It’s a well-known fact that metal causes two major problems for radio frequency identification transponders: It can reflect energy away from a tag, and it can detune a tag antenna, preventing it from receiving energy from a reader.
Several years ago, RFID providers met the physics challenge: They developed “on-metal” tags, now available in a wide variety of sizes and frequencies, that enable companies in myriad industries to track metal assets and to use RFID in warehouses and other environments that contain metal fixtures. Many on-metal tags are designed to withstand harsh environments, so companies in the construction, energy and manufacturing sectors can use RFID to track parts, pipes, tools and other equipment (see Rough Riders: RFID Tags Get Rugged).
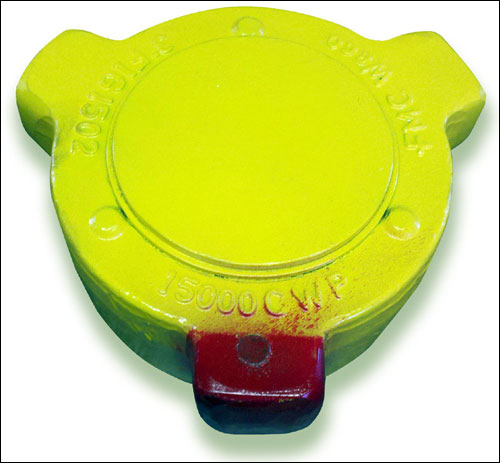
solution enables a company to keep track of the assets it rents to oil and gas firms.
Still, there are some applications for which on-metal tags don’t work optimally, because the asset is too small, conditions are too harsh or the tag interferes with use of the asset. So RFID providers developed tags that can be embedded in metal items. These solutions are designed to track a variety of assets, including surgical equipment, handheld tools, weapons, metal utility poles, heavy machinery exposed to extreme heat and vibration, iron beams, oil and gas pipes, and valves, agricultural equipment and industrial bolts for automotive assembly.
“On-surface solutions are generally considered first,” says Patrick King, founder of tag provider Technologies ROI (TROI). But, he adds, on-metal tags can be vulnerable to certain environmental conditions. “Some companies may want to ensure mechanical, chemical or heat integrity, which adds life to the solution,” he says. Embedding the tag prevents it from being hit or exposed to unusual chemical procedures, as in the case of paint lines and metal foundries.
In addition, the use of on-metal tags can affect the design of finished products. “When you design any product and assuming you take pride in your work, you will always make an efficient design with no waste and meeting all specifications,” King says. “If someone then comes to you and suggests either adding to the design or removing something to replace it with a tag, then likely the proposal violates your design intent and may even put the design at risk for quality or cosmetics.”
The solution, King says, is to make the tag an integral part of the product, and have the design engineer “envision a total solution and not one modified after fabrication. This is the real goal and the likely outcome needed in order to have the embedded tag market take off and grow significantly.”
Embedded tags are ideal for tracking IT equipment and other high-value assets, says Tracy Gay, VP of marketing at Omni-ID. In addition, Gay says, the company’s tags are commonly embedded in tools used in industrial manufacturing or aerospace industries. They are “especially critical” in aerospace, where they enable technicians to “easily scan planes after maintenance to ensure that no tools are left behind,” she notes.
Another benefit is that embedded tags can provide security for high-value assets, says Richard Aufreiter, director of product management for identification technologies at HID Global. “The RFID component is fully protected from the environment,” he says. “The tag is not visible and cannot be removed—as long as it is embedded into the asset itself, instead of simply being a tag with metallic housing.”
Embedding tags in assets is more expensive than attaching on-metal options. But, King says, manufacturers need to consider the long-term benefits. “If a tag is incorporated into the raw material, that allows for automated tracking of the entire work-in-process, so the cost of embedding plummets.”
Here’s what else you need to know to determine whether an embedded tag solution might be right for your company. For more details, see the vendor table on opposite page.
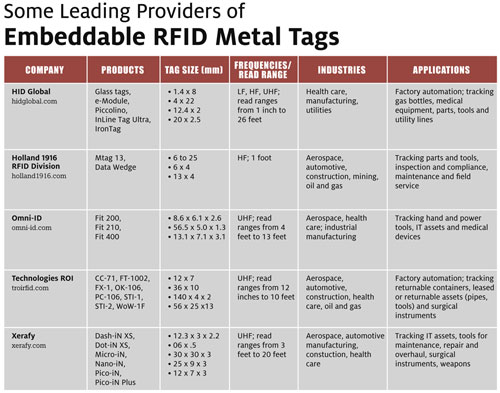
Embedding the Tag
Metal assets can be retrofitted with embedded RFID tags or the tags can be embedded during manufacturing. Retrofitting involves drilling a cavity into the asset, placing the tag inside, then covering it with a metal plate that is typically screwed or snapped in, or backfilling the depression with resin. TROI’s FX-1 tag is a small round plug with a magnetic base that can be pressed into a fitted hole or secured by the magnet to the metal in a larger recess. (TROI tags are available from William Frick and other RFID providers.)
Generally, it costs more to add an embedded tag aftermarket. “The lowest cost is when the part to be tagged had the recess [for the tag] prepared in production,” TROI’s King says. “In this scenario, the tag can even be added during fabrication, including by automation, at a reduced cost.”
“Several OEMs [original equipment manufacturers] currently include RFID in the manufacturing of their products,” says Sanders Roth, director of Holland 1916‘s RFID division. “But most OEMs retrofit the tag into the asset based upon customer requests.”
Xerafy provides a user guide for its family of “iN” tags. “We have had customers who retrofit their existing assets [such as gas valves and meat hooks], and there are already tools on the market from manufacturers like Stanley Black & Decker that are manufactured with RFID tags already in place,” says Xerafy CEO Dennis Khoo.
Choosing an Embedded Tag
Embedded tags come in a variety of shapes and sizes, and frequencies and read ranges, which determine how the tags can be embedded into metal and what functions they provide.
“Low-frequency technology is suitable for embedding a tag into a full metallic housing with no opening,” HID Global’s Aufreiter says. “High-frequency technology requires that there be a small opening in the metal to power the antenna, which makes it suitable for use with NFC [Near-Field Communication] handsets, adding value to the overall solution. Ultrahigh-frequency is not suitable for embedding into metal without a large opening [the full antenna must be exposed].”
HID Global offers products in each of these categories. Its LF solutions include a Glass tag that can be embedded in metal for use in inventory tracking, warranty validation and other automation and manufacturing applications. The e-Module and Piccolino HF tags can be used for tool maintenance and utility line applications. Its UHF tags include the InLine Tag Ultra, for tracking vehicles, pallets, shipping containers, gas cylinders, and commercial and industrial bins, and the IronTag, designed for tracking machinery, metal tools and industrial components in harsh environments.
Holland developed its own HF chip, and works with Xerafy, Tagsys and other partners to provide UHF components. “We are a metal fabrication shop so we have the ability to make any shape the customer needs,” Roth says.
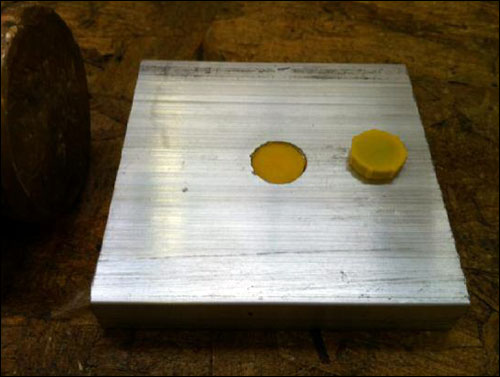
in a metal asset and push the tag into it.
Omni-ID offers the Fit 200, a very small, passive UHF tag suited for tracking hand tools and medical devices. It has a read range of roughly 8 feet with a fixed reader and 4 feet with a handheld. The Fit 210 is a bar-shaped tag the company says works well for tracking hand and power tools.
The Omni-ID tags are all embeddable, but require varying levels of custom tuning depending on the application, says Tony Kington, managing director and executive VP of sales, Europe and EMEA. “There is not an off-the-shelf solution, because there are a number of variables when you embed a tag that can affect performance,” such as the size of the recess into which the tag is being embedded, he says.
Xerafy offers “the smallest UHF RFID tags on the market,” Khoo says. Its Dash-iN XS and Dot-iN XS are designed to track small tools and surgical instruments. “The tags are also designed to comply with medical standards and put to the test to ensure they survive repeated autoclave cycles,” he says. For applications that require a long read range, such as tracking metal assets at construction sites and during automobile manufacturing, Xerafy offers the Micro-iN tag, which has a 20-foot read range.
RFID providers admit that the market for embedded tags is small. But they believe there will be a growing demand for such tags as more effective ways of embedding become available and more companies begin tracking metal items through the supply chain.
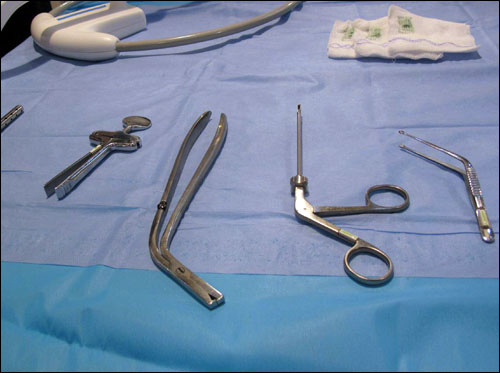
with medical standards and survive repeated sterilizations.
TROI, for example, has developed a proprietary embedding method in which the metal part being tagged actually becomes the tag. This enables significant cost savings and improved mechanical and chemical performance, King says. The company also has a patent-pending design for a tag that can be screwed into a threaded hole. This tag can withstand extreme temperatures and pressure, he says.
“As the size of embedded tags continues to shrink… and more manufacturers begin to tag at the source,” Xerafy’s Khoo says, “this market will continue to grow.”