- Phased Approach to Tagging Higher- and Lower-Value Assets
- Carts Equipped with RFID Readers Capture Room-Level Tag Location
- Time Savings for Nursing, Material Lending, Maintenance Departments
Belgian hospital AZ Sint-Maarten has boosted its asset-management efficiency, ensuring that personnel can locate thousands of items when needed. The medical facility is using ultrahigh-frequency (UHF) RFID technology provided by Aucxis RFID Solutions. Since the system was taken live, it has increased the speed at which medical materials, ranging from pumps to patient beds and wheelchairs, can be located and retrieved, according to Stijn Dupriez, the hospital’s technical department director for projects and quality. The facility has achieved financial benefits as well, he says, since available equipment is now being used more frequently, reducing the need for excess stock.
Approximately 4,500 tags have been applied to date, while the long-term goal is to track in excess of 20,000 assets. The regional hospital serves the area around the Belgian city of Mechelen, stretching from Ranst to Zemst and from Londerzeel to Heist-op-den-Berg. The hospital has 643 beds, in addition to numerous research departments and an extensive outpatient clinic. Around 50 percent of its patient beds are in single rooms. The hospital treats more than 49,000 patients annually, 60 percent of whom receive outpatient treatment, while another 300,000 visit the clinic for scheduled examinations or consultations.
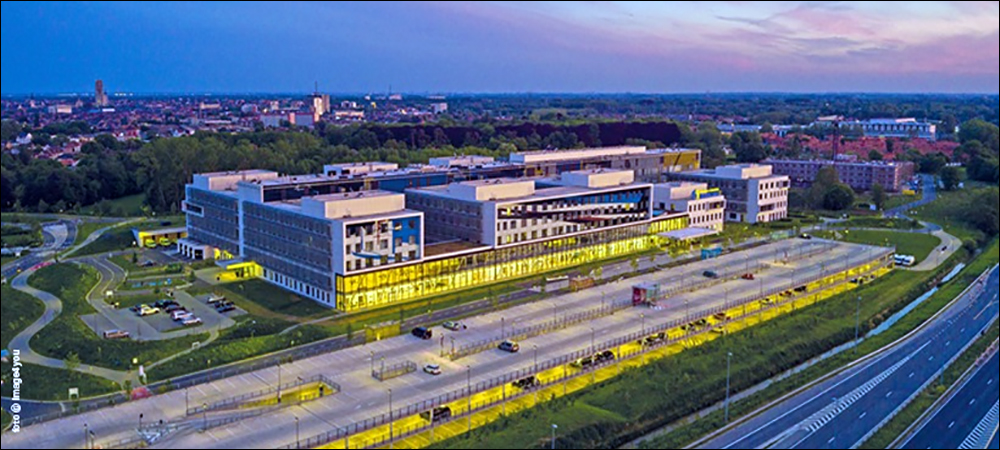
AZ Sint-Maarten
Management and personnel knew, as part of the care process for the many patients, that too much time was being spent searching for assets. That inefficiency was made more apparent with the opening of its new, larger facility in October 2018. The number of hours staff members wasted looking for materials was not registered in the hospital’s enterprise resource planning (ERP) system, but the anecdotal evidence indicated that asset searches were taking employees away from other more critical tasks. Therefore, the facility chose to deploy a system that would address these challenges, and it commenced technology analysis in early 2021.
“We quickly realized that the investment and recurring costs of the BLE [Bluetooth Low Energy] and Wi-Fi active tag technologies would be very high,” Dupriez says. “RFID seemed to be the right and affordable technology to us,” since the passive tags do not require batteries and are, therefore, lower in cost. To further reduce expenses, the hospital looked into ways that it could capture location data without installing fixed readers around the facility. “We developed this further with the Aucxis team and came up with the idea of working with mobile scanners” that could be mounted on the hospital’s existing mobile carts, known as trolleys.
Phased Approach to Tagging Higher- and Lower-Value Assets
AZ Sint-Maarten issued a tender for this concept in May 2021, Dupriez recalls, which was awarded to Aucxis in July of that year. Following a pilot in July, deployment took place between August 2021 and June 2022. Tags are still being applied to assets. From the beginning, he says, “We consciously opted for a phased approach.” A proof-of-concept project was first completed, followed by the rollout with modifications to optimize the system for the hospital.
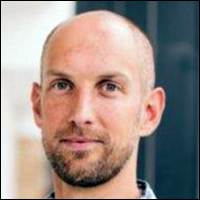
Stijn Dupriez
The facility faced several challenges, Dupriez says, including the tens of thousands of tags it would need to track assets for nursing and equipment maintenance support. The hospital wanted to track not only high-value assets, but also other commonly used items. Aucxis worked with AZ Sint-Maarten to determine that its Atlas kit with mobile readers and antennas could be integrated into existing logistics trolleys, according to Patrick Catthoor, Aucxis’s account manager. The software could be seamlessly integrated into the hospital’s existing Ultimo management system, he says, and because the solution uses passive RFID tags, there was no limit to the number of assets that could be tagged.
The pilot provided the deployment team with confirmation of several technical questions. It found that RFID tags installed in each room’s door hinges could be properly read by mobile readers as carts passed by, or as they entered through doors. It also found tags could be read inside patient rooms from corridors and be linked to specific room tags. The team researched the most appropriate tag for each asset type. The proof-of-concept helped them identify different types of material (metal or textile, for instance) and the most suitable UHF RFID tag for each. The tags needed to meet the requirements of medical environments as well, so they were selected for their resistance to dust, and to the frequent cleanings of the devices on which they are mounted.
The subsequent rollout throughout the hospital involved RFID tags being applied to each piece of equipment. To read those tags, Aucxis integrated its own Atlas hardware kit, with mobile RFID readers and antennas from Impinj, into five existing carts used for the lending of goods and drink deliveries. The readers utilize the battery already built onto each cart for power. In this way, medical personnel need not perform extra tasks to identify the materials, such as carrying a handheld reader and making extra tours around various departments to capture inventory counts.
Instead, the localization process is automatically integrated into workers’ daily routines. As the hospital acquires new products, employees attach a UHF RFID tag encoded with a unique ID number to each item. They then register that tag and link it to the specific product in the ERP software, using a handheld reader running Aucxis’s Polaris app, which interrogates the tag ID and the product’s barcode in order to create the link. The asset is then put into use.
Carts Equipped with RFID Readers Capture Room-Level Tag Location
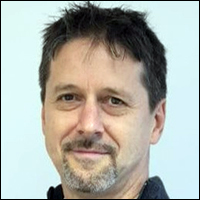
Patrick Catthoor
Each time a cart passes from or near one room to another, data is captured from the door hinge locator tag and the asset tags, and this information is then forwarded to the software via the existing standard Wi-Fi connection. The location data is updated and stored in Aucxis’s cloud-based Polaris Asset Management software. If an item is missing or is identified at an incorrect location, an alert can be displayed for users.
When the trolleys follow routes from one patient to the next, they pass more than 90 percent of the tagged assets, so the staff does not need to perform extra tasks to identify those materials. In order to cover the remaining 10 percent, Aucxis equipped one of the hospital’s transporting carts with the Atlas hardware.
The Polaris Asset Management software serves as an RFID management platform that collects and manages the read data and exports it to the hospital’s Ultimo ERP system. Aucxis’s Hertz middleware runs on the Atlas hardware kit to provide interpretation and integration. The company also extended the Atlas functionalities for AZ Sint-Maarten’s requirements, to serve as a data buffer, and it continues to scan even without a Wi-Fi connection. These added functionalities are now part of the standard Atlas solution.
Time Savings for Nursing, Material Lending, Maintenance Departments
Since the system was taken live, Dupriez says, hospital management has received daily updates regarding the current locations of all tagged materials. “We notice that there are about 250 movements each day,” he states, in which an asset is relocated to a new room or area. By July of this year, 1,899 of the 8,327 medical devices were tagged, while 2,869 of the 16,094 nursing or facility materials were tagged. The cost of RFID label tags is only a fraction of the price of active tags, Catthoor notes, so there is no limit to the number of goods that can be located.
The hospital has found that the technology’s benefit is felt most immediately by support services personnel. For instance, the Medical Instrumentation department can quickly locate materials that require maintenance, enabling them to more quickly be returned for service with patients. Additionally, the Lending Center now knows where assets are located, and consequently in which department, as well as whether departments may be disposing of too many or too few lendable items. Meanwhile, the Nursing Department can retrieve data in the Ultimo ERP system indicating which materials are currently in that area.
“We have now started tagging our medical materials that move frequently,” Dupriez states, along with objects loaned out by the Lending Center. Furniture and some technical equipment, such as ladders, are slated to be tagged next. Going forward, he reports, the hospital pharmacy will conduct analysis to examine the tracing and automatic invoicing of medical implants and catheters.
Key Takeaways:
- RFID readers installed in mobile carts enable healthcare employees to capture asset data as they move around the facility conducting patient-care tasks.
- The data is helping AZ Sint-Maarten to track not only high-value equipment, but also commonly used, lower-value products, to ensure materials are available for treatment when required.