After two years of trialing and then deploying an inventory-tracking RFID system for a large European apparel retailer, sister companies IER and SDV are now marketing a solution based on that deployment. The offering, known as iD by SDV, combines SDV’s software and logistics services with IER’s RFID tags and readers, enabling users to track goods from the point of manufacture to the point of sale (POS).
The European retailer deployed the original solution to track inventory at hundreds of its stores worldwide, according to Béatrice Piau, SDV’s marketing manager. The next phase, she says, will be to expand the system to include reader portals at a distribution center, and thereby monitor products from that warehouse to the stores. In the meantime, iD by SDV is being trialed by other retailers.
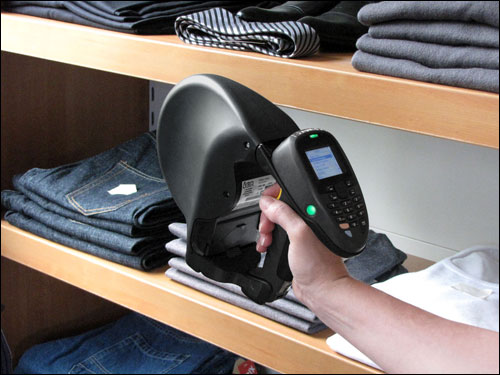
SDV and IER are owned by French investment and industrial holding firm Bolloré Group. SDV is a supply chain management company focused on such industries as retail, aerospace, food, health care, and oil and gas. IER makes RFID hardware and other electronic products at two manufacturing facilities in France, targeting use cases such as air and public transportation, as well as logistics, access control and retail. At one French manufacturing facility, IER creates tags, while at another it produces RFID readers and RFID printer-encoders, along with non-RFID printers. IER began working in the RFID space approximately 10 years ago, says Talel Hatira, the firm’s RFID solutions sales manager. Initially, the company focused on RFID tag use in the airline industry, but it began developing technology for the retail sector about five years ago.
During the interim, Piau says, SDV found that many of its retail clients were suffering from a discrepancy between theoretical inventory (what they believed they had in stock) and actual stock. Theoretical stock often was simply wrong, she explains—and if the stock at a store was inaccurate, the companies were missing sales opportunities. Missing inventory is a greater problem today than it was prior to the advent on online sales, she notes, since customers can simply purchase a product from another company via their Internet-connected smartphones if the item they seek at a store is not in stock.
Together, SDV and IER began developing a scalable solution for one of SDV’s customers—a large European apparel retailer with stores worldwide. While the retailer’s priority was to track goods in-store, it sought visibility into its inventory in the long term, from the point of manufacture to the point of sale. Therefore, iD by SDV is intended to enable users to tag goods at the factory as they are manufactured, or at SDV’s network of warehouses and logistics hubs, and to then track those products through DCs or other locations along the supply chain, into the store and through the point of sale.
IER manufactures finished RFID labels that can be applied directly to garments, and also supplies inlays to service bureaus that a customer can then convert. The company reports that it will be able to produce more than 150 million tags annually by next year. With that increasing capability, IER will be able to supply iD by SDV tags to clothing factories in the Asia-Pacific region and other locations. In the case of the large retailer for which this solution was developed, tags are already being applied to some garments at the point of manufacture. Therefore, once the retailer is ready to expand its use of the technology, it could immediately begin reading tags at other points in its supply chain.
Here’s how the iD by SDV solution works: First, a tag is applied to a garment at the factory or at an SDV hub, and it can then be encoded onsite, or simply be read in order to create a digital record in the SDV software, linking the RFID tag’s ID number with the specific item to which that tag is affixed. The software can either be hosted on SDV’s own server or integrated with the user’s existing management software on its own server. “Our solutions adapt to our customers’ needs and to their level of complexity,” Piau states, “to include a scalable range of tracking capabilities, management of logistics platforms and global supply chain monitoring.” The tag could then be interrogated by an IER fixed reader at various points along the supply chain, such as when the garment is shipped from the factory or an SDV hub to a distribution center, and again when it is received at that DC. It could be read again as the clothing leaves the DC and arrives at the store. Store personnel could then use IER 680 handheld readers to conduct periodic in-store inventory counts.
This final step in the process—the counting of inventory at the store—is where SDV’s initial customer has been using the RFID technology. As tagged goods are received, workers utilize an IER handheld reader to capture the tag’s ID number, which is linked to the stock-keeping unit (SKU) data, and create an update in the SDV Information System software residing on the company’s server, indicating which items are present at the store. As goods are sold, the store’s management software shares that information with the SDV software, so that it can identify which goods are gone from the premises and will thus need to be reordered. Inventory checks are typically conducted every three weeks.
SDV Information System software can also generate an automatic shipping order for the distribution center in the event that the quantity of goods of a specific SKU drops below a selected threshold.
The solution is designed not only to boost sales by reducing the incidence of out-of-stocks, but also to be used for anti-theft applications, if an RFID reader were deployed at the store exit and linked to POS data to identify when an unpurchased item is leaving the store. Further upstream, as goods are transported from the factory to the DC and on to the store, the data culled from SDV Information System software could enable users to measure the carbon footprint related to transportation, and thereby reduce carbon dioxide emissions by making the supply chain more efficient.
Since the global retailer began using SDV’s RFID solution about two years ago, it has reported a 10 to 12 percent increase in sales due to accurate store inventory replenishment. Its next step will be to begin tracking goods between the distribution center and the store, thereby creating a more accurate record of which goods have been shipped, and thus when they will arrive. In this way, the store can also compare what the DC claims to have shipped against actual shipping data, via RFID reads.
At present, Hatira reports, the retailer is employing two IER 680 handheld readers at each of up to 1,000 stores, though it plans to also install IER RFID fixed reader portals at the distribution center for this second phase of the installation.
Throughout the two years during which the technology has been tested and deployed, Hatira says, “We’ve derived a lot of knowledge from this.” As a result, SDV and IER developed the packaged offering known as iD by SDV, and began marketing it during summer 2013. “We are working with new customers,” he states. Those potential customers consist of retailers that could purchase the solution directly from SDV, as well as from integrators that are already providing RFID middleware installation and would become SDV’s partners in managing those customers’ supply chains.