Nokian Tyres is employing an RFID system to track the components of the tires it makes at its plant in Nokia, Finland. The system, provided by Trackway, utilizes both RFID tags and bar-coded labels to provide the tire manufacturer better management of its assembly area as treaded rubber is distributed to assembly lines.
Nokian Tyres began working with the Tampere University of Technology in 2005 to draw up initial plans for an RFID-based system that would better manage the movement of treaded strips of rubber sent to assembly lines for specific tire assembly. Armed with those plans, the company then started seeking vendors of RFID technology.
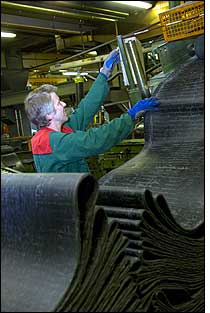
The problem the company was attempting to solve involved getting the correct materials to the right assembly lines on time, without developing a backlog at any particular location. Nokian Tyres has 27 assembly lines, so space on its factory floor is limited. If the system works properly, tire treads, wound onto wheeled reels (also known as wagons), are stored in primary and secondary buffer stock areas until they are used. There is often a shortage or backlog of material, however, waiting at manufacturing lines.
One of Nokian Tyres’ priorities was to reduce the size of local and primary buffer stock, thereby ensuring the correct amount of product is available at the manufacturing line and not building up as buffer stock. Prior to implementing an RFID system, the company attached color-coded plastic cards, printed with text, to the steel reels to indicate which assembly line they were destined for. Workers then had to estimate the time at which the reels needed to be available for the assembly line.
Nokian Tyres carried out RFID pilot projects involving other vendors before turning to Trackway in 2007. According to Jouni Petrow, Trackway’s director of professional services, the resulting RFID system—for which Trackway provided software and integration—directs which types of treads are to be manufactured, monitors stock levels by tracking the location of reels of rubber tread in storage and at the assembly line, and alerts forklift drivers regarding the appropriate time to move a particular reel of treaded rubber to the correct location.
The Trackway system, installed in mid-January 2008, enables Nokian Tyres to manage its RFID interrogators, process its bar-code scanner data and instruct forklift drivers to pick up specific reels and inform manufacturing line employees to create specific treads and tire styles. Two operations take place at the plant: First, the tire company makes 100-meter-long strips of treaded rubber, each of which is then wound onto a reel and delivered to the tire assembly line, as needed, to be unwound, cut and attached to other tire components such as steel cord.
Initially, the Trackway system software informs employees at tread manufacturing stations which size and type of tire tread they need to create. If workers choose to make a different tread type and size than what is requested, they must first manually override the system.
When workers finish making a tread, they roll it onto a reel, which has a Confidex plastic-encased EPC Gen 2 UHF passive RFID tag encoded with a unique ID number, as well as a bar-code label containing the same ID number. An Elektrobit Group (EB) RFID reader at the end of the manufacturing line captures the reel’s tag ID number and transmits it to Nokian Tyres’ back-end system via a cabled connection. The Trackway software then links that tag number with the specific size and type of tread that has just been manufactured.
The reel is carried by forklift to a temporary storage area known as the “primary buffer stock.” It then passes another EB RFID interrogator as it enters the buffer stock area, says Olli Airaksinen, EB’s sales and marketing director of wireless sensor solutions, indicating the reel has arrived in the primary buffer stock area. There, forklift drivers place the reel on a shelf at one of about 30 queues.
Once the reel is placed in its queue, the forklift driver uses a NordicID PL3000 handheld computer to scan the reel’s bar code, as well as the bar-code label on the shelf at the queue, indicating the reel’s location. The handheld device enables the driver to scan reels when he needs to leave his forklift. The PL3000 also contains a built-in RFID interrogator, though the forklift drivers primarily use the device’s bar-code scanner at present, because the RFID reader might erroneously capture the tags of neighboring reels.
When the assembly line is in need of another reel of treaded rubber, drivers are alerted on their forklift’s wireless terminal, which displays the tread reel number as well as the ID number for that particular assembly line. The driver picks up the requested reel and employs his vehicle’s built-in PowerScan XLR extra-long-range bar-code scanner to confirm the reel’s identity, then drops it off at the local buffer stock area—the one nearest to the destination assembly line—and once more scans the bar-code labels on the reel and at the local buffer stock queue. The vehicle’s wireless terminal then sends a message to the server, notifying the system that the reel has been delivered to a local buffer stock area, to be pushed by hand to the assembly line.
When the reel is wheeled into position at the assembly line, another fixed EB RFID interrogator at that location captures the reel’s RFID tag number. Here the use of RFID allows employees to move more quickly with the manufacturing process than when using the bar-code scanners. “This event generates a signal which tells us that that individual wagon is now in use,” Petrow says. About 10 minutes after that time, the reel is automatically identified as empty in the back-end system, which then sends out an alert indicating the assembly line is ready for another reel.
Nokian Tyres declines to comment for the article, but Petrow indicates the system has made operations more efficient at the plant by reducing over-stocks at the buffer areas, and by ensuring a full reel is always available for the assembly line when needed. Nokian Tyres is utilizing the system on this particular assembly operation, Airaksinen says, but could eventually expand it to include the production of other tire products as well, such as steel cords.
“That would be the next phase,” Airaksinen says. “They selected the most complex [manufacturing] process first, and now they can look at implementing the system for other products.” That strategy, he explains, allows the company to test the system in a limited fashion prior to deploying it more widely to a variety of manufacturing processes. “Companies look for isolated benefits first,” he notes, “then they make an enterprise solution, like a patchwork, and they can start to really get value from the system.”