In many companies, a large chunk of time is wasted on manual, repetitive work. This is not only soul-crushing for employees, but also incredibly counter-productive. On average, the hours devoted to routine, data-intensive tasks represents a loss of up to 19 working days annually per employee. Beyond that lost time, which could be redirected to more worthwhile work, this outdated approach also impacts finances. Operational inefficiencies end up costing companies 20 to 30 percent of their revenue every year.
Furthermore, it’s difficult for many of these manual processes to operate efficiently in a virtual workplace—as many businesses are discovering, their existing processes are under new strains due to the impact of the global COVID-19 pandemic, which requires a whole new way to approach completing work with customers and partners.
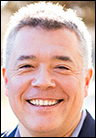
Fortunately, with so many digital technologies within reach today, it’s possible for enterprises to drive improvements and become more productive—and, at the same time, to work virtually. By using market-ready digital solutions to automate manual processes and modernize operations, these companies can give time back to skilled employees—and add value to their bottom line.
A New Lens on Digital Transformation
There are a number of ways for businesses to accelerate digital transformation and eliminate costly, error-prone processes. A modern approach is intelligent process automation. This is not a specific technology in itself, but rather a strategy that combines multiple technologies to improve performance and profitability.
There’s the saying “If you’re a hammer, everything looks like a nail.” That’s the situation with digital, for which every vendor claims to be the one-size-fits-all solution. However, keep in mind that each element of your digital strategy provides different benefits—don’t pick just one tool. You may need a hammer, but you may also need a saw or a drill or a crowbar; use all of the tools in the toolbox for their appropriate use and they will help you reach the outcome you’re trying to achieve. Think holistically about your digital transformation roadmap and look at the range of technologies you need and the right approach to phasing in the digitization of your processes.
When it’s done well, intelligent process automation can unlock many new opportunities for process transformation. Below are some of the tools and techniques that are often included in the intelligent automation environment.
Process Extraction and Mining
Historically, the challenge facing business-process initiatives was defining or discovering the process; this often required lengthy consulting and business process documentation to produce an understanding of the current process. To more quickly understand the current process state and identify opportunities for optimization, businesses could look to leverage process-mining or process-extraction tools, which can offer objective, fact-based insights derived from actual event logs.
Armed with this process intelligence, companies can audit, analyze and fine-tune existing business processes and look for opportunities to re-imagine using digital approaches. They could, for example, identify process steps that could be eliminated or optimized through automation, artificial intelligence (AI) and other solutions.
Phased Digital Process Automation
With all the noise related to digital transformation, it can be daunting for business leaders to determine the right approach and technology to use for process automation. Sometimes, the uncertainty and risks may lead to analysis paralysis and a hesitation on getting started at all. However, that’s the wrong approach, as there are some compelling business benefits to realize from taking action; using digital can help companies respond more rapidly to change. But it’s important for businesses to start with a clear understanding of what outcomes they are looking to achieve.
They need to build a phased roadmap, with an understanding of the right phases of technologies and how to align resources, people and process changes around those technologies. Digital transformation is ultimately achieved by first having a complete roadmap around what your organization is looking to achieve but taking agile, incremental steps to deliver against that vision.
Machine Learning and Artificial Intelligence
Machine learning (ML) is a subset of artificial intelligence that involves software algorithms that can learn from data to identify patterns and make predictions, without being explicitly programmed to reach these specific conclusions. However, it’s not about completely removing people from a process; that is usually not the right approach, given the need for tapping into subject-matter expertise and being able to make very agile decisions in the face of uncertainty.
Instead, the right approach is usually using ML and AI to assist the process and free up humans from low-value and repetitive tasks, so that they can focus on the high-value and high-impact activities. An intelligent process-automation strategy will use process models and cutting-edge ML to streamline the flow of work between humans, bots and systems to deliver revenue growth, enhance the customer experience and lower operating costs.
Physical and Digital Connections
Integrating processes isn’t only about connecting people and systems—it can also connect to physical things in the real world. Using RFID technology, businesses can automatically identify objects, collect data about these real-world objects and feed that data into digital systems, without the need for human input. This way, physical resources—including goods, vehicles and even people—can be automatically traced or localized as they move through a process or supply chain. This supports more intelligent inventory-management and stock-taking processes, as data on what stock is available in a warehouse can instantly be fed into an application that is used by staff members in a retail outlet, for example.
When these types of technologies work cohesively, companies can digitize end-to-end processes on a single platform or dashboard to provide multiple business benefits.
Identify and Remove Bottlenecks
Process automation and process mining provide companies with end-to-end visibility into all processes and identify opportunities for automation. RFID technology can also improve visibility into inventory and the movement of goods through the supply chain, to help businesses better anticipate and prevent bottlenecks. By identifying and fixing fragmented processes, companies can shorten delivery cycles for new products and services, in order to grow and expand into new markets.
Prepare for Audit and Compliance Checks
Running processes digitally has many advantages in tightly regulated industries, like healthcare or financial services. When every action by technology or human user is logged in the technology framework, processes can be easily audited for inconsistencies. This helps to flag processes that are out of compliance. It can also provide evidence that processes have been executed in line with certain requirements, should this ever be required by internal or external auditors or regulatory authorities.
Virtual and Remote Working
The current global pandemic has accelerated the need to be able to have teams work virtually and support a remote workforce. This has been a trend for some time but it is being accelerated given the current environment. We see digital transformation as a catalyst for enabling this change change, allowing businesses to work virtually by replacing manual tasks or paper forms with newer digital processes; also, it can enable employees to upskill and focus on more strategic, meaningful ways, as opposed to wading around in mundane, repetitive tasks that may require working in a traditional office environment.
Connecting Across Functional Silos
Digital transformation hinges on tearing down data silos and creating a more complete view of what is happening enterprise-wide, from which new intelligence can be used to drive more effective decision-making. If there isn’t a way to connect the data in a meaningful way, businesses will find that their existing systems may not be able to meet a customer’s latest expectations around a modern digital experience.
Modern digital front-ends, like mobile, modern websites or voice, are powerful experiences but are simply the “tip of the iceberg”; what’s below the waterline is often not seamless, and exposes the fact that the processes behind the digital front-end are still often manual, non-integrated and reflect sometimes batch processes. Studies estimate that 70 to 80 percent of the processes on which a business rely are still manual, with documents often being shared via email. It is important to continue to digitize the full business process—otherwise, the customer front-end experience won’t measure up.
Deliver a Return on Investment
Making technology investments to enhance processes and productivity can take time and money. However, with the right strategy and tools in place, the return on investment is clear. With an intelligent process-automation framework in place, businesses can access, visualize and act on data to accelerate digital business transformation enterprise-wide. In order to gain optimum ROI, users should continuously adapt their business processes to accelerate performance improvements and deliver better outcomes.
Importantly, large corporations aren’t the only entities that can benefit from the technologies that work together to power intelligent automation. Recent innovations have made many of these solutions suitable for mid-size companies as well. Despite the high frequency of operational inefficiencies at most large and mid-size enterprises, businesses now have a range of options to improve their systems and processes. Intelligent process automation, which combines a range of different technical capabilities, offers businesses the right solutions to help them drive needed enhancements in order to further productivity.
Burley Kawasaki is the chief product officer at K2. Burley is a software industry veteran with more than 25 years of experience working in leading high-technology and cloud-based companies. Burley leads K2’s global product-management and software-engineering organization and is responsible for K2’s product innovation, design and development as the company continues to drive digital transformation initiatives across enterprises. Prior to working at K2, Burley served as the executive VP of product at Kony, a leading platform in the low-code mobile and Web application development market. He has also held a variety of leadership roles at Microsoft, Avanade and Accenture.