Minera Norge, a Norwegian firm that manufactures slate tiles and other products, is employing an RFID-based system known as SuperDAGFINN, provided by ACT System Skandinavia, to identify stone products after they are produced. The system enables the staff to track the exact locations of forklifts, as well as monitor where they place those products, using GPS units that identify each vehicle’s longitude and latitude. That information is then transmitted to the company’s back-end system in real time.
Minera began utilizing the system in May 2009, with incremental additions as employees have gotten accustomed to using it. Initially, the firm began by simply attaching EPC Gen 2 RFID tags to pallets. Currently, however, the system is being used to track pallets from the time they are loaded with product until they are shipped, says Knut Fossum, the copany’s manager of production. The system helps the firm reduce errors, such as incorrect shipments and lost products.
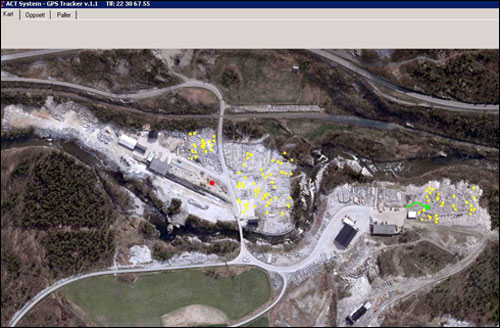
Minera Norge cuts slate rock into tiles and blocks used for flooring, walkways, roofing and other applications. These products are then stored in an outdoor yard on pallets, where they await shipment. Because of the yard’s size—more than 20,000 square meters (215,280 square feet)—and large quantity of products stored therein, the company could easily lose track of pallets loaded with a particular order. In the winter, the firm reports, the problem can be exacerbated, as the pallets are often buried under a layer of snow. So far this month, there has been approximately 1 meter (3.3 feet) of snow over the products in the yard, according to Jan Erik Evanger, ACT System Skandinavia’s managing director.
The company initially considered a bar-coding solution, but that would require an employee to climb down from his forklift, brush snow or dirt off the bar-code labels and then read them with a scanner in order to determine what a particular pallet was loaded with, and whether it was the one he was seeking. Instead, the firm installed the ACT system, which includes RFID interrogators on the manufacturing conveyors, as well as on the forklifts. ACT’s SuperDAGFINN software integrates with Minera’s enterprise resource planning (ERP) system, where its VISMA software, provided by Amesto, stores information regarding shipment orders and their status, such as completed, in storage or shipped.
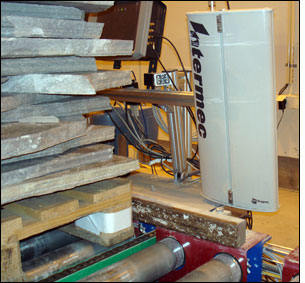
Typically, eight stonecutters work alongside the conveyor at any given time. Each worker first uses an ID card to log himself in to Minera’s ERP system at a station that includes a touch screen to display data for the manufacturing staff, the PC where the ERP software resides and an RFID reader. The ID badge has an ultrahigh-frequency (UHF) EPC Gen 2 RFID tag embedded in it, and the interrogator captures its ID number, which links to the employee’s name in software, thereby logging that individual in for work. The employee can view a list of orders to be completed and then press his chisel against a prompt on the touch screen to indicate he has taken a specific job, and to request the stones he would need to cut into products to fulfill that order.
Data regarding the product, order and customer are stored in Minera’s VISMA ERP software. That information links to the ACT software, which displays the orders on the screen, as well as manages data related to RFID reads on the assembly floor. The employee cuts the stone into tiles or other products, and those finished products are then loaded onto pallets. Each pallet has a UPM Raflatac UHF Gen 2 RFID tag attached to one corner, encoded with a unique ID number and printed by SATO printers.
The pallets pass down a conveyor to a scale, where they are weighed (based on the weight, the company can deduce the total meters of tiles on each pallet) and then moved to an Intermec RFID reader portal, which captures each tag’s unique ID number and links the pallets with the order and the product’s weight in the ACT software. An RFID tag with an order number printed on the front is then attached to stretch wrap on the side of the pallet’s product. “The stretch wrap tag provides redundancy in the event the tag placed on the pallet is unreadable,” Evanger explains, “as well as offering printed data the customers can read.”
Each of the two forklifts that deliver the pallet to the yard for storage is equipped with a GPS system, as well as an RFID reader. When a forklift picks up the pallet, its interrogator captures the tags’ unique ID numbers, and ACT software displays the product information on the forklift’s screen. With this data, the driver can confirm that he has the correct pallet. As the driver moves the pallet though the yard, the GPS unit determines the vehicle’s location, which the forklift reader unit transmits, along with RFID data, to the back-end system via a wireless 802.11 connection. In that way, the ACT software on Minera’s back-end system knows where the specific product is located in real time as the forklift moves around the yard. After putting the product down, the forklift pulls away from the pallet, and the RFID reader on the vehicle no longer receives the unique ID number from the pallet’s two RFID tags, thus indicating, in the ACT software, that the pallet has been released. The forklift’s location at that time is then saved, in order to indicate the location of the pallet.
Upon later being instructed to pick up a pallet to load onto a truck, a driver can enter the order number for the products he seeks into his onboard RFID/GPS unit, and a screen attached to that unit will then display an icon on a map of the yard, showing where that particular pallet was placed. In addition, the screen displays an icon of the forklift itself, which the driver can use to determine his location in relation to that pallet, and also provides directions that the worker can follow in order to reach that pallet.
The entire system took four weeks to install, Evanger says. The only problems, he notes, have involved a reader antenna being damaged as a forklift is submerged in water, when employees move the vehicle into a river to be washed. The units do not suffer from exposure to water related to rain or snow, he says, but in the future, the company intends to be more careful about how it submerges the forklifts—by lifting the forks on which the device is installed, prior to placing the machines in the river.
According to Evanger, the benefits have been faster location of products and greater accuracy. What’s more, he adds, when the product is picked up and loaded onto a truck, a forklift driver can press a prompt on his vehicle’s screen to indicate that the product has been shipped, and an advance shipping notice is automatically sent via e-mail to the customer; the invoicing process is then launched, making billing faster and more automatic.