A Chinese mine has been testing an automatous vehicle and machinery system that employs Internet of Things (IoT) and other automation technologies to capture, manage and transmit data related to each vehicle’s operation. The technology, being used in the open pit mine in the Inner Mongolia province, enables vehicles to travel into and out of the mining area, as well as pick up and transport materials, while understanding their location and proximity to other vehicles—all without the presence of drivers.
Solution provider TAGE Idriver Technology Co. has teamed up with Wind River to provide the solution for autonomous vehicles leveraging sensors, as well as wireless connectivity and software to allow the trucks to operate safely within mines without the need for human intervention. The technology companies are offering the solution commercially after a year of testing it at the Mongolian site. During the pilot, unmanned dump trucks have been traveling on fixed pre-programmed routes, using automatic obstacle avoidance and accomplishing material pick-up and dumping.
Wind River is a California-based software company whose solutions are designed to provide edge-to-cloud connectivity, according to Gareth Noyes, the firm’s senior VP of products. In partnership with TAGE, Wind River is providing the onboard and server-based software, as well as an NXP Semiconductors i.MX 6 Series multicore processor with 5G cellular connectivity.
TAGE Idriver Technology, based in Beijing, was launched in 2016 to design an autonomous vehicle solution for use in open pit mines. The resulting Idriver haulage system allows trucks that transport material out of the mines to operate completely autonomously, using sensors and software-based intelligence to understand not only their own location within the mine, but also those of other vehicles, and thereby travel safely along prescribed routes.
Robotic mining haulage is intended to reduced accidents, keeping labor costs down while enabling operations in areas where access to labor is limited, explains Huang Liming, TAGE’s chief technology officer. To date, the intelligent mining solutions company has carried out deployments at mines in China, operated by such companies as Baogang and State Power Investment Corp (SPIC). “The application of an autonomous haulage system solution will not only protect mining workers,” Liming says, “but also greatly improve the overall economic benefit of mining enterprises.
In traditional driver-operated vehicles, Liming says, dispatchers must send workers onto the site. Operations at the mine are restricted to the availability of workers and the shifts that each person works. For instance, he adds, “The large vehicle requires two drivers. After automation, it will be driverless and work around the clock.” In this way, Liming explains, “The working site is considered safe, with relatively few personnel.” To enable this, TAGE equips vehicles with the company’s central control unit (CCU) core algorithm module, which analyzes data from the vehicle’s sensors. With the commercial release, the system is being provided as new machines or as retrofits on existing ones.
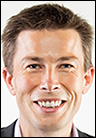
Wind River’s Gareth Noyes
Wind River’s role is to provide software that enables the capture of a vehicle’s onboard sensor data, in order to detect where that vehicle is located and the orientation of other trucks around it, and to then forward that data wirelessly to a server, as well as enabling the vehicle’s automatic response in real time. Traditionally, Noyes says, Wind River provides its VxWorks solution for safety-critical intelligent devices and systems. The technology is being used, for instance, by the Insight Mars Lander, as well as in medical infusion pumps and imaging systems in the healthcare market, and for manufacturing robots in factories.
The technology companies began working together on the autonomous mining vehicle solution during the second quarter of 2019. TAGE has used VxWorks in the past with positive experiences, Liming reports. “VxWorks works in the master computer of the autonomous vehicle,” he says, by integrating with the vehicle’s CCU. “It provides real-time views, including processing of various sensor information and motion-control components.” The technology was then deployed at the Mongolian mine on 10 vehicles.
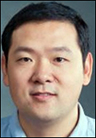
TAGE’s Huang Liming
In each vehicle, Wind River provided an NXP i-mxp unit integrated with the CCU. The sensor data being captured by the CCU includes vision from the front end, along with GPS satellite-based location and T-Box V2V data. The onboard software performs prediction, planning and decision functionalities for forward collision warning, automatic emergency braking, lane department warning and blind spot monitoring, among other features. The system can then generate and deliver the vehicle control command via a controller area network (CAN) bus to the truck’s chassis or power train. The vehicle’s data is captured in Wind River’s onboard gateway, which forwards that information via a 5G cellular connection.
Testing has been under way at the mine that generates earth minerals, iron, niobium, manganese, phosphorus and flourite, Liming reports. Mining vehicles, which typically stand 6.8 meters (22.3 feet) tall and have a payload capacity of 150 to 172 tons, leverage the system to travel and conduct operations around the site, using the onboard intelligence in real time, while sending the data to a server via 5G connectivity provided by China Mobile. The mining company can then view the movements of vehicles as they go about their tasks, or manage historical data about a particular vehicle’s movement, along with related productivity in the mining operation.
The solution is adaptable to both large mine trucks and non-rigid wide-body dumpers. TAGE provides the technology for blasthole drill rigs, excavators, bulldozers and other manned auxiliary equipment to enable them to locate the mine’s truck fleets.