Bionest, a Spanish grower of organic strawberries, is deploying an RFID solution enabling the company to view the temperature of the strawberries packed at its processing facility, as well as record temperature fluctuations in a truck while the berries are transported, and monitor the temperature in real time once more at a retailer’s distribution center (DC) in Germany.
Temperature fluctuation of fresh produce during shipment is rarely transparent, and can result in spoilage. (The optimum temperature for strawberries is between 2 and 4 degrees Celsius, or 37 and 39 degrees Fahrenheit.) As a result, produce suppliers and retailers have had to accept a large percentage of produce that has become unsellable at some point between the time it was picked and when it reaches store shelves.
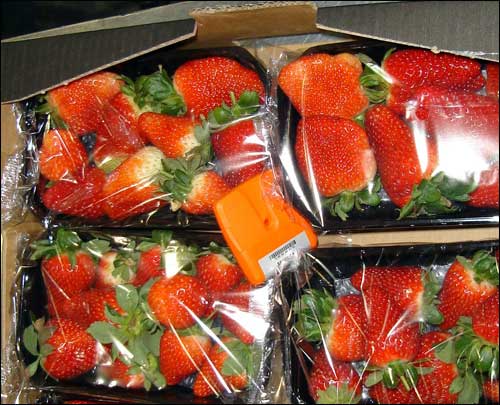
Consequently, Bionest seeks to resolve some “big temperature troubles during transport,” says Thomas Cera, the strawberry grower’s sales manager. Bionest piloted the technology on a limited number of shipments during the 2009 Spanish strawberry season (February to May), and intends to install it as a permanent deployment for the 2010 season. The solution was provided by Dutch RFID firm Ambient.
The grower hopes to improve its monitoring of temperature changes, and thereby catch temperature problems as they happen. In addition to saving products that might be approaching the high-temperature threshold (4 degrees Celsius), Bionest wants to ascertain where the temperature problems occur.
Bionest typically loads trays of strawberries onto pallets and ships them on the same day they are picked. During the pilot, pallets were tracked from the Bionest facility near Seville, in southern Spain, to the German retailer’s DC near Cologne (the retailer has asked Bionest not to reveal its name). Several shipments were tracked each week, with multiple pallets tagged and read throughout the transport per shipment. Before loading the pallets onto trucks, Bionest placed Ambient’s SmartPoint tags on top of the trays of fruit, which were then moved through a precooling process before being shipped on the same afternoon.
Ambient’s Product Series 3000 is based on the IEEE 802.15.4 standard, on which ZigBee is based. Each SmartPoint tag has a 2.4 GHz RFID chip, antenna and battery, as well as a temperature sensor certified as compliant with the EN-12830 standard, the European norm for temperature recorder devices in the food supply chain. Although Ambient and ZigBee systems are both based on IEEE 802.15.4—and, as a result, share some common features (both operate at 2.4 GHz, for instance, and provide a data rate of 250 kilobits per second)—they are also different from each other. SmartPoint tags, for example, have the capability to determine their own location in a network (in three-dimensional coordinates), using a combination of RSSI (received signal strength indication) and other techniques to calculate their own position.
The SmartPoint tags communicate with Ambient’s wireless mesh network, which consists of other SmartPoint tags, as well as Ambient MicroRouters, which receive the tags’ signals and transmit the tags’ data, along with their own location, to a GateWay reader that, in turn, forwards the information to a back-end server.For the Bionest deployment, the MicroRouters received temperature data, along with each sensor’s unique ID number, every 15 minutes, then wirelessly transmitted that information to the GateWay. “In this pilot,” explains Eelco de Jong, Ambient’s director of marketing and business development, “we installed the small wireless mesh network in the Bionest facility in Spain, and the retailer’s distribution center in Germany.” At Bionest’s facility, the GateWay used a wired Internet connection to send each tag’s ID number and temperature data, as well the time and date of those temperature readings, to the Ambient software, known as Cool Chain Monitor, running on Bionest’s back-end server.
Once the strawberries were loaded onto trucks, the sensor data could no longer be interrogated by a reader network. The SmartPoint tags have 1 megabyte of memory, however, so they continued to take temperature readings every 15 minutes, and store those results throughout the two-day journey from Spain to Germany. Upon arrival at the retailer’s distribution center, Ambient MicroRouters installed at that location received each tag’s temperature history and transmitted that data to a single GateWay, which utilized a GPRS connection to forward this information to the Cool Chain Monitor software.
Cool Chain Monitor interpreted the data, which was made available to Bionest and any other authorized user through a Web-based software application. “It’s important to note that data from two separate networks in different countries was integrated into a single database,” de Jong says. “This Cool Chain Monitor solution enables the monitoring of goods as they move along the supply chain in a single view.”
In addition, de Jong says, the SmartPoint tags contain a shelf-life algorithm developed by Ambient and researchers at the University of Bremen. The algorithm is based on time and temperature measurements, he states, and is specific for each type of fruit and vegetable. When a SmartPoint tag arrives in Germany after the trip from Spain, it will give an indication, such as “Remaining shelf-life: 3.4 days.”
According to Ambient, SmartPoint tags can be read by a MicroRouter as far as 25 meters (82 feet) away indoors and 50 meters (164 feet) outdoors. A MicroRouter can, in turn, forward the data to a GateWay up 50 to 100 meters (164 to 328 feet) away.
Bionest’s staff spent two to three hours training before using the system, Cera says. “As in any trial, the first steps were difficult, and the first sendings [of tag and temperature data] were used to personalize and optimize the system to our needs,” he indicates. Once the system was set up and operating properly, he says, “it worked quite well.”
Because of the pilot’s limited size, Bionest was unable to gauge the technology’s success in reducing wasted product. “This phase was to give us an overview of the cold chain during road transport,” Cera states. “We just wanted to know more about it—see what are the critical points, discuss it with the different actors and see how we can do a better job using this information given by the RFID loggers. Now, we would like to extend the RFID temp monitoring to our [other] customers, for the best-quality fruit.”