Research and real-world retail deployments have proved that inventory accuracy is the foundation for a solid omnichannel strategy (see Retailers Must Reframe Their Thinking). This fact has been widely publicized in the retail sector. So it surprises—and frustrates—me that many retailers simply refuse to acknowledge that they have an inventory accuracy problem, or fail to recognize the issue.
Recently, some folks from a major retailer contacted the RFID Lab and asked us to give its C-level executives an overview of the use of RFID in retail, where we thought it was headed and discuss best adoption practices. As usual, we asked if the retailer knew its current inventory accuracy. Their reply: “Yes, and it is in the upper 80s or lower 90s [percent].” I immediately knew we had a problem. No large retailer we have worked with or know of has consistent inventory accuracy in that range without using RFID. We asked if we could conduct our own audit to check their inventory accuracy in a randomly chosen store. They agreed. We chose five categories in the store and did a thorough manual count of the items in each category and then a comparison of those counts against the system of record.
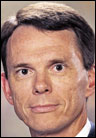
We found inventory accuracy ranging from 30 percent to 60 percent across the five categories. Typically, we find inventory accuracy without RFID to be roughly 60 percent. So this retailer was average to below average in the categories we examined. The obvious question: Why did they think their inventory accuracy was approximately 90 percent, when we found it to be less than 60 percent?
Upon further discussion, we found the answer. This retailer looks at inventory accuracy on an aggregated level—that is, it aggregates similar stock-keeping units to form groups rather than looking at inventory accuracy at the stock-keeping unit (SKU) level. Take hand towels, for example. If the inventory system shows it has 100 hand towels and a manual count finds 90 towels, the retailer concludes its inventory accuracy is 90 percent.
The issue, of course, is that all the different colors and styles of hand towels are combined. When disaggregated, there are many different SKUs: yellow, 100 percent cotton hand towels; blue, 100 percent cotton hand towels; pink, 80 percent cotton hand towels; and so on. At the individual SKU level, only 40 percent of the SKUs had an accurate count.
Which count do consumers care about? The answer, of course, is the latter. Consumers don’t care if you have 90 total hand towels. They care if you have the yellow, 100 percent cotton hand towel that matches their bathroom. In today’s omnichannel environment, inventory accuracy must be viewed at the consumer-facing (SKU) level, rather than the aggregate level.
Too many retailers ignore their inventory accuracy problems, purposely mask them (by, for example, looking at aggregate counts) or work around them (by holding more safety stock). The first step to correcting the problem is to recognize and admit you have a problem. It is time for the Emperor to put on some clothes.
Bill Hardgrave is dean of Auburn University’s Harbert College of Business and the founder of the RFID Lab. He will address other RFID adoption and business case issues in this column. Send your questions to [email protected]. Follow him on Twitter at @bhardgrave.