When companies print RFID labels in large volume, ensuring that they all operate prior to shipping them to customers can be a manual process. Businesses may test sample tags, such as the last few tags of every roll, or test a small number of completed rolls of labels, by using an RFID reader to ensure they can all be interrogated. Since 2005, GlueLogix has been providing its LineLogix solutions to label converters and service bureaus, to automate the identification of any inoperable labels. The LineLogix product line consists of several devices used independently or in tandem, including one that reads each tag and marks any that are found to be inoperable in the label press machinery. Other LineLogix products include rewinders or rewinder retrofit technology for identifying inoperable tags during the rewinding process (which follows the manufacturing stage in the press). GlueLogix equipment also encodes tags as needed by a customer.
This month, GlueLogix is introducing a new narrow-field antenna to help its customers read tags within an area comprising 1 square inch, enabling them to test tags that are smaller and more tightly arranged on a roll, and to thereby print a greater quantity of labels, faster, within a narrower roll. Next year, says Larry Martin, GlueLogix’s CEO and founder, the company also plans to release a conveyor system for testing and identifying inoperable tags in other form factors, such as hard labels or key fobs.
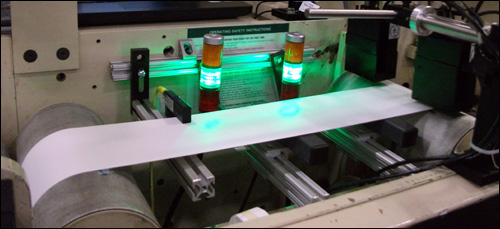
For the past several years, GlueLogix’s solutions have been sold by Tamarack Products, which manufactures specialty equipment for affixing materials such as RFID inlays to labels and cartons. Tamarack also sells the LineLogix product line as part of its own solution, to be used on presses or during the rewinding process, says David Steidinger, the company’s president. Tamarack’s RFID inlay inserting equipment (which has been available for approximately 15 years) can be retrofitted onto its customers’ existing presses.
Martin founded GlueLogix after working at RFID hardware and consulting firm SAMSys Technologies, which was purchased by Sirit (now part of 3M’s motor vehicle services and systems division) in 2006 (see Sirit to Buy SAMSys Technologies). According to Martin, GlueLogix was incorporated, and began selling embedded system firmware products, in 2005 for the printing industry. The company found a niche in RFID almost right away, he says, and has since been offering tester, rewinding and encoding solutions.
Many label converters that are GlueLogix customers have traditionally been in the paper-printing business, with a limited background in RFID technology. When RFID labels are converted using equipment designed simply for paper, Martin explains, things can go wrong for. For instance, he says, the static electricity generated from paper can damage RFID inlays, while the press and rewinding machinery can put excessive pressure on inlays and break a chip or antenna. If a company wants to ensure that it does not sell ineffective labels, it must either develop its own reader solution to identify each unreadable label during post-production, or run scans on samples of labels in the hope of identifying any potential problems.
LineLogix solutions are designed to ensure that ineffective labels are identified before rolls are sent to customers. The company’s press-based system can be fitted into a label press itself. Here, the label is printed, the adhesive is attached along with the label backing (a strip of release liner, typically made with silicon) and an RFID inlay is mechanically attached to the label. If a LineLogix device is installed in the press, each label is read after the inlay is attached; in the event that a label fails to respond to the interrogator, the LineLogix system paints a black mark on that label.
Following the conversion process, the resulting large roll of RFID labels is rewound on another machine, and is then cut into smaller rolls, to be sold to customers. GlueLogix manufactures rewinders with built-in RFID readers that interrogate the labels (as an alternative to reading them at the press), as well as sensors that can be used to identify an ineffective tag’s black mark (in the scenario in which the label was marked in the press). It can then deactivate the rewinder until staff members replace that inoperable label with a working one, and also mark bad labels to be addressed later by personnel.
If the customer alternatively opts only for the LineLogix system for marking ineffective labels in the press, employees can simply watch the labels pass on the LineLogix device, or any industry standard rewinder, and manually shut off the machine long enough for the labels to be replaced.
LineLogix products can read labels at a rate of about 20 per second, GlueLogix reports. The latest narrow field antenna, Martin says—which isolates its read area to about 1 square inch—allows users to reach the same speed with smaller, more closely spaced tags. Several converters are attempting to reduce label size in order to make them closer in size to the inlay inside them, he reports, thereby saving material and enabling a greater number of labels to be encoded and printed within a smaller space. With the new antenna, Martin notes, a company could run an 8-inch-wide roll with eight labels across its width, and then test-read each row of labels at once.
Next year, Martin says, GlueLogix plans to introduce a conveyor system for RFID cards or other single-piece items not produced on a roll. In this case, an item—an NFC ID card, ski lift ticket or ultrahigh-frequency (UHF) key fob, for instance—could be manufactured and then sent down the LineLogix conveyor, which interrogates each item, rejecting any whose RFID inlay is not read properly.
The company currently has about 20 customers that serve either as converters or service bureaus, most located within the United States or in other parts of North America. Martin says he is in conversations with several potential customers in Europe as well. The systems typically cost about $10,000 to $15,000 apiece, depending on the specific solution in use.
Tamarack offers its P500 and P300 inserting systems for inserting RFID inlays into labels (see RFID News Roundup: Tamarack Intros New RFID Inlay Affixing System). Typically, Steidinger says, each solution is custom-made for a particular end user’s needs.