To help end users of RFID find the best location, or sweet spot, to place an RFID tag on a case of goods, a number of RFID service providers have devised ways to test the signal strength of tags at each possible placement. (See ODIN Announces Certification Service and Integral RFID Looks for RF Hot Spot.) Venture Research, a systems integrator based in Plano, Texas, has developed what it calls the first fully automated sweet spot test, designed especially for companies with hundreds or thousands of stock keeping units (SKUs) to tag.
Before running a case of each SKU through a detailed sweet spot test, Venture Research first performs a gross RF characterization to determine whether the case’s contents are likely to cause significant RF interference when a tag is placed on it and read. If the result meets or exceeds a set interference threshold, the SKU is put through sweet spot testing. If it falls below the threshold, however, such testing is not required because tagging the SKU is unlikely to be difficult.
“We have a customer that is one of Wal-Mart‘s top eight suppliers, and it has 15,000 SKUs,” says Venture Research President John Baker, who explains that cases for all those SKUs will eventually need to be tagged. “Our challenge was to figure out how to rapidly analyze their products and develop a strategy of determining what buckets the products fall into from a viewpoint of RF characterization.”
After determining a product’s gross RF characterizations, Venture Research collects additional data on each SKU. This data includes its SKU number, a product description, the materials the product and its packaging contain and the thickness of the cardboard case’s corrugation. The thicker the cardboard, the more insulation it provides the signal from potential interference caused by products packed inside the case. For example, a tag read on a case containing goods made of metal or liquid would more likely be read if the cardboard were very thick. This data helps determine which tags (embedded in smart labels) will provide the best sweet spot testing results.
In addition, the company measures the dimensions of the case in which the product is shipped, noting the locations of any printed matter on the case (such as logos, bar codes and text) over which the RFID smart label cannot be placed. Venture Research also takes a digital image of each face of the case.
The Venture Research system performs the sweet spot tests inside an anechoic chamber, which filters out extraneous electromagnetic radiation sources that could cause interference and skew test results. The tests must be done with as much consistency and accuracy as possible, Baker explains, so that the results of a test done one week are the same as those of an identical test done six months later.
To further ensure consistency—and to allow tests to be run quickly and without human error—the Venture Research testing system uses a robotic arm inside the chamber to move each case through a set pattern of positions behind the tag being tested. The tag is held in a stationary position, roughly 5 feet in front of an RFID reader’s linear antenna. The antenna takes a reading of the tag at each position.
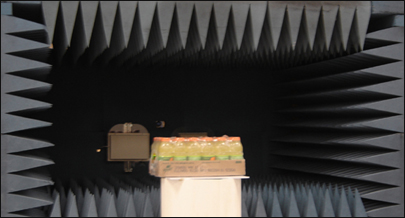
Tags are tested against all four sides of the case, and sometimes against its top and/or bottom, using a different anechoic chamber in which the antenna and tag are positioned above and below the case. Sweet spot testing across the top face is most often done with liquid products because the top of the case holds the most air and has the best chance of giving a good reading.
The carton-profiling software Venture Research developed for tag testing takes all of the signal data being generated at each location and produces a color-coded RF map of each analyzed face. Green areas show strong signal strength, while red indicates no signal or a weak signal. This map is superimposed on the image of the corresponding side of the case, so that the graphics are visible and the areas where the tag cannot be placed are noted.
Baker says Venture Research works with 21 label converters to maintain a pool of the most affordable and newest RFID smart labels on the market. The company generally begins testing with the least expensive tag first, then works with the end user to identify the best tag for their tests. Sometimes, the end user has a stock of smart labels it already uses on products being tagged, says Baker, and wants to try these in the sweet spot tests.
If the sweet spot test reveals few or no tag placements on a given case that will produce a strong RF signal with the first smart label tested, that label is ruled out and the next on the list is tested.
Following the static tests performed in the anechoic chamber, the tag is placed in what has been determined the best location on the case, excluding any printed areas that would be obscured by an attached tag. A dynamic test is then performed by placing the case on a conveyor running as fast as 650 feet per minute—the recommended upper limit for conveyable product initially specified by Wal-Mart, and mimicked by other retailers as a guideline—and through an interrogation zone around the conveyor.
A tag that performed well during the static tests will occasionally perform less than optimally in the dynamic testing. When this happens, that tag is ruled out and another tag is tested.
Once a tag is chosen and the end user begins tagging cases of an SKU, Baker says, the Venture Research software can send placement instructions to an automated RFID label applicator, regardless of the model or brand of applicator used, to ensure tag placement is done accurately. If labels are manually placed on the cases, the software can display an image of the case on a monitor to show a worker where to place the tag.
According to Baker, end users can either outsource the tag testing to Venture Research, or purchase the testing system from the company and have it installed on-site. An end user’s decision to outsource the service or bring the testing capabilities in-house will depend on how many SKUs it must tag, as well as the costs of training staff to perform the tests.
Baker notes that in the long run, when manufacturers start embedding tags into packaging materials, they will likely outsource tag placement testing to a packaging designer.
The automated testing service is available now and costs roughly $750 per SKU, though this price can be reduced through volume. Baker says the company has not yet determined pricing for those wishing to purchase the entire testing system for in-house use.