A number of South African gold mines are employing an RFID-based tracking system known as Oretrak, provided by RF Tags SA, to ensure that extracted material is not misrouted during the mining process. Goldfields, Harmony Gold Mining Co. and AngloGold Ashanti are all utilizing the system, while the Amplats Group is currently installing it.
Tracking gold ore (also known as reef) can be a monumental task in large mining operations. Goldfields’ Driefontein mine, in Gauteng, South Africa, for instance, produced 1.1 million ounces of gold from 6.8 million tons of ore in the 2005-2006 financial year—with approximately 13 tons of ore per minute hauled from a number of shafts. In smaller mines, the tunnel network can extend to 17 miles in length, while larger mines may have a total of almost 300 miles in tunnels, along with thousands of workers.
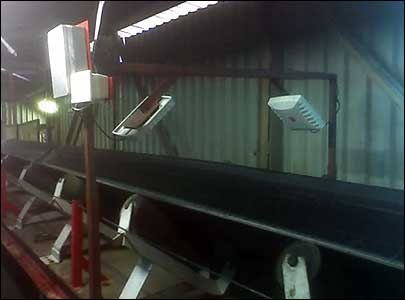
When material is blasted at a mine and removed from a shaft, it typically travels through a complex transport system comprised of “ore passes” (underground trains), belts and trucks. A skip—a bucket that carries tons of material—is usually employed to transport the rock to the surface, where the ore is sent to one location for processing, while the rest of the material (rock containing no ore) is diverted to another location as refuse.
With such a large volume of material coming from the mine at any particular time on belts moving continuously at a rate of 3 miles per hour, however, it is impossible for a worker at the mine’s surface to visually determine what is gold ore and what is waste—and to direct the material to its appropriate destination. As a result, it’s common for large mining operations to erroneously identify some ore as refuse to be discarded, while sending some waste to be processed as ore. Such mistakes, known as “cross-tramming,” can be costly.
Traditionally, mining officials have used a system involving metal washers or balls imprinted with ID numbers and thrown in with material they wish to monitor—either ore or waste. When an official identifies a vein of gold, for example, its footwall is prepared for blasting and a washer or ball is placed at the site. After blasting, the broken rock, along with the ball or washer, is removed. As the material moves up the mine shaft, it passes a large magnet that pulls the washer or ball from the rubble, alerting employees that the material they wish to monitor has arrived at the surface.
To identify the material, however, a worker must read each washer’s ID number and check it by comparing it with a printed list of all the washer IDs, or by entering each number into a computer system. What’s more, the rate at which the washers or balls are actually retrieved and identified can be as low as 3 percent, either because they simply don’t get captured by the magnets, or because the numbers written on them are illegible.
With the Oretrak system, says John McMurray, RF Tags’ engineering manager, 915 MHz semi-active, disposable RFID tags complying with ISO 18000-6C are utilized instead of metal washers or balls. The tube-shaped tags measure about 8 inches in length. In such a scenario, the official identifies an area for blasting and uses a pen and paper to record the location.
When the official returns to the surface, an Oretrak RFID tag is interrogated and its ID number is entered into a database containing that individual’s name, the location and type of ore or material, and the time and date. The mine location number is hand-written onto the tag’s black surface using a white pen, and the tag is then taken into the mine and placed at the blasting site indicated by the location number. According to McMurray, the system does not yet employ handheld readers for inputting mine wall locations because the dark, cramped and dusty conditions in the mine do not lend themselves to carrying and operating handheld devices.
Interrogators and antennas installed above conveyor belts in the mine shafts, as well as at the surface, can capture the unique ID number on the RFID tag as it is transported with mining material back to the surface, then transmit that data to a back-end system, notifying the company where specific material has gone. Information from the reader can be sent to the back-end system via a cabled or wireless connection using Wi-Fi, ZigBee or GSM/GPRS. If the tag data indicates an instance of cross-tramming—either in the shaft or at the mine’s surface—the system can alert the office staff, informing them that material has been transported in the wrong direction.
Each interrogator can store up to several months’ worth of data if necessary, McMurray says, to be retrieved at a later date. This ensures that should communications be lost, for example, due to a rock fall damaging cables leading to the surface, no data would be lost. The Oretrak system software also enables self-diagnosis, allowing a user to display a map of every reader on the installed Oretrak system and its status. In the case of large mines with multiple wireless readers, one interrogator can act as the mesh network node to host a large number of readers communicating with it.
Data from the Oretrak system is stored in the mine company’s back-end database (usually SQL), including the data inputted when the tag was first read, as well as the time, date and location for every instance the tag was interrogated, the belt it was read on, the type of material being transported and the belt it should travel on.
“Our first mine—Masimong Mine—claimed a saving of 1,000,000 rands ($138,000) in a month against a capital cost [of the system] of under 100,000 rands ($13,800),” McMurray says. Masimong Mine, part of the Harmony Group, has been using the Oretrak system since February 2006. Amplats intends to go live with a similar system at the end of May.
Mines use between two and eight interrogators, some mounted at shaft openings, others at waste belts, and others for issuing tags.