Intermech Machinery, a Singapore distributor and manufacturer of industrial automation components, is using RFID to help track and manage inventory and production at its new 52,000-square-foot factory in Tuas. Its goal is to improve customer service by delivering better products more quickly.
Intermech got its start 16 years ago as a distributor of such products as geared motors and speed controllers, and as a manufacturer of subsystems for factory automation. The company says it used to keep customers happy by fulfilling orders within one to two months. However, according to C.E. Tan, Intermech Machinery’s general manager, that has now changed. “Today, they are demanding less than a week of turnaround time to achieve their own just-in-time targets to reduce downtime,” Tan says.
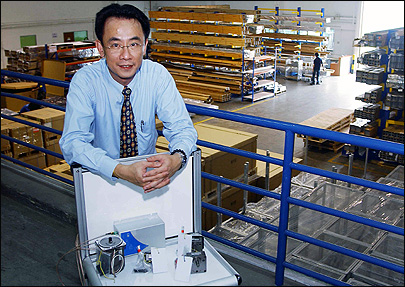
To improve visibility into its inventory and distribution processes, Intermech is using passive HF (13.56 MHz) tags made with Philips Semiconductors‘ I-Code SLI chip, which is compliant with the ISO 15693 standard. The tags are affixed to about 80 percent of the inventory of products the company distributes and the materials it uses to manufacture subsystems. Each tag is encoded with the item’s unique purchase-order number andthe date the item was received. RFID antennas placed on shelves communicate with RFID readers and multiplexers. Intermech worked with TCM, an RFID systems integrator, to provide customized antennas and other RFID components. Its readers, meanwhile, were supplied by Brooks Automation.
The antennas automatically read the tags, thereby detecting the volume and age of the inventory sitting on the smart shelves. This allows the company to adhere to its first-in-first-out (FIFO) inventory policy, designed to reduce waste stemming from outdated materials. Many of the components Intermech offers have one-year factory warranties. If warranties expire, Intermech has to put the components through costly and time-consuming tests to have warranties reissued.
The RFID interrogators transmit tag data via a wireless 802.11g network to Microsoft Dynamics AX, a supply-chain management system that keeps track of inventory and work-in-progress, helping to manage picking, packing and shipping processes at the factory.
In addition, before goods are shipped to customers, supervisors provide employees with handheld RFID interrogators and a pick list generated by supply-chain software. The latter identifies the exact products needed to fill orders, and on which shelf and in which case the products can be found. Employees then pick these products, using handheld interrogators to read their tags and document that the correct items were picked for a particular order. In addition, workers in Intermech’s factory use handheld interrogators to track works-in-progress as they move from pallet to pallet and assembly station to assembly station.
Intermech expects the system to reduce materials wastage by up to 50 percent, while driving up overall business productivity by 40 percent. The RFID technology and supply-chain software are replacing manual inventory and tracking procedures that Tan says had provided very little visibility into actual inventory. Because of that lack of visibility, Intermech Machinery typically had to keep 20 percent additional on-hand inventory to serve as a buffer against out-of-stocks.
“Each touch point along the supply chain brings extra labor, expense and increased risk of manual mistakes,” Tan says. “For example, the wrong product being moved to the wrong locations leads to a slowdown of Intermech’s manufacturing operations and possible missed customer-delivery dates. The primary goal of the RFID solution is to help Intermech reduce overall costs of operations and increase profitability.”
Intermech tested RFID for a year prior to implementing the technology fully in its new factory, which opened doors in May 2006. The company determined that it did not make economic sense to tag every item. Therefore, it figured out which items it would tag and which it would not.
Already, there have been improvements reported. Ultimately, Intermech says it expects the RFID and supply-chain management system to help reduce the man-hours required to take inventory of its stock. Prior to its RFID implementation, Intermech needed 40 employees working one entire workday to check stock. With its RFID system deployed, however, it hopes to accomplish the same task using just two employees working half a day.
What’s more, Tan says the system is increasing the number of orders Intermech can accurately fulfill. “Previously, it would take up to one working day to process just one customer order,” he says.
Intermech is now working with manufacturers in Germany, as well as with local suppliers, to determine how it might use RFID to improve its collaboration with those companies.