Several industrial companies will be testing a new version of Panasonic‘s Logiscend Software 3.0 solution, which provides Bluetooth Low Energy (BLE)-based location within approximately 1 meter (3.3 feet). Users can gain the real-time locations of goods or assets in industrial or manufacturing environments, with limited infrastructure installation. The Logiscend solution provides material-flow management and could also leverage a UHF RFID-enabled Panasonic VIEW Tag with an e-paper surface that displays location-based content or instructions.
With the BLE device attached to a container or item under assembly, BLE locators can calculate the tag’s location to identify where an item is. The cloud-based software provides analytics, alerting and visuals regarding each tag’s location and, therefore, its status. Prior to the BLE integration, the Logiscend system’s VIEW Tag captured location based on UHF 433 MHz transmission. By capturing the tag’s RFID transmission, the solution can identify where a tag is located in general, while the VIEW Tag can display data based on its specific location, such as directing assembly workers to complete specific tasks for a given item at a particular station.
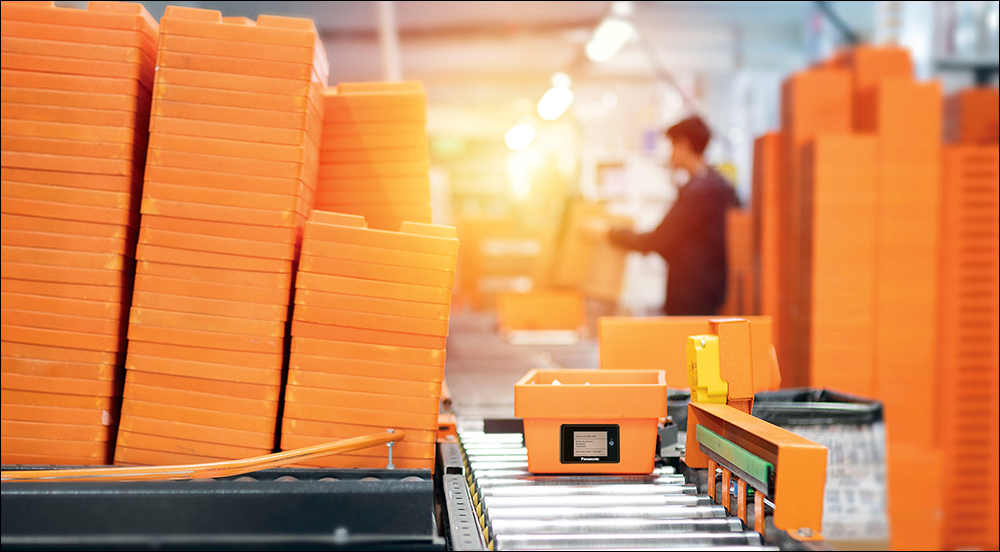
Totes are tracked at a warehouse.
By adding a BLE radio, Panasonic enables its customers to obtain specific location data so they can identify a specific workstation or staging area where a tagged item is dwelling, according to Ryan Carr, Panasonic’s product manager. That, he says, can help users locate an item on a tightly designed manufacturing floor, or in a staging area at a shipping dock. Panasonic says it will reveal its BLE technology partner at a later date.
The BLE functionality, Carr says, addresses some of the challenges manufacturers face in terms of strained production and supply chains. Companies are trying to operate with less labor due to employee shortages and social-distancing requirements, while dealing with the high cost of training new workers as they are brought onboard post-pandemic. Due to supply chain challenges, many businesses experience greater pressure from customers to increase production times. One company told Panasonic that if it fails to meet its OEM customer’s deadline, it can be charged an extra 40 percent for every late delivery.
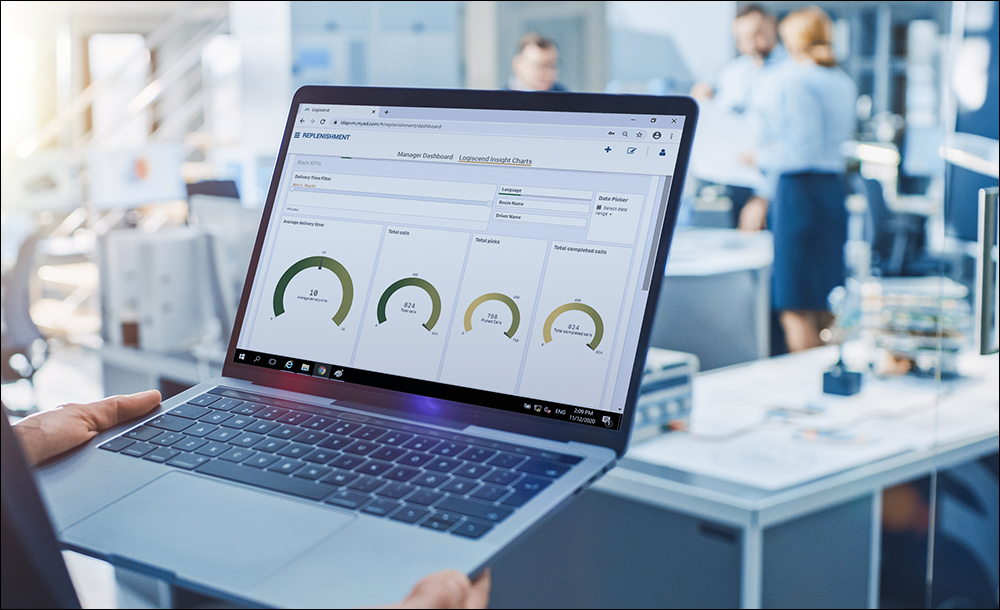
An engineer uses a laptop computer to view graphs and diagrams in trend-analytics software.
Additionally, Carr says, assembly floors often need to be highly flexible in order to change their production configuration and the location of workstations based on specific products and orders. “Everything is so tight,” he explains, “and manufacturers are putting a lot of the pressure on their suppliers” to get product assembly moving faster. Thus, businesses needed a system that would automate processes for workers onsite, as well as provide alerting for management to prevent delays.
Panasonic already addresses these issues with the Logiscend system, Carr says. “We can trigger all kinds of manufacturing-based workflows out of Logiscend,” he states, but the company sought to provide a more granular location to enable greater automation. “Other systems provide data that a product is in a room, but that’s not good enough.” With more precise location information, for instance, the system knows the station at which a specific item can be found.
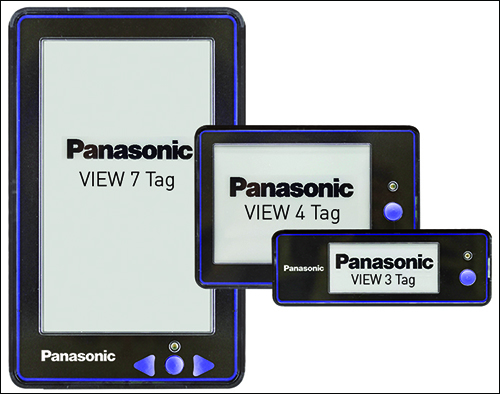
Panasonic’s VIEW Tags
The company found that other real-time location systems (RTLS) that use ultra-wideband (UWB) or active RFID can be too expensive to deploy. Therefore, its solution leverages BLE—which, Carr, says is relatively low-cost due to the prolific use of Bluetooth, which has driven down the cost of materials. Bluetooth systems allow for interoperability, he explains, so a variety of beacons, for example, could be used with BLE tags. What’s more, the power consumption of BLE is low, so the tags do not require battery replacement for around four years.
With the Logiscend system, a BLE tag is attached to a product and BLE locators are installed around a facility. While a new product is under assembly, the tag’s unique ID number is linked to that item’s details and its requirements for manufacturing and shipment. Users can customize the kind of data that is stored, along with any requirements a product may have, such as deadlines for completion, or they can set the system to send an alert if a product remains at a specific location for too long. It can also alert users if a product is ready for shipping, to ensure it is transported to the OEM before a deadline passes.
When used with the VIEW Tags, the BLE tags provide data that can be viewed by those within the vicinity. Each VIEW Tag transmits its unique ID via 433 MHz UHF RFID, Carr says, and with the help of a built-in battery, it can transmit at long range. The readers can capture UHF data from hundreds of meters away, and the BLE-based location data can help a company create a system by which the software knows exactly which tasks must be completed for a given product at each workstation. The VIEW Tag automatically displays instructions for that station and product, based on the BLE data.
The VIEW Tags enable operators to update information by pressing a button on a tag’s face, alerting the system that a product has completed a specific process, such as being approved through quality control. The software includes maps that show users where an item is located in real time, as well as dashboards on which management can identify a specific item’s location and status, or multiple parts of an order. It also enables the locating of high-value assets.
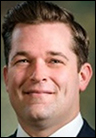
Ryan Carr
Logiscend customers are typically mid- to large-sized discrete manufacturing companies. In most cases, the businesses purchase the BLE tags, the VIEW Tags (if the RFID functionality and e-paper display are required), and the reader and locator infrastructure, and they pay an annual subscription fee for the platform, with charges for each additional service. Users can choose whether to utilize RFID, BLE or both. “Our platform doesn’t care what technology you use,” Carr states. “We will recommend the right solution—such as passive RFID, active RFID, BLE or VIEW Tags—for the customer’s specific use case.”
Panasonic expects users to gain a return on investment within about nine to 12 months, based on a reduction in training time for new employees, who can benefit from using the location-based data to view their instructions for each product. In addition, Carr says, the solution allows companies to adjust the configuration of their assembly floor for different products, and to update the related data being captured in the software. That, he says, reduces changeover times.
The BLE tags are IP65-rated, Carr says, so they can sustain an industrial environment or be used outdoors. For example, a company can extend the system’s use beyond the four walls of its factory by deploying beacons along the exterior of a building, which would enable it to detect goods in storage yards or overflow areas. Panasonic says it expects the BLE functionality to be made commercially available by the end of the year.