insight and analysis on what works and what doesn’t, giving hospitals the information they need to make smart decisions in areas of staffing, resource planning, patient workflow and process improvement,” Norris says. Rich RTLS-generated data helps health-care organizations better understand how to reduce costs and drive more revenue. “Underutilization of time and resources remains one of the health-care industry’s biggest challenges,” he says, “and RTLS can help the health-care industry address this challenge with location awareness.”
Airbus’ Nizam offers one last thought on eliminating waste. “There’s an old saying: The bolt is only tightened on the last turn, and everything else is just movement,” he says. “There are many things we’re doing to try to minimize all that movement inside the company. The use of RFID is helping us focus and make sure we’re only doing the things that need to be done.”
More Waste-Busting Applications
RFID Journal’s annual conference and exhibition will feature more than 50 end-user case studies, including many that focus on eliminating waste. Here are some highlights.
Bloomingdale’s has been RFID-tagging items to improve inventory accuracy, reducing overstocks and understocks. Roger V. Blazek, the company’s VP of shortage control for omnichannel, will deliver a keynote address on the retailer’s RFID journey from concept to rollout.
American Apparel has RFID-enabled roughly 100 stores. Stacey Shulman, the company’s CTO, will speak about how the clothing manufacturer and retailer uses RFID to improve inventory accuracy and reduce shrinkage.
TAP Portugal, the country’s national airline, uses RFID to track engine-overhaul components and tools. Fernando Matos, head of information technologies at TAP Maintenance and Engineering, will discuss how the solution improves visibility into its parts and tools, and eliminates the need to conduct time-wasting manual inventory searches.
Speedy Services developed an RFID-enabled onsite mobile equipment pod that provides workers with continuous access to tools, to help crews meet schedules. Glyn Matthews, Speedy’s senior project manager, will explain how the solution eliminates waste for the tool-rental company and its customers.
Celebration Health, a Florida Hospital facility, deployed a real-time location system to reduce the many miles nurses typically walk during a shift. Todd Frantz, associate CTF, will detail how the solution improves efficiencies at its new patient tower.