When Littleton, Co., valve distributor and service firm ProTech Sales began its contract 18 months ago with Anadarko Petroleum Corp., to provide maintenance and inspection services for its more than 5,000 valves, the company received a list of each valve’s identification, along with its records in the form of a stack of papers, written in pen. The handwritten papers would need to be manually entered into a Microsoft Excel spreadsheet, and inspectors would later, on paper, need to track everything that they did involving each valve.
The business has historically run this way, says Carol Arnim, ProTech Sales’ project manager. For this large contract, covering two sites spanning a combined total of more than 1,000 square miles, ProTech opted to create an automated solution comprising passive EPC Gen 2 ultrahigh-frequency (UHF) RFID tags and handheld readers, as well as software provided on a cloud-based server to interpret read data, and to make that information available to both ProTech and Anadarko. Since that system’s launch in September 2011, the company now offers the RFID-enabled inspection service to other customers, and is applying RFID tags to all valves that it rents to petrochemical companies.
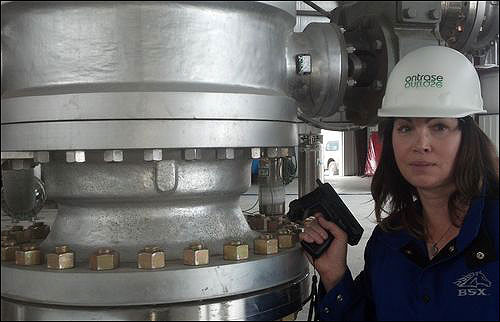
Valves on pipes that carry petroleum or chemicals must be inspected annually, and be properly maintained to ensure they function correctly. A valve failure can cause significant problems for a petrochemical company, since it may require shutting down operations until that valve can be replaced. In addition, government agencies, such as the U.S. Department of Transportation, require that businesses provide a record of regular inspections for any valves located on public land that they oversee.
Using the manual paper-and-pen method, inspectors walk or drive to each valve, complete an inspection and any necessary maintenance work, and write notes beside that valve’s serial number. Those notes are then taken to the office to be entered into a spreadsheet. However, the company reports, notes can be incomplete, difficult to decipher or hard to locate when required in the future. What’s more, the valves themselves can be difficult to find; inspectors use the notes and a map to determine a particular valve’s location.
The solution is a Xerafy MicroX II RFID tag attached to each valve. ProTech attached the tags to all 5,000 valves on Anadarko’s two oil fields—one located in Brighton, Co., the other in Salt Creek, Wyo.—via an epoxy adhesive.
“Our timing was impeccable,” Arnim says, noting that by 2011, tags had been developed to work effectively on metal. In fact, she adds, the MicroX II tag’s read range is long enough that inspectors or other system operators could interrogate a tag overhead that may be located many feet in the air. The Xerafy tags not only are rugged and function well on metal, she says, but “they can withstand temperature swings between -40 degrees and +482 degrees Fahrenheit [-40 degrees and +250 degrees Celsius].” The long read range, she reports, was an important consideration as well, providing access to valves located aboveground and potentially out of inspectors’ reach without using a lift.
To manage the collected read data, ProTech designed a solution known as Ontrase, using software provided by idsTAG. The software interprets data from each RFID read, links that read event with information input on mobile devices, and then stores that data.
ProTech’s and Anadarko’s staff members are equipped with ATID AT870 handheld readers and RFID-enabled laptops. Typically, when first attaching the tags to valves onsite, ProTech’s employees used the laptops with a SkyeTek SkyeReader SR70 USB RFID reader attached to it. It was easier for the staff to use the laptop—with its keyboard and larger screen—for this task than it would have been using a handheld reader.
Workers held each tag over the SkyeTek reader to capture its unique ID number, and then entered other details about that valve, such as its serial and lot numbers, its years in service and its GPS location. For future inspections, Arnim says, the maintenance staff are more likely to utilize the ATID readers to interrogate the tags, since they are more mobile than a laptop, and to then follow prompts in the Ontrase software (loaded onto that handheld) to indicate which services they are providing.
As the handheld reader captures the tag’s ID number, it can forward that ID, via a GPRS or Wi-Fi connection, to the Ontrase software running on its cloud-based server. If no GPRS or Wi-Fi service is available, the data is stored on the handheld, to be later loaded into the system. Users indicate when they are commencing an inspection or maintenance cycle, when they finish, and the type of service provided. In that way, Anadarko and ProTech can view, in real time, which valves are being maintained, the method used and how long it takes to complete the task. The software also allows for business analytics, such as determining which valves are faster to maintain, which require a greater amount of maintenance and the dates on which valves need servicing.
In terms of the solution’s benefits, Arnim says, “I think there’s a level of accountability that RFID provides,” since the technology can track which specific service has been provided to each valve. With the system in place, she says, both ProTech’s inspectors and Anadarko will have a greater understanding of each valve’s conditions and maintenance history.
Next month, Armin reports, ProTech plans to undertake its first full valve inspection for Anadarko since the RFID technology’s installation. In addition, ProTech has been tagging its own valves, so that it can offer interested customers access to real-time data regarding each valve, as well as track its own staff’s work. ProTech also offers the solution to companies that may wish to use it to perform their own equipment inspection and maintenance servicing. The firm provides a variety of handheld readers, including ATID’s AT 570 and AT87 models, as well as an RFID-enabled version of Motorola Solutions‘ MC9190-G reader.