The death of a beloved pet is difficult enough, but waiting for cremation and the return of an ash-filled urn, as well as the potential for mistakes, make the process harder for some people. That is why San Diego technology company Angelpaw has begun selling a solution that helps pet owners know where their dog’s or cat’s remains are as services are completed for a veterinarian.
The solution, now being deployed by pet crematoriums around the United States, consists of ruggedized plastic RFID tags on pet cadaver bags, as well as UHF RFID readers deployed at each point along the chain of custody or at each processing station. Running the data captured from those readers is cloud-based software that captures each tag ID event and updates the software to indicate the chain of custody’s status and the processes the remains undergo based on a pet owners’ request.
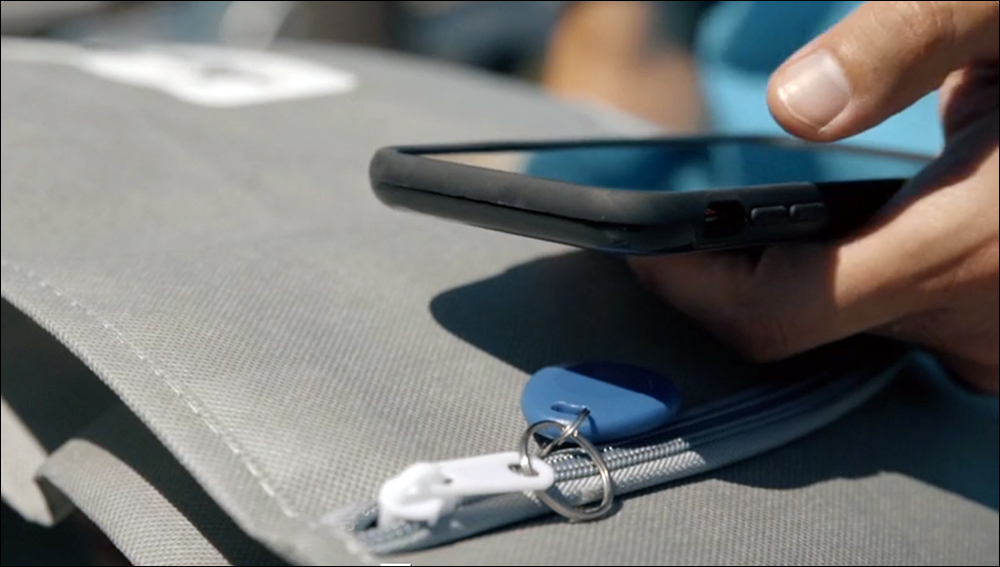
Employees can track each step of the process using a handheld device.
James Byler, Angelpaw’s founder and CEO, is an entrepreneur who had already created multiple startups when he developed the technology and launched a company to provide it to pet owners, based on his own experience. His dogs had died, he recalls, and when their remains were cremated, the veterinarian’s office had little information to offer him regarding the location of their cremains, or how they were being cared for. In fact, Byler found, the management of pet remains typically relies on paper records as those remains are picked up from a vet’s office and transferred to a crematorium, then when the cremains are later returned, so that they can be provided to the owners or be disposed of, as requested.
If the owners have specific requests, such as a paw print or a tuft of fur, the process can become more complex. The lack of information, Byler says, creates undue stress for the “parents” and can often lead to errors. To put his new technology to the test, Byler opened a pet crematorium in San Diego under the same name as that of his new company. “I built a technology platform to do a couple of things,” he says, “to fulfill the requirements of a crematorium, ensuring errors are never made, no animals are lost and the cremains are tracked properly.” The solution also provides an automated way to prove the remains were properly handled.
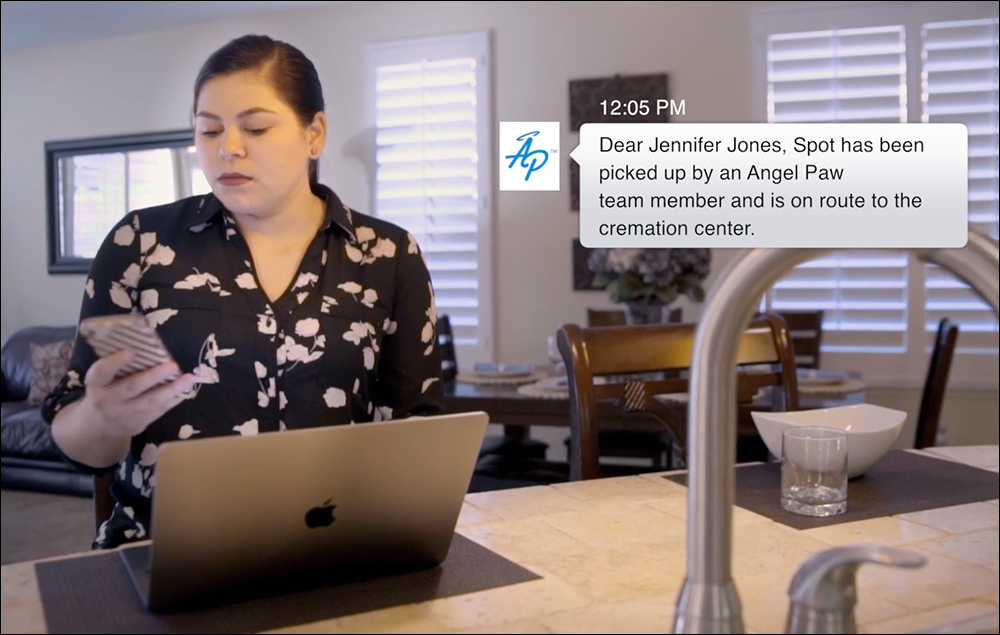
Pet owners receive messages updating them about their pets’ cremains.
Some people want their pets’ cremains to be disposed of, while others want them back with a variety of other services. With Byler’s system, a veterinarian’s office would first place the body in a cadaver bag, then apply a passive UHF RFID tag provided by the crematorium. The veterinarian staff would use a desktop reader to capture the tag read, then link the tag’s ID number with the pet’s information and the specific instructions for the remains. This is all accomplished on a read-write application loaded on a handheld reader, which is plugged into a laptop or desktop computer via a USB port.
“That starts the tracking process for the remains,” Byler explains. The data is then stored in the cloud-based software and can be accessed by the crematorium. Upon picking up the remains, the crematorium’s field representative scans the tag ID using a handheld running the Angelpaw app, which shows the driver information indicating which animals are required to be picked up at each site. The tag-read data shows which animals were picked up, and that change of custody is updated in the software. At the crematorium’s receiving area, a fixed RFID reader captures each cadaver bag’s ID as the truck arrives.
Crematoriums operate multiple stations where specific services are conducted—typically, between two and 12 stations altogether. The remains then undergo a set of processes at each station, such as creating a clay paw imprint or cutting a tuft of fur. A large screen at the site displays details regarding each animal whose tag has been read, along with the services it requires next. The remains do not move to the next process until the prior one has been completed, so if a tag read is captured out of order, an alert can be displayed. That mechanism in the system ensures no process is missed prior to cremation, Byler says, adding, “There is a lot of failsafe built into the system to ensure a mistake does not occur.”
The tag is removed from the cadaver bag before the remains are put into the oven, then is placed on the container in which the cremains are placed, and the box is prepared for return to the veterinarian’s office. The pet’s owners can access that data if they wish to view when the remains have been processed and are being returned to the vet. The system can be set up to send messages indicating the remains have been picked up or are being returned as cremains to the vet’s office in an urn.
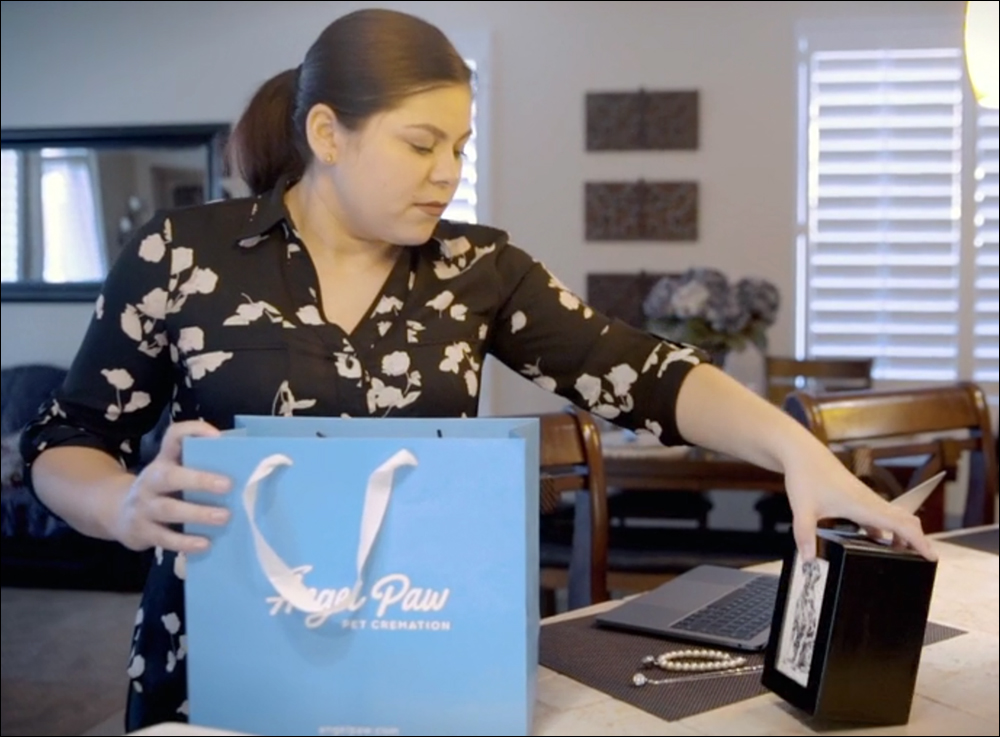
The cremains are ultimately delivered to the pet owners.
This information, Byler says, “gives them peace of mind by [letting them] understand what is happening during the final destination of a beloved pet.” Because no such similar systems were in place when he began developing his solution, Byler had to perform some customizing. He opted to use an Avery Dennison tag modified to be ruggedized by label company Northern Apex. In that way, the tags can sustain temperature changes when placed in freezers or exposed to water, as well as high temperatures near the oven. The readers are provided by Zebra Technologies.
The system was in development since early 2019, Byler says, and he calls it the fastest-growing solution for tracking pet cremains. Other such solutions, he reports, rely on manual paper- or barcode-based records to manage data. “We’re the first company to digitize the entire life cycle,” he states. The system is already being deployed at crematoriums and veterinarian offices across the United States. Baltimore-based Regency, which operates crematoriums throughout the country, is among the technology’s first implementers.
After releasing the solution, Byler says, “I didn’t realize how desperate the industry was for something cutting-edge. It’s been overwhelming.” According to reports from his customers, he adds, operational efficiency increased substantially, with error rates down to zero. Large companies can now view how much time it takes to complete services at each of their sites, as well as identify where processes are slower and where retraining may be necessary.
Next year, the company plans to expand into medical waste tracking for the pet industry. “We’ve started to scope and build the medical waste tracking system,” Byler says, which will help veterinarian offices track the chain of custody of their hazardous waste, such as needles, X-rays and other materials used in surgical procedures. In such a case, an RFID tag would be applied to reusable containers, and the system would provide proof that waste was properly disposed of, thereby enabling vets to share that data with regulatory bodies.