Indonesian mobile phone operator Telkomsel has launched an RFID solution for tracking assets that brings together more than 100 previously disparate asset-management systems from its buildings throughout the country and automates data capture via handheld RFID readers at each site. Since it began rolling out the technology, the system has ensured audits take place more often, requiring less time and preventing losses, according to Pak Tio, Telkomsel’s VP of corporate service management. Once fully deployed, he predicts, the technology will provide a single, accurate view into the status of approximately 100,000 assets. The solution, provided by Cudo Communications (Cudocomm), leverages UHF RFID tags from Confidex.
The multinational telecommunications conglomerate for Internet, fixed line and mobile phone communications is headquartered in South Jakarta. It is the largest cellular operator in Indonesia, with more than 164 million subscribers. The company has as many as 200 office buildings throughout the country, each containing hundreds or thousands of assets. Employees at each site must regularly count and inspect every item, Tio says, then share the results with the company’s headquarters. Because each building traditionally had its own methods and regulations for audit counts, he adds, the resulting data was not centralized. Some buildings or branches used barcode scans to identify and count assets, while others had workers physically input data into a spreadsheet.
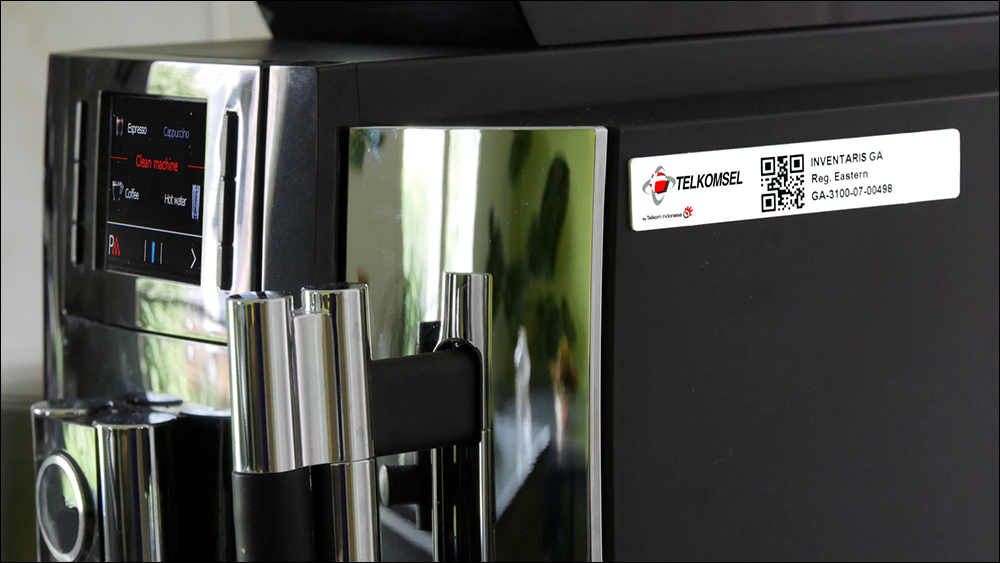
The RFID solution brings together more than 100 disparate asset-management systems from the company’s buildings and automates data capture via handheld RFID readers at each site.
In 2020, Telkomsel’s management approached Tio and asked him to align and standardize all audits. The company sought to bring its assets into view in a single system at its headquarters, Tio recalls. “My responsibility includes all 200 offices,” he says—every item at the Jakarta headquarters, as well as those at small branches where employees deliver local services. Prior to the deployment, Tio says, if someone had asked how many assets the firm had, there would have been a problem. “So I started to think, ‘How can I monitor my assets?'” He wanted to find an integrated, affordable system that would work across all sites and provide automatic data.
Telkomsel determined early on that it required a versatile UHF RFID solution to automate data capture regarding furniture, electronics and other assets—chairs, tables, lamps, coffee makers, laptops and small equipment—used to run an office. Tio worked with five technology providers, whose solutions were tested in multiple buildings. The team tested systems for ease of use, the ability to integrate the software with the company’s own software-management system, and affordability. In addition, they tested to determine how long it would take to conduct audits. “We also have to monitor time,” he states. “We have so many buildings.”
The company selected Cudocomm’s Asset Watcher asset-management system. “My pain point was to integrate the system across all our sites,” Tio recalls. Thus, the software was designed to create standardized categories of rooms and floors within each building in which assets are assigned. The software enables the firm to set up a grid of floors and rooms within each building, and to assign locations for each item. Users can then capture tag IDs in each room. With the solution’s Asset Transfer Movement feature, users can identify incorrectly placed items and return them to the appropriate location, says Yugo Budiyanto, Cudocomm’s CTO.
Each item is first tagged with a Confidex Ferrowave Classic on-metal label. That specific label was selected for its flexibility to adhere to different materials, as well as its cost-effectiveness, according to Edward Lu, Confidex’s sales director for the Asia-Pacific region. The Ferrowave Classic tag can be applied to fabric, metal, glass, plastic and wood, and it can achieve a read range of 5 to 7 meters (16.4 to 23 feet) with a handheld reader. The unique ID number encoded on each tag is linked in the software to details about the asset to which it is applied.
With the solution, users carry a handheld reader, on which they indicate the room in which they are reading tags. They then walk through the room and capture every item’s tag ID. Once they have finished counting assets with the handheld, they upload the data to the server, and that information is then available throughout the enterprise. The software resides on Telkomsel’s database and manages asset data for all sites, Budiyanto explains, while Cudocomm provides an app for Android-based mobile devices to manage the handheld reader data.
The software can identify when an asset moves from one location to another, such as a chair assigned to the 15th floor being identified in a conference room on floor 20. If an asset’s actual location does not match its assigned location, the software alerts both the user and management via the app so that it can be properly relocated. Tio says the company can access the software to view not only on which floor a tagged asset is located, but also in which specific room.
Cudocomm has provided the solution to military customers for tracking weapons, as well as to telecommunications companies. Its asset-management solutions can include 15 modules, though Telkomsel began its own deployment leveraging just three, in order to monitor asset locations, asset movements, and the import and export of data to link that information to the company’s existing SAP software.
“There are two solutions in one label,” Tio says: RFID and QR code. “If the RFID is not available—and we know technology could have a problem sometimes—we have alternative ways to capture the data.” For instance, QR code scans using an Android phone can be taken to access an asset’s identification and history via the same Electronic Product Code.
At present, workers are employing a handheld RFID reader at each facility. During the next stage, the company says it may introduce fixed readers as well. So far, Tio reports, the RFID solution has helped Telkomsel to save time during each audit, enabling more frequent audits and thus more accurate data regarding each asset’s location and status.