Arab Paper Manufacturing Co. (also called Waraq), located in Dammam, Saudi Arabia, has launched an RFID-based system to manage the location and movement of every roll of paper stored and accessed within its warehouse, and to ensure that the correct product is loaded with the right shipment. The technology is expected not only to prevent costly shipping errors, but also to lower labor costs previously incurred as employees attempted to locate and visually identify rolls of paper prior to shipment.
The solution is provided by Tanweer United Co., an RFID technology solutions company based in Jeddah.
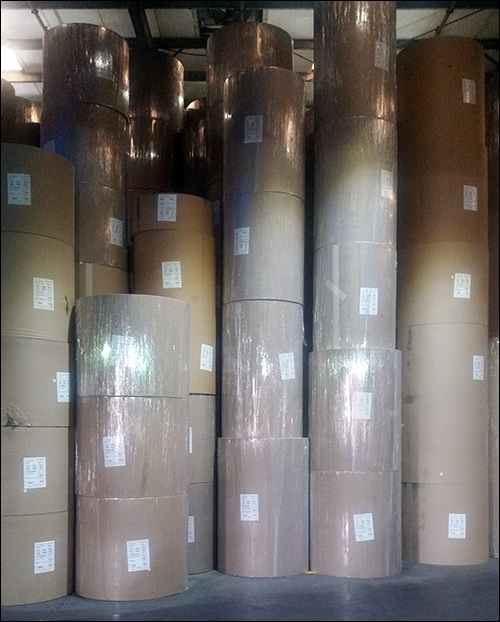
Waraq manufactures industrial paper used in corrugated cartons and packaging, as well as textile bobbins and paper tubes for a variety of applications, for customers located throughout the Middle East and worldwide. Customers require different types of product, including varying stock and weight, so Waraq makes a large number of types of paper, which is rolled on spools and then stored at its facility until customers’ orders are received.
The management of these paper rolls can be a complex process, reports N.P. Suneer, a senior infrastructure officer at Waraq. Although the papers vary in type, they tend to look the same, and there are thousands of rolls, stacked throughout the facility, in three different warehouses, each measuring about 80 meters by 150 meters (262 feet by 492 feet). Some spools are too high for staff members to manually reach so they can read printed descriptive information or scan a bar code, Suneer explains. “Usually, the stacking of rolls can be up to four levels, which will be around 7 to 8 meters high,” explains Praveen Perumal, Tanweer United’s technical architect for RFID designs and solutions. “Bar-code scanning is not possible for this scenario.” In addition, the rolls themselves can weigh 1.5 to 2 tons apiece.
Prior to the RFID deployment, when orders were received, workers had to manually search through the inventory to find the correct roll, then transport it by forklift to the loading dock and load it onto a vehicle destined to a port where it could then be shipped to the customer. If a roll of paper is shipped to the wrong customer, the resultant shipping costs, delays for that customer and drop in customer satisfaction can be high.
The solution that Waraq now uses, Perumal says, consists of an ultrahigh-frequency (UHF) RFID reader and two antennas mounted on each forklift, as well as tags on each paper roll and Tanweer United software to manage the collected read data.
When a new roll of paper is produced at the Waraq plant, a tag is applied to it. The tag’s unique ID number is linked to that roll’s product type, manufacturing date and serial number in the Tanweer United software, which can be integrated with Waraq’s own enterprise resource planning (ERP) software. The finished roll must then be placed in storage. A forklift driver is equipped with a Zebra Technologies FX9500 reader, as well as a Microsoft Windows 10-based tablet that displays the Tanweer United software data.
When a forklift driver picks up a roll, the reader antenna mounted on the front of the vehicle captures the roll’s tag ID number and forwards that data to the software via a Wi-Fi connection, while the tablet on the forklift displays information about that roll. Throughout the facility, Tanweer United applied locator tags in the floor. Each of these UHF RFID tags is encoded with an ID number linked to a specific location. The second reader antenna on the forklift, which faces the floor, reads the RFID tags as the vehicle passes over them. As the driver deposits the paper roll at the proper warehouse location, as instructed by the software (viewable on his or her tablet), the software links the locator tag at which the roll is unloaded with the paper roll’s RFID tag, thereby creating a storage location in the software.
When a customer places an order for a specific roll of paper, the forklift driver will see the picking order on the tablet display, along with that specific roll’s location within the warehouse. He or she then proceeds to that location and picks up the roll, and the reader interrogates the roll’s tag ID and confirms that action in the software. The roll can then be staged at the loading dock.
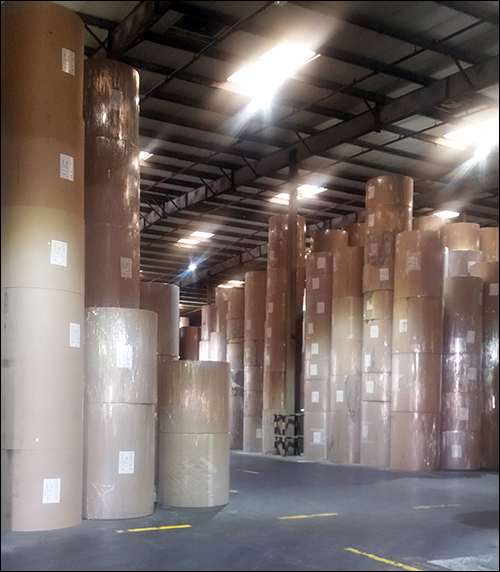
When rolls are placed onto trucks, the software provides a further step for personnel to ensure products are being loaded accurately. Workers at the loading area, equipped with Alien Technology handheld readers, can read each roll’s tag ID after it is loaded, and can also view whether an error is being made before the vehicles leaves with the wrong product aboard. In addition, Perumal says, “Managers can walk around the truck with a handheld reader” and view all loaded products (10 to 15 rolls are typically loaded onto each truck).
The RFID system not only provides automated data collection, Perumal explains, but also spares workers from the safety hazards of having to climb around the rolls to confirm their identity during or after the loading process.
Suneer indicates that the solution, installed a month ago, has reduced labor hours and the costs related to that labor. “Forklift users need to easily scan the RFID tag on the rolls without much strain,” he states.
The company plans to test the technology for approximately six months, Suneer says, adding that during that time, “We expect the production capacity and dispatch will increase in [the next] few months.” Once the six-month pilot concludes, the company intends to review the results and determine where to permanently deploy the technology.