Cox Industries is attaching passive EPC Gen 2 ultrahigh-frequency (UHF) RFID tags to wooden utility poles after they are manufactured at its Blackstone, Va., facility, in order to track their location and status within the yard in which they are stored and then loaded onto trucks bound for utility companies across the Eastern Seaboard. At the same time, in the city of Orangeburg, S.C., the Department of Public Utilities’ Electric Division is applying similar tags to 20,000 poles, for use by its inspectors and maintenance staff.
Both solutions are provided by Sustainable Management Systems. Although the two applications represent different segments in the approximately 40-year lifespan of a wooden utility pole, says Barry Breede, Sustainable Management Systems’ CEO, they could eventually be combined by means of a single tag, attached by a pole manufacturer to each log arriving by truck from a lumber company and used by both the manufacturer and the utility companies that are its customers.
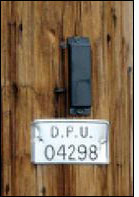
Utility poles, used to support overhead power lines and various other cables and equipment installed by other public utilities, usually measure approximately 40 feet in height. Most are made of wood, and it is these poles that are being targeted for this technology.
Cox Industries’ chief operating officer, Greg Campbell, envisions being able to provide RFID data about the locations of wood poles. Initially, the company is tagging poles after they have completed the manufacturing process (which involves heating to remove moisture, as well as chemical treatment to make the wood more durable), and is using the tag-read data to track the poles’ locations within its yard, as well as to ensure that the proper product is being shipped to its approximately 150 customers. The firm chose to employ less expensive tags that need not go through the rigors of the manufacturing process, though Breede notes that it could also use tags capable of withstanding the heat and chemicals. Though such tags would likely be more expensive, he adds, they would enable it to track a pole through the entire manufacturing process.
The next step for Cox, Campbell says, will be to make information about each pole’s location—based on RFID data collected in the yard, as well as additional information derived from GPS units installed on delivery trucks—available to its customers on a Web portal. In that way, he explains, a customer could view an order’s status, such as whether it is ready for loading or has already been loaded. If utility companies had RFID handheld readers, they could then encode the tags with such information as when a particular pole was inspected or maintained, and use that data throughout the pole’s life.
Sustainable Management Systems was founded in 2009 by Breede, who was a member of Cox Industries’ board of directors when that firm first began investigating inventory-tracking systems for managing the thousands of poles received at each of its 10 manufacturing sites. “I began to see there was a bigger business plan,” Breede says, as he considered the challenges that utility companies faced when tracking poles within their own yards, and then while monitoring the inspection and use of those poles by other utility companies, once the poles were erected.Sustainable Management Systems began developing two solutions: Yardtrack, for Cox and other companies like it, and Pole Information Management System (PIMS), to be used by those further down the supply chain—the utility companies and their pole workers. In 2010, Sustainable Management Systems began testing the Yardtrack RFID system at Cox’s facility in Blackstone, as well as the PIMS solution in Orangeburg, with both pilots completed in the fall of 2010. In both cases, the technology is now being deployed permanently.
At Cox Industries, logs that already have been peeled of their bark and cut to size arrive at the facility, and must then pass through a heating process—in order to dry the wood—as well as a chemical treatment. Each pole is branded with the company’s name, and is then sent to one of several locations within the storage yards, to await shipment to the specific utility that has purchased it. Some utilities require different treatment processes than others, as well as different pole sizes and wood types, so it is critical that the poles are not moved to the incorrect yard location and inadvertently loaded onto the wrong truck.
Typically, poles are tracked by visually checking a serial number stamped on a metal plate stapled to the wood. That system can be time-consuming, however, since the plate numbers are not always easy to see, and must be checked against printed order details.
With the RFID solution, the UHF EPC Gen 2 hardened tags are stapled to the pole after it has completed processing. The tag’s unique ID number is then read using a mobile Motorola RD5000 interrogator, in order to link that ID with data about the pole, such as its size and wood type. Cox Industries and Sustainable Management Systems are currently seeking an inexpensive rugged tag for this solution that would cost no more than $2 apiece.
The poles are transported to other staging areas, based on the specific customer that has ordered them. All seven lift trucks at Cox’s Blackstone facility will also be enabled with RD5000 readers and a 13-inch display screen. When orders are received, the company’s enterprise resource planning (ERP) system sends the order data via a Wi-Fi signal to a lift-truck operator, who can see the order on his screen. He can then proceed to the locations of the necessary poles, and as he lifts a pole, the reader will capture the unique ID number on its RFID tag, verifying that the ID matches one of the poles listed on the order. At that time, either a green or red alert flashes on the screen, thereby indicating if it is the correct pole. Upon depositing the pole at a loading area for trucks, the driver presses the “load” button, which alerts Stratum Global‘s TagNet application software—which resides on Cox Industries’ back-end system—that a specific pole, or poles, has been deposited and is ready for loading. The TagNet software’s function is to receive and store RFID read data.
Cox also installed portals with Motorola FX7400 fixed readers, through which lift trucks pass. Data from the portal, handheld and lift-truck readers is received by the TagNet software, which links the ID number of each pole’s tag with information related to that pole, and identifies its whereabouts within the yard, based on the known location of the fixed reader portal that reads that tag. Cox’s management can then use that data to determine where the pole is located within the shipping process, such as whether it is being loaded onto the correct truck, according to its assigned destination, and when a mistake is made. The TagNet software also monitors activity against configured business process rules. When a process is out of sequence or in violation, such as a pole being removed to an unexpected location, TagNet’s event-management component can issue alerts in the form of e-mail or SMS text messages, or trigger lights or alarms. “So we are not only recording the transactional issue, we are notifying as well,” says Bill Hood, Stratum Global’s chief operation officer.With the data, Cox’s management hopes to improve efficiency at its manufacturing and storage yards, as well as reduce the risk of errors, such as the wrong poles being loaded with the incorrect orders. Although the system is initially being installed only at its Virginia plant, the firm expects, in the coming few years, to roll it out at all 10 of its facilities throughout the Southeast.
In a separate application, the electric division of Orangeburg’s Department of Utilities completed a six-month pilot in October 2010. Based on that pilot’s success, the agency is deploying the PIMS system, which also uses TagNet software, to track maintenance and inspection histories for all of its utility poles. In this case, Breede says, the city utility attached RFID tags provided by William Frick & Co. to between 200 and 300 wooden utility poles already in service. Each tag was encoded with a unique ID number linked, in the TagNet system residing on the utility’s back-end system, to inspection and maintenance data about the pole to which that tag was attached. Orangeburg’s electric division has typically used paper and pen and a computer program to manually manage the inspection and maintenance history data, says John Bagwell, the division’s director. “It was too much paper,” he states, and the filling out of paperwork by pole crews was time-consuming and inefficient. “Barry Breede had approached us, and we thought we’d go ahead with a pilot.”
During that pilot, city workers utilized an Intermec CN3 mobile computer with an Intermec IP30 reader. Upon arriving at a pole, an employee first read its tag’s unique ID number, then used the drop-down menu on the handheld device to indicate the condition of the pole and its many attachments. That data, along with the pole’s unique ID, was then uploaded from the device once it was attached to a PC dock at a central office.
The inspection included the condition of such assets as transformers, conductors and light fixtures mounted to the pole, as well as the pole itself, any tree or brush growth impacting a pole or asset, and any joint-use situations in which another service provider has attached lines to a pole since the last time that an inspection was performed.
This summer, the city’s department of public utilities plans to employ college students to screw tags onto 20,000 poles and commission them by using a handheld device to read each tag’s ID number, and then inputting data related to the pole on which that tag is mounted. With the PIMS system, any problems are designated and sent to maintenance crews in real time as part of an alert. The handheld has a built-in camera and can thus be used to take pictures of the problem. “A key benefit realized by Orangeburg,” Breede notes, “was the improved communication and responsiveness of maintenance to these alerts, as previously this information sat back in an office in-box until someone acted on it.”
The pole installation will use the same type of Frick tags, which are ruggedized to last the 40-year life of the pole. William Frick & Co. is “experienced with outdoor durable identification materials,” says the company’s PR manager, Barbara Crystal.Utilities are required by state law to inspect all of their poles within a defined time period (typically, at least once every five to seven years). They require clear records of these inspections to support their case for a rate increase—a key revenue source for utilities—to the local public utility commission (PUC).
Breede predicts the RFID system can improve workflow processes by reducing the amount of time workers spend in the field filling out paperwork about each inspection, as well as provide a more accurate record of a wood pole’s inspections throughout its life (most poles are expected to remain usable for approximately 40 years).
The system, Bagwell says, will help the utility reach its goal of providing improved power reliability and quality to its customers. “The old school of thought [for utility maintenance] was ‘Don’t worry about it until it falls down, and then put it back up,'” he says. “Our school of thought is providing a system where there are no lights blinking for the customers. This will allow Orangeburg to be proactive in our maintenance.” The result, he says, will be “fewer outages and better service for our customers. That’s our goal.”
In the future, Campbell says, when a low-cost robust tag is identified—that is, one priced at less than $2 apiece—he hopes to be able to apply tags to the logs prior to the heating and chemical-treatment processes, and also plans to enable the tag to be used by customers throughout a pole’s life. Data could be stored on the tag, as well as in the back-end system. With Cox Industries’ Web portal, which the firm intends to offer in 2011, a utility company could log onto the site and learn the location and status of its order, or instruct its workers to remove an outdated pole. The RFID tag on the pole could store not only birth and maintenance data, but also an indication of when it might need replacement—and why.
Over the upcoming months, with a Web portal established, Cox Industries will allow customers to log onto the Web site and look up outstanding orders. The system could then inform a user where a specific order is located within the yard, based on the RFID data collected, or where a shipment is located, based on information received from GPS units installed on Cox’s delivery trucks.
Breede will describe the application in detail during the RFID in Energy preconference seminar at this year’s RFID Journal LIVE! conference and exhibition, to be held in Orlando, Fla., on Apr. 12-14, 2011 (the preconference will take place on Apr. 12).