Gillette, an ardent proponent of using radio frequency identification technology in the supply chain, believes the technology can also provide internal benefits. The company has been running an extensive pilot since 2003 in its packaging facility in Fort Devens, Mass., where Electronic Product Code tags are encoded and placed on cases and pallets of its Venus women’s razors.
Sonoco, the packaging company that Gillette contracts to put its products into cardboard cases, applies RFID smart labels to the cases of Venus razors. Once a pallet of the cases is assembled, Sonoco affixes to it an RFID label encoded with a unique ID that links to the EPC on each case and the associated order from Gillette. The pallets are then brought through a tunnel that connects the packaging facility to the distribution center.
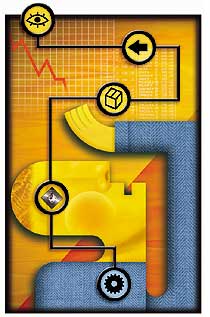
As each pallet enters the DC, a portal RFID interrogator automatically reads the EPC encoded to the pallet tag and sends it to the Provia ViaWare warehouse management system (WMS) software that Gillette uses to operate its DCs. ViaWare compares the EPC assigned to the pallet with an advance shipment notice (ASN). If it finds a match, it automatically adds the contents of the pallet into the DC’s inventory and then sends instructions to the workers specifying where the pallet should be directed. This process takes 5 seconds. Before the introduction of RFID, it took workers 20 seconds to receive each pallet of Venus razors because they had to manually scan several bar codes on the cases and pallet and make three keyboard entries to receive it into inventory.
When Venus razors are being prepared to ship out of the Fort Devens DC, an RFID-enabled forklift is used. By interfacing with the ViaWare WMS, the interrogator mounted on the forklift helps the forklift operator pick either full pallets or cases of the razors needed to fulfill an order. Once the pallets are collected or built, an interrogator mounted to a stretch-wrap machine reads all the cases on the pallet as it is being spun and wrapped. The WMS then verifies the order by matching the EPCs to the order being fulfilled. This verification process takes 20 seconds per pallet. The old system, which involved manually reading bar codes attached to the cases as they were picked and then manually comparing them with the order, took anywhere from 80 seconds to 20 minutes.
Once each pallet is assembled, it is brought through portal readers that send the tag data to ViaWare, which again verifies that the order is complete and that it’s being loaded onto the correct trailer. This takes 5 seconds, half the time it took to verify pallets of Venus razors using bar codes.
In addition to achieving these time savings, which reduce labor costs, Gillette projects that the use of RFID will lead to increased accuracy over the manual practice of scanning bar codes in each step of the process. Based on its findings with this integrated RFID system at the Fort Devens DC, Gillette says RFID could provide more than 20 percent yearly return on investment in operational costs at each of its DCs.
“While the adoption curve of RFID is driven by retailer requirements, we’re seeing the clear value of using RFID within our own four walls,” says Paul Fox, Gillette’s director of global external relations. An IBM study of RFID within a warehouse environment found that RFID could reduce picking errors and labor costs by 36 percent and reduce labor costs associated with receiving and checking goods into the distribution center by 60 percent to 93 percent.
George Spohrer, an executive with Crowe Chizek and Co., a consulting, risk management and technology services firm based in Indianapolis, says that too often companies miss the benefits of RFID. “Some people who have completed pilots focused only on tag selection, placement on pallets, etc. They didn’t see business benefits because they skipped over the business process changes that should accompany RFID integration. So now they are starting to come back around, evaluate process changes, and are starting to make some of those changes so that RFID benefits them, not just their customers. If you can use RFID to process goods better, faster, cheaper than someone else, you might get a new customer.”
Ready and Waiting
Most large WMS providers have begun offering RFID-enabled versions of their WMS software. “Somewhere between 75 percent and 80 percent of WMS systems can store EPC data,” says Philip Obal, president of Industrial Data & Information, an Ohio-based WMS consultancy. “As soon as EPC made the news, most WMS companies realized they’d need to start handling EPC data, and a lot of them jumped on the bandwagon.”
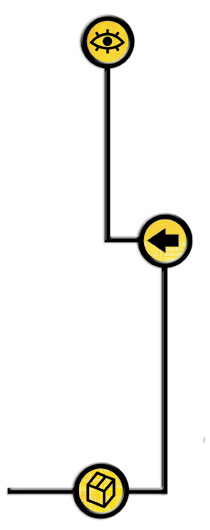
Some have built the RFID capabilities straight into their WMS, while others provide it as a bolt-on solution that runs on a separate server. HighJump, a 3M company based in Eden Prairie, Minn., offers an upgrade to its Warehouse Advantage WMS platform that enables RFID integration. Manhattan Associates, headquartered in Atlanta, offers RFID integration through its RFID in a Box platform. RedPrairie, based in Waukesha, Wis., sells an RFID-enabled version of its WMS, DLx Warehouse. Enterprise resource planning software providers that also sell WMS programs, such as Oracle and SAP, now offer RFID-enabled WMS options.
Central to the function of all of these platforms is a middleware component that filters, translates and routes EPC numbers between the RFID interrogators and the WMS. Some WMS vendors partner with Acsis, BEA Systems, GlobeRanger, OATSystems and other providers of RFID device middleware. Other WMS vendors, such as Manhattan Associates, have developed their own middleware.
End users that have upgraded their WMS platforms to process EPC data are slow to leverage the new capabilities. Greg Gilbert, Manhattan Associates’ director of RFID solutions and strategy, says 40 percent of Manhattan Associates’ customers that are tagging goods have upgraded their WMS to process EPC data, but most of those are only testing the integration capabilities on a few stock-keeping units. “The biggest limiting factor is scale,” says Gilbert. “Most are just tagging a small selection of SKUs in a few locations. The more SKUs these suppliers have to tag, the more they are going to look at switching to RFID-enabled WMS software.”
Tom Kozinski, vice president of product marketing for warehouse management and distribution at RedPrairie, says that companies need configurability in their WMS because they’ll likely transition into RFID slowly, starting with a slap-and-ship process that is slightly integrated with their WMS. These companies will also want to make sure that their WMS can track and cross-reference bar codes with EPCs, because they’ll likely be dealing with a mixed environment of bar-coded and RFID-tagged goods for years to come.
“There’s no one-size-fits-all solution,” says Kozinski. “So software has to support these different approaches—and in some cases support all of them simultaneously for the same end user.”
Depending on whether a company buys an upgrade to its existing WMS or opts for a new system, an RFID-enabled WMS can cost anywhere from $5,000 to $150,000, according to Marlo Brooke, president of consulting services firm Avatar Partners, based in Irvine, Calif.
Don’t Wait, Anticipate
Companies won’t realize the full benefits of integrating RFID with their WMS until they start tagging goods at the point of manufacture and receiving tagged pallets and cases in their warehouse or DC. “Until you’re tagging a significant percentage of goods and sending them to a large geography, I don’t know that you need to integrate,” says Simon Ellis, supply chain futurist at Unilever, one of Wal-Mart’s top suppliers.
Steve Banker, supply chain practice service director at Boston-based ARC Advisory Group, says suppliers should move tagging back to the point of manufacture when they begin tagging 40 percent to 60 percent of the goods they ship. “Once suppliers move tagging back to the point of manufacturing,” says Banker, “the DCs will realize benefits of RFID that they would not otherwise because they can automate receiving.”
RFID read rates are another factor that can determine when companies integrate RFID into their WMS processes. Ellis says the EPC Generation 1 tags that Unilever is using are not providing the types of read rates he thinks the company would need to proceed with any significant integration between the WMS platform the company uses—RedPrairie’s DLx Warehouse—and its slap-and-ship RFID tagging system. “Based on my experience with Gen 1, integrating is madness for a large company,” he says.
Unilever is currently testing Gen 2 tags, and Ellis says the results of these tests will help determine if and when the company begins tagging cases before they reach Unilever DCs, which, in turn, will affect its decision to upgrade its WMS.
But other companies don’t see integrating RFID with their WMS as an all-or-nothing proposition, and they are taking baby steps toward integration. For example, Deluxe Media, a third-party logistics provider that replicates and distributes DVDs for Sony, Paramount and Universal, has linked Manhattan Associates’ RFID Integration Engine with its WMS to flag DVD orders headed for Wal-Mart that require RFID tags.
While most companies may not be ready to start tagging pallets and cases at the point of manufacture, those that have to tag some SKUs now to comply with retailer tagging mandates could start to integrate RFID into their WMS processes. This would enable them to recoup some of the RFID infrastructure costs, through increased operational efficiencies. At the same time, they could work to improve read rates. That way they’d be ready when it was time to fully integrate RFID with their WMS. And meanwhile, they could realize some of the warehouse improvements that Gillette is currently enjoying with its tagged pallets and cases of Venus razors.
Illustration by Gordon Studer.