Indian stainless steel manufacturer Viraj Profiles has reduced its stock-taking time from 12 hours to just one hour, and has also improved the visibility of its inventory to 99 percent, following the introduction of radio frequency identification.
Viraj, which manufactures a variety of shaped stainless steel pieces (profiles), ranging from 20 millimeters to 150 millimeters (0.8 inch to 6 inches) in width, wanted to gain visibility regarding which profiles it had in stock, as well as improve the speed and accuracy with which those profiles were retrieved, prevent mistaken shipments and reduce labor costs.
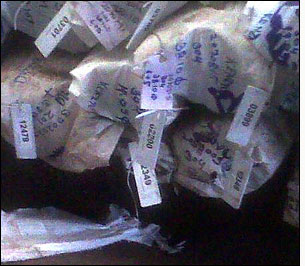
The steel profiles are packed in bundles that weigh up to half a ton each. Viraj’s managing director, Nitan Chhatwal, says that previously, each bundle was marked with a manually written code and placed in the warehouse in stacks of more than 150, depending on space availability. Employees manually searched for each bundle using a printed list. This created a labor-intensive search and retrieval process, and human error sometimes led to the wrong bundles being shipped to clients, thus resulting in customers refusing to accept the shipments.
According to Chhatwal, with exports to more than 80 countries, from multiple manufacturing facilities and warehouses, Viraj Profiles believed it was vital to improve its operational efficiency.
“The goal of RFID was to determine the precise location of bundles in the warehouse, faster retrieval of bundles, zero mismatch during retrieval, faster movement of inventory and a reduction in labor costs,” Chhatwal explains.
Indian-based technology provider Vicinity RFID was chosen to develop the system. The company first conducted a small trial involving approximately 50 UPM Raflatac ShortDipole EPC Gen 2 passive ultrahigh-frequency (UHF) RFID inlays and a Psion Teklogix Workabout Pro 7527C G2 handheld computer with an RFID interrogator. Challenges included determining the best point at which to tag the bundles, as well as designing a solution in such a way that it could be easily used by the primary workers, such as loaders who pick and place the bundles in the warehouse, who might not be familiar with the technology.
Vicinity’s director, Anandkrishnan, says that after the trial, the next step was to divide each location within the warehouse into individually tagged zones. Upon arrival at the facility, each bundle is tagged with a UPM Raflatac RFID label encoded with a serial number that is also printed on the surface for visual identification.
“The tag number is associated with the bundle and updated in the SAP system,” Anandkrishnan states. “When the bundles are received at the dispatch warehouse, they are stored according to availability, and using the handheld reader, staff can scan all the bundles across each zone and map them.”
Upon docking the handheld reader, Vicinity’s VRIF middleware for warehouse and inventory management synchronizes the stock details to the company’s server. Based on the orders received, the packing list provided by the existing SAP system is then updated by the middleware, with additional information such as location details and serial number.
“An Excel sheet containing certain parameters for each bundle, including the serial number, would be supplied to Vicinity VRIF middleware,” Anandkrishnan says. “The information would be received on a periodic basis, or at the end of the day. The tag record would now include its associated bundle number, status and the zone in which it has been received.”
With the packing list including up-to-date location details and serial numbers for each bundle, the shipment of steel profiles was both accelerated and more accurate, Anandkrishnan notes, with electronic proof of dispatch provided upon departure.
Some 20,000 RFID tags, as well as six handheld readers, are being utilized in the current project. According to Chhatwal, the benefits have been immediate, with a return on investment in just six months. Through the use of RFID, he says, Viraj Profiles has improved its inventory visibility to 99 percent and increased dispatch by 20 percent, while experiencing no incorrect shipments. There has also been a reduction in labor costs, because inventory can now be conducted in just one hour, whereas one employee took 12 hours using the previous manual system.
The steel industry has started to use RFID in a number of ways. ThyssenKrupp Steel, one of the world’s largest steel companies, completed a pilot in which it tagged 1,000 steel slabs and tracked them from Brazil to Germany (see ThyssenKrupp to Use EPC UHF Tags to Track Steel). And South Korean steel manufacturer Posco used ultra-wideband (UWB) RFID tags and interrogators to create a real-time location system (RTLS) at its steel mill, in order to reduce accidents and improve employee and visitor safety (see Posco Steel Mill Improves Safety, Energy Conservation).