When Gruma Corp.‘s Mission Foods subsidiary decided in 2009 to replace the disposable corrugated boxes it was using to ship products with reusable plastic containers—and to deploy a radio frequency identification system to track those containers at its Dallas, Texas, warehouse—the goal was to reduce packaging costs and improve warehouse management. Today, the RFID solution has not only fulfilled those business and operations objectives—it also has met Gruma’s corporatewide green initiative.
Mission Foods is one of the world’s largest producers of corn flour and tortilla products, providing nearly one-quarter of all tortillas sold throughout the world. It also manufactures wraps, salsas, snacks and other food products. The company operates production plants throughout the United States, as well as in Europe and China. Food products come into the company’s 34 U.S. warehouses and plants from its manufacturing sites, and go out when Mission Foods’ independent distributors pick up orders.
|
The company was shipping tortilla chips and other light food products in corrugated boxes that cost $1 apiece. “We were basically throwing a dollar away,” says Eduardo Valdes, VP of management information systems at Gruma, in Irving, Texas, because the box was used only once. Mission Foods was purchasing nearly one million boxes annually for just its three Texas facilities, he says. Including all its U.S. locations, Mission Foods was spending more than $5 million per year on the boxes.
In addition to cost, Mission Foods managers were well aware that the corrugated boxes, which ended up as waste, were negatively impacting the environment. “The major environmental issue our company was trying to address was the lack of recycling and sustainable culture in our manufacturing plants and warehouses,” Valdes says.
Management decided to replace the corrugated boxes with plastic containers, to save money and promote recycling. The reusable containers cost approximately $7 apiece, and the company estimated it needed to use each one roughly eight times to break even. But there was a hitch. The company was already using plastic containers to ship heavier products, and a number of those containers were often lost in transit.
To ensure the move from corrugated boxes to plastic containers would be economically feasible, Mission Foods decided to deploy an RFID system to track when containers were shipped out and returned to company facilities. “We were looking for a system that wouldn’t create extra work for our warehouse personnel,” Valdes says, “something that would follow the natural picking and shipping process.”
An Idea Takes Root
Mission Foods set up a cross-functional team—including representatives from information technology, logistics, procurement, sustainability, quality assurance, manufacturing and sales—to evaluate RFID tracking systems and select the new plastic containers. The company had a relationship with Intermec and decided to work with the RFID systems vendor, which supplied the hardware and helped develop and test the system.
During the planning process, Technology Container Corp. (TCC), which Mission Foods chose to supply the plastic containers, conducted a study of the economic and environmental savings the food supplier could expect by eliminating the use of corrugated boxes at all its U.S. facilities. TCC determined that over a five-year period, Mission Foods would save approximately $15 million, decrease energy consumption by 91 percent, cut solid waste by 98 percent and reduce greenhouse gases by 90 percent.
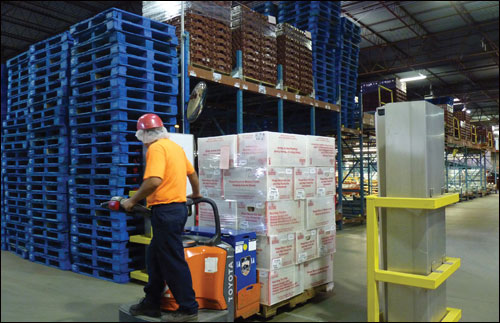
It took roughly seven months to develop, test and implement the system in the Dallas warehouse. The solution includes two types of passive Gen 2 RFID tags, both from Avery Dennison—one with a permanent adhesive to apply to containers, the other with a regular adhesive to temporarily apply to pallets used in the warehouse. Workers rely on an Intermec RFID printer to encode the labels. The permanent labels are sent to TCC, which applies them to the containers before shipment to the warehouse.
Three fixed readers are placed strategically within the 150,000-square-foot warehouse: One is near the shipping area, where forklift drivers exit the facility on their way to the trucks; a second is near the receiving area, where drivers return empty trays after use. The third is in the middle of the warehouse and used for both shipping and receiving when traffic is high in the other areas.
Workers pick packaged food products and place them in the RFID-labeled plastic containers, which are then loaded onto pallets. An RFID tag encoded with an independent distributor number and an order number is applied to each pallet. The reader software, developed by Intermec, associates the pallet number with the container number.
The pallets are loaded onto a forklift and driven to the shipping area. Before being loaded onto trucks, they move through the RFID portal and a reader records both the pallet and container numbers. When the trucks return to the warehouse, the containers are processed through an inbound portal to reconcile them per route.
The RFID data is organized by plant, customer, product, date, container type and other parameters. The information is transferred once a day to an SQL server, then processed and added to a database for reporting purposes. Mission Foods develops reports using Microsoft‘s SQL Server Reporting Services, a server-based reporting platform; these reports enable the company to keep tabs on which independent distributors are receiving containers from its warehouse at a given time, and which are returning them. “Since every reader has a unique IP address, we know where the containers were read and if they were leaving or coming back to our plant,” Valdes says.
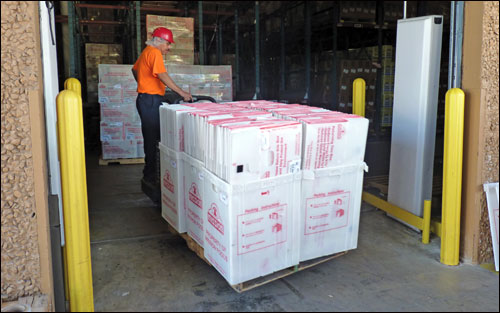
Mission Foods had to overcome several challenges during its RFID implementation. The IT department and Intermec tested various tags, as well as ways to place them on the containers to achieve the highest read rates. They first tried rigid tags, but these were expensive and difficult to install, Valdes says. The vendor then recommended tags that are weather-resistant and feature an adhesive that gets stronger and tougher to remove over time.
The company also struggled with identifying good reads from bad ones. For instance, if a container was near an area where a reader was placed, the reader might recognize the tray as having passed through the portal even though it was still in the warehouse. To resolve this, the company had to build a logic capability into its reports, so if a tag is read multiple times within a short period of time, managers could ignore the reports of a container leaving or entering the warehouse.
A Mission Flourishes
The RFID system was deployed in June 2009 in the Dallas warehouse. After analyzing the pilot results, Mission Foods rolled out the system, in December, to its Houston and San Antonio facilities. It cost approximately $100,000, including readers, tags and software, to RFID-enable the three warehouses. With the new tracking capability, Mission Foods managers now can determine at any time which of the company’s independent distributors are taking shipping containers from the warehouse, and when they are returning those containers. Mission Foods has been averaging 20 turns per container, and estimates it has saved nearly $700,000 by eliminating the corrugated boxes.
“Just in the first year in the state of Texas, we eliminated the use of 1 million boxes,” Valdes says. This not only helps the environment, he says, it also meets Gruma’s corporate responsibility program, called Today’s Mission for a Better Tomorrow.
Mission Foods plans to deploy the RFID system at all its other U.S. warehouses and plants—in Arizona, California, Colorado, Georgia, Minnesota, Oregon, Pennsylvania, South Carolina and Washington—by the end of 2012.
Currently, the company is exploring ways to leverage its RFID infrastructure. It’s considering, for example, replacing wooden pallets with RFID-tagged plastic ones. In addition to improving tracking, plastic pallets are considered more environmentally friendly.
To learn about this year’s other winners, see 2011 RFID Journal Awards: Excellence in RFID.