London’s Heathrow Airport is evaluating the results of a three-month proof-of-concept (POC) involving the use of radio frequency identification technology from Vero Solutions to track its luggage carts [trolleys] as they arrive at and leave a baggage-claim area at one of its terminals. The pilot—which ran from October 2017 through January of this year—was intended to determine how well technology can track the numbers of carts, and thereby ensure they are available for passengers when they are needed, as well as to better understand how many were onsite at any given time.
Heathrow is the second busiest airport in the world in terms of international flights (its flights go to 84 countries). It is those international flights, as well as many domestic ones, that generate a high volume of luggage, along with the need for passengers to transport those bags. The airport’s Innovation Team, which managed the RFID pilot, has found that the technology was effective in capturing the movements of carts into and out of the baggage-claim area, and it is now researching how an airport-wide solution might work.
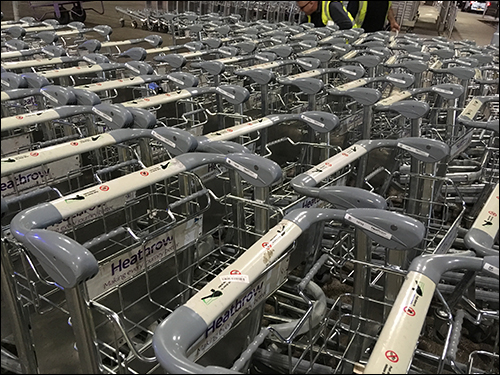
The Innovation Team is tasked with testing new technology options for solving problems at Heathrow, one of the world’s busiest airports. The group takes a systematic approach to testing the technology in practice before planning full-scale deployments, according to Ben Wagenaar, an innovation technologist at the airport. Any technology, he says, must solve an ongoing business challenge, in order to have a place at the airport.
The airport’s Trolley Operations Team consists of personnel tasked with walking around the areas in which carts collect, including parking lots, and returning them to the places where they are needed—namely, the arrivals and baggage-claims areas. They also deliver carts requiring repair to a staging area, where they are then sent to a third-party provider that services the carts. On occasion, carts run out when passengers need them.
In general, Wagenaar says, the Trolley Operations Team is highly efficient at its work. They did not need to track the carts as they moved around the airport, he notes, as much as they needed to know how many they had on hand—especially in the areas in which they are needed most by passengers. “They’re brilliant at finding the trolleys, he states. “They have a good system,” but lacked visibility.
The airport hopes the technology could provide enough visibility into the carts’ locations that they could begin to predict high-demand times and adjust the collection and transfer of the carts around the airport accordingly. The pilot consisted of passive UHF adhesive tags affixed to approximately 2,000 carts. The airport attached low-cost, off-the-shelf tags to the plastic handles of the carts, Wagenaar explains. It chose the low-cost tags in order to ascertain whether they could sustain damage from use around the facility.
The airport piloted the system at Terminal 4, the most secluded of its terminals. It installed five Impinj Speedway x-portal RIFD readers around the baggage-claim area, says Declan Begley, Vero Solution’s business-development manager—one each at the three ingress gates and the two exit doors. Each time a tagged cart passed into or out of the baggage-claim area, the tag’s unique ID number was captured by the Power-over-Ethernet reader, and was then forwarded to a cloud-based server, where Vero Solution’s software interpreted and managed the data.
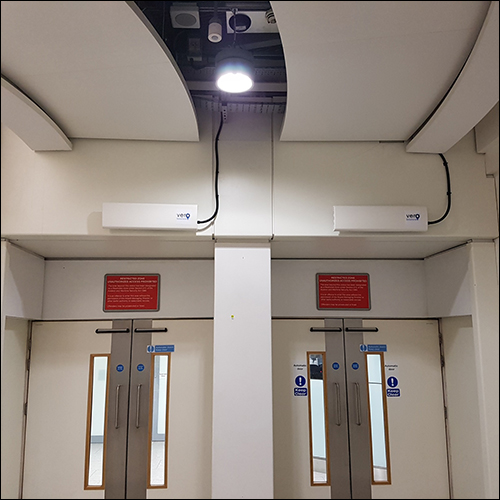
During the pilot, the airport dispatched personnel to the site to physically count the carts, using a manual paper-based system, as they arrived and left, to be compared against the RFID data. Begley says the team found that the RFID data effectively captured each cart as it passed through the reader portals, except in cases when a tag had been lost. The read range was at least 10 meters (33 feet), Wagenaar estimates.
In some cases, passengers removed tags or they were damaged by luggage or transportation, and those tags then needed to be replaced. For that reason, Wagenaar says, the team never had a complete and specific count of the carts onsite, though it did gain visibility into the number of carts in the baggage-claim area at any given time. If the number of carts became extremely low, trolley-management employees could restock them.
However, the airport discovered that in some cases, the team was more effective than it needed to be. Wagenaar says the airport had estimated that one out of every two passengers use the carts, but that the average was found to be lower with the RFID system. Now, the airport has data on hand that helps it to understand how many times a specific cart was used during the 12-week pilot, as well as how long it took for that cart to be returned to the baggage-claim area, on average, or during any specific date and time.
Traditionally, staff members sweep through parking lots and other areas in order to collect all trolleys and return them to the baggage-claim and departure areas at night. However, the RFID data showed that the carts may not need to be restocked at the rate and volume that they were, since passengers utilized fewer trolleys than expected.
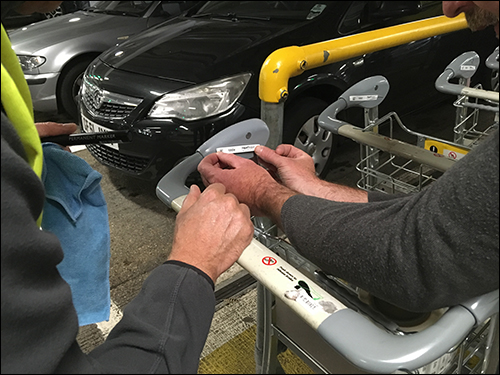
If the system were deployed throughout the five-terminal facility, Wagenaar says he thinks the airport could accomplish more. For instance, if it were to link RFID data regarding cart use with flight information (such as shortly after a large international flight arrives at a particular terminal), it could better manage the staging of carts to ensure their availability to those passengers. It could also track the day and time, and thus better meet needs according to traffic flow. What’s more, it could link weather information—for instance, more carts might be borrowed on rainy days.
Additionally, the technology could bring intelligence to the repair process. For instance, if a specific cart were returning to the service facility for repairs on a frequent basis, airport management could identify that it needed to be replaced, thereby reducing the number of problematic carts onsite. That data could also be of use when carts are purchased, Begley says, since the airport could better understand the lifespan of carts, identify which carts are more rugged, and predict when they may need to be replaced.