Norsk Lastbaerer Pool (NLP) is an Oslo-based company that manages returnable transport items (RTIs) for manufacturers and retailers in Norway and Sweden. It uses radio frequency identification to track and manage approximately 900,000 pallets and 1 million totes that are shipped to roughly 750 customers at 1,000 locations, nearly 98 percent of the Norwegian retail market. Each pallet is identified with four EPC Gen 2 ultrahigh-frequency RFID tags, to ensure the pallet can be read from any angle when it passes through an RFID portal, and each tote is identified with two tags. The tags are read when the RTIs arrive at NLP’s main distribution center and when they are dispatched to a customer warehouse. At some customer locations, the tagged pallets and totes are read when they are sent to a retailer DC. In addition, some customers use the tagged RTIs to manage product shipments.
The RFID solution helps NLP better manage inventory and automates manual processes, such as paperwork. Some of NLP’s customers use the system to improve their own supply-chain processes.
In Fukuroi City, Japan, a large agricultural center for rice, tea, melons and other products, logistics for individual farmers is prohibitively expensive. To streamline commerce, farmers attach RFID tags and bar codes to food packages and crates to identify their produce. Buyers then aggregate the goods to facilitate delivery, using a packaging and product management system, and to track shipments through the supply chain.
What these deployments have in common is that they both use the Electronic Product Code Information Services (EPCIS) standard to share data with their supply-chain partners and gain visibility into their business processes. EPCIS is the driving force behind the Internet of Things, in which any type of captured data on physical items is tracked and managed as the items move from company to company and country to country. That’s because EPCIS gives businesses a common language to interpret the data.
There is an incredible amount of data moving around,” says Ken Traub, president of Ken Traub Consulting. “But you have to have the right data to get business value. The EPCIS data model is unique in the way it connects RFID and bar-code data to business processes. Without EPCIS, an IoT platform can connect ‘things’ to the Internet, but the data might not have business meaning. EPCIS data makes it possible for businesses to build applications that derive real value from connected devices.”
Traub, who helped create the EPCIS standard, which was introduced in 2006, says companies are increasingly putting EPCIS into production. While numerous pilots worldwide have proved its business value, he acknowledges that companies first had to get comfortable using RFID, and they did so with deployments within their own operations. Now, they have millions of tagged assets and other things, and they’re looking at optimizing their supply chains to achieve additional benefits. “They turn to EPCIS, which offers a solid foundation for doing this,” he says.
“Businesses need to think about how to put EPCIS to use, and how it can help them operate more efficiently and cost-effectively,” says Gena Morgan, program manager at GS1 US, an organization that helps establish standards for supply-chain management. “The technology is applicable across a wide range of industries and environments. EPCIS puts information in the hands of people when and where they need it—and it ultimately drives better decision making.”
Most Industries Can Benefit From IoT Apps
NLP and Fukuroi City are just two examples of the companies and organizations that are adopting or piloting EPCIS to improve supply-chain visibility. Some companies, such as those in the food and pharmaceuticals industries, are relying on the technology to meet government traceability regulations. Others are adopting the technology to improve business processes. Tine, the largest Norwegian dairy product cooperative, uses RFID and EPCIS to track its RTIs and shipments. City’super, a high-end supermarket and retail chain in Hong Kong, is managing shipments of perishable items with temperature sensor RFID tags and EPCIS, to detect and minimize financial losses from potential food deterioration. EPCIS can also be used to track the raw materials that go into a finished product, to facilitate recalls.
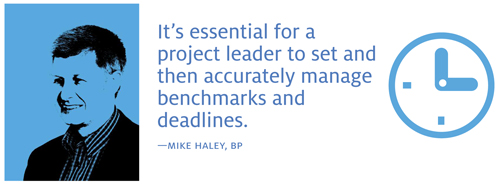
Construction, energy, logistics, rail and port organizations are also beginning to adopt EPCIS for supply-chain management and safety improvement. In these sectors, which often involve transporting assets between countries, it’s particularly important to have a standard language for sharing information, Morgan says. In Scandinavia, for example, the Swedish, Norwegian and Finnish railway transport agencies are using RFID and EPCIS to track national and international trains, to improve operations.
Manufacturers can benefit from using RFID and EPCIS to facilitate electronic proof of delivery from their suppliers, to reduce errors. And once that process is in place, they can use the technology to automate vendor-managed inventory and replenishment.
Apparel retailers are nearing the tipping point in using RFID for in-store inventory management. They are beginning to require their suppliers to RFID-tag items at the point of manufacture. “I am not aware of any retailers or suppliers using EPCIS to share data,” says Bill Hardgrave, dean of Auburn University’s Harbert College of Business and founder of the RFID Research Center. “But for RFID to be completely effective, it must be used throughout the supply chain. The visibility provided by RFID is only possible if supply-chain partners share data, and this includes retailers, who must be willing to share data such as receipt of goods with their suppliers. It would be inefficient to create proprietary solutions to share information. EPCIS provides the common framework.”
Bridging the Physical and Business Worlds
EPCIS bridges the physical world, where RFID tags and other IoT devices capture information, with the business applications their supply-chain partners use. EPCIS is an open standard, so it allows for the acceptance of data from just about any type of data-capture technology—including RFID, sensors, bar codes and mobile phones—via the Internet.
At the core of a typical EPCIS deployment is a database, called an EPCIS repository, that serves as an enterprisewide hub for storing the captured data, such as the location or condition of products and shipments, that originates from a company’s operations, Traub says. From there, the company can allow the data to flow to any business application that needs it.
How? The EPCIS repository interfaces with internal and external systems via a second component, an EPCIS Accessing Application. “It is responsible for addressing specific business needs by extracting data from the EPCIS repository as required and then delivering it in whatever form applications require,” Traub says. “The legacy systems that companies already have in place, including enterprise resource planning and supply-chain management, are often recipients for EPCIS data, and an EPCIS Accessing Application adapts the high volume of EPCIS data to the capabilities of the legacy system.” At the same time, newer applications designed specifically to process EPCIS data may connect directly to the EPCIS repository.
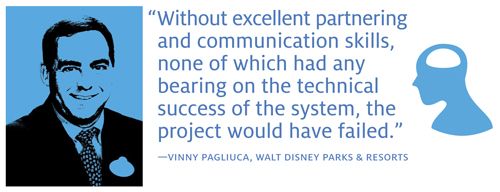
EPCIS succeeds at bridging the physical and business worlds because it standardizes the data flowing from IoT devices to business applications in a way that allows data to be shared with multiple applications and across companies. This begins with common identification for products, locations and other real-world things. Every company and organization has its own way of identifying goods or parts, but to achieve “joint visibility,” says Ian Robertson, CEO and president of Supply Chain RFID Consulting, supply-chain partners need to speak the same language. “The Electronic Product Code standards were developed precisely for this purpose,” he says. Recently, GS1 developed an RFID standard for identifying automotive components and parts so they can be tracked in the open-loop supply chain.
In addition to having common identification, it’s important to add context so IoT data can be related to business processes. “There is a key difference between a raw tag read and EPCIS data,” Traub says. “A raw tag read lacks the context of where and why the tag was read. The EPCIS data model includes dimensions of what, when, where and why, so it not only identifies the object being tracked but also the date and time, the location and the business-process step being carried out.” A business application seeing an EPCIS event not only knows the RFID tagged product was seen at the loading dock, but why it was there; it was, for example, being shipped, received or returned.
By including the where and why dimensions, EPCIS hides the type of reader and tags, reader position and other operational details that are irrelevant at the business level. This has a double benefit, Traub says. Many different business applications can run off the same EPCIS data, maximizing the return on the investment made to capture the data. At the same time, companies can evolve their RFID infrastructure to take advantage of the latest tag and reader innovations without concern about disturbing existing applications that consume the EPCIS data stream.
Companies have a wide choice of software products that store and process EPCIS data, from standalone software to add-on features of legacy and cloud-based systems, both proprietary and open-source. Most EPCIS software comes with fine-grain access control to help organizations protect intellectual property and maintain strong security. This means a manufacturer can view data about, say, product demand and inventory levels in stores, but a supply-chain partner might see only basic shipping information. Yet, both could have access to relevant regulatory data.
“Today’s supply chains have many more demands on them than only a few years ago,” Morgan points out. “EPCIS makes it possible for organizations to connect diverse data points in a relational way.”
Return on Investment
“EPCIS does not require a huge IT investment and a huge chunk of time to implement,” Morgan says. “It is already a mature and viable technology, and a proven tool.”
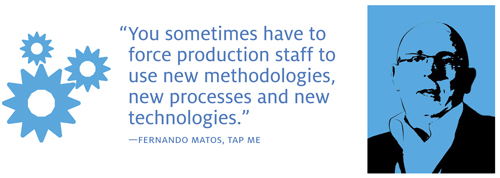
The Fukuroi City project has resulted in sales gains for participating farmers by a factor of 2.8, says Jin Mitsugi, associate professor at Keio University, who worked on the project with Tashiro Takashi, at Daiwa Computer. The efficiency of the system—sorting and packing processes take place roughly 26 times faster than before—allows farmers to wave shipping costs for orders above approximately U.S. $50, he says. In addition, Fukuroi City is using the EPCIS platform to track and manage relief supplies identified with RFID and bar codes.
At NLP, inventory accuracy has improved to nearly 100 percent, according to Tom Romanich, the company’s business manager. Missing RTIs have become outdated, Romanich reports, a substantial savings considering an RTI can cost U.S. $70. The pallets and totes are also tracked through the washing process. NLP’s inventory-management application extracts all data from the EPCIS repository, which enables managers to better understand the flow of RTIs and analyze their lifespan, to determine when they need to be replaced. The company now plans to add temperature sensors to better detect conditions during shipping, so it can boost quality control.
The flexibility of EPCIS was critical to adoption, Romanich says. “We have developed an open-loop system that works for us and our customers,” he says. “We can use the system and customize it to our exact requirements, while customers can use the EPCIS data how it works best for them. They often have a very different approach.”
One NLP customer, a major Norwegian retailer, uses the tagged pallets to track when goods have been delivered. “The system queries for the serial shipping container code (SSCC) and automatically adds dozens of pallets at a time to existing inventory, with no human interaction,” Romanich says. “The truck driver simply unloads the truck, and RFID and EPCIS handle the rest. This scenario is repeated over several thousands of pallets a week. The process removes about 45 seconds of labor per pallet.” He estimates that the 45 seconds saved per pallet equates to more than U.S. $80,000 per year.
The system also trims roughly 24 hours of shipping and transport time as goods move through the supply chain, Romanich says. In the past, the pallets or totes would sit in a warehouse until someone scanned them into the retailer’s enterprise resource planning application. Now, he says, the process occurs automatically.
In spite of the potential benefits, Romanich says, the biggest challenge has revolved around motivating customers to tap into the system and integrate their data. NLP logs every internal transaction, both receiving and sending, and the database could provide broader functionality and capabilities with partner data. “We cannot force them to use the system,” he says. “We simply try to demonstrate the benefits.”
But, Romanich adds, customers are beginning to understand the benefits of EPCIS. “Over the last couple of years, we have noticed an increased interest in using the EPC of the tote or pallet to improve and automate internal processes,” he says. “NLP thinks this is just the beginning of a future where NLP pallets and totes will be used for food tracking, internal automation and better RTI inventory control in the Norwegian retail market.”
During the next few years, Morgan believes companies across a wide swath of industries will come to recognize the benefits of EPCIS. The continuing evolution of the technology and standards—along with packaged software designed to handle various tasks related to EPCIS—will pave the way for more sophisticated and automated functionality. “As organizations become aware of the power of the technology and the granularity of the data it can deliver, adoption will accelerate and efficiency gains and cost savings will result,” she says.
“EPCIS intersects with mobility, big data and the Internet of Things,” Traub says. “It’s an important piece of the technology puzzle.”
5 Steps to Using EPCIS
Here’s how to use the Electronic Product Code Information Services standard successfully, says Ken Traub, president of Ken Traub Consulting.
1) Establish the business goals and benefits your company hopes to achieve.
2) Build the system methodically by identifying the business processes and steps in which EPCIS data will be generated, and designing the data content carefully. “If EPCIS data is well-designed and constructed, there is greater flexibility and freedom to change things in the future,” Traub says.
3) Deploy the hardware and software systems, including middleware, that can generate and connect EPCIS data, as well as front-end and mobile enterprise systems with which you can put the data to maximum use.
4) Get familiar with EPCIS by using it within your organization to let different business units share information.
5) To learn how to use EPCIS to share information with your business partners, see How to Deploy EPCIS and “Supply-Chain Visibility.”