European manufacturer Roba Metals has increased its product shipping volume via radio frequency identification, improving the efficiency and accuracy of how it locates and identifies loaded pallets scheduled for delivery to a customer. By reducing search times for order-pickers and confirming the identity of each pallet, the RFID system makes it possible for Roba Metals to ship more products faster, and to meet a growing demand from its customers.
The solution, consisting of UHF RFID tags on pallets, readers on forklifts and cranes, and middleware to capture and interpret read data, was provided by Belgian technology company Aucxis RFID Solutions. Aucxis also supplied the front-end software that provides the data to be viewed and managed by the metals manufacturer.
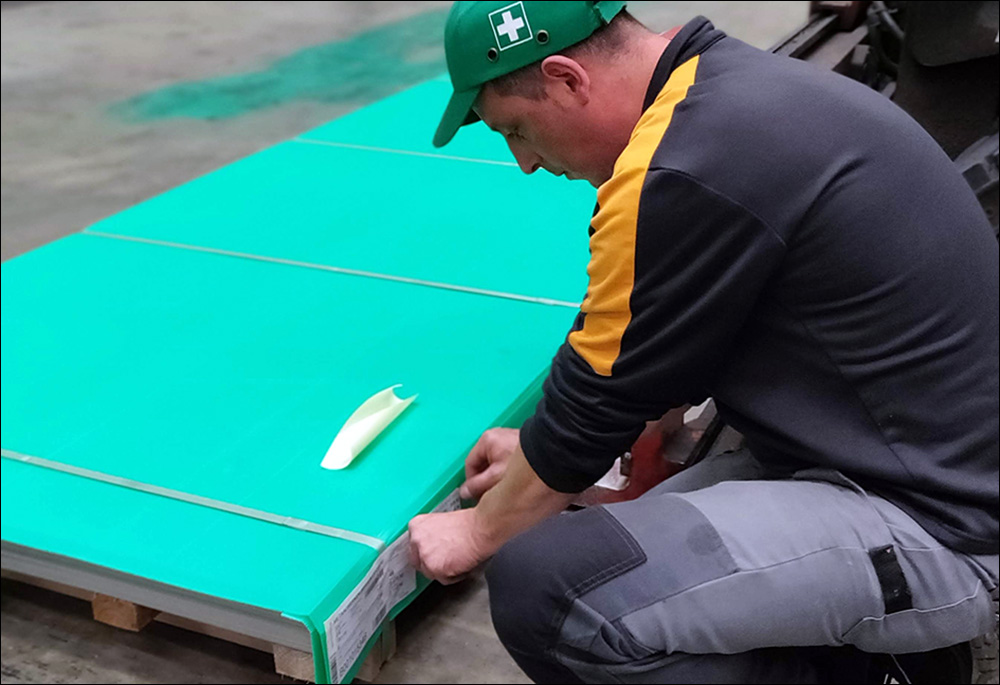
A worker applies a tag to a pallet.
Roba Metals, headquartered in The Netherlands, supplies steel, stainless steel, aluminium and other non-ferrous semi-finished products to customers worldwide. The company produces approximately 5,000 metal plates each month, says Gert Machon, Roba Metals’ production manager, and products are manufactured and sized according to specific orders. The company’s production site, located in the city of Genk, Belgium, has an average of 7,000 pallets in stock, of which about 1,000 are delivered to customers on a weekly basis.
Thirty-five employees are involved in the firm’s production and logistics flow processes. In order to locate the correct pallets for shipment to a customer, and to ensure that the right pallets are placed in the proper vehicles, Roba Metals had historically used barcodes. Workers carried a traditional barcode scanner, with each pallet’s barcode ID and other details stored in a Microsoft Excel file, along with the pallet’s warehouse location.
Locating pallets loaded with product, as well as identifying them prior to shipment, was often a time-consuming process, Machon says, often requiring a few extra minutes or more to ensure the right pallet was ready for shipment. That limited the number of shipments that could be picked and loaded daily for customer orders.
As a growing amount of storage space has been built, and since pallet locations are not always registered, search have times increased. At the same time, delivery times are becoming increasingly shorter, with customers often expecting delivery just one day after placing their order. Roba Metals, therefore, sought a real-time location system that could be linked to its warehouse-management software (WMS). The company met with Aucxis in 2018 to automate the process of locating and identifying loaded pallets, says Lauran D’hanis, an Aucxis account manager and business consultant.
Aucxis recommended a UHF RFID-based system, using its ATLAS Forklift Track&Trace solution, for automatic location and load control. That same year, Aucxis conducted a proof-of-concept at Roba Metals’ Genk site to confirm that the RFID application was economically and technically viable. The pilot was conducted in a 20,000-square-meter (215,300-square-foot) area of the plant, divided into four halls through which goods are transported. Each hall has a bridge crane that travels on a ceiling rail to move goods to and from storage areas. Based on the pilot’s success, Roba Metals opted to proceed with a full deployment throughout its facility.
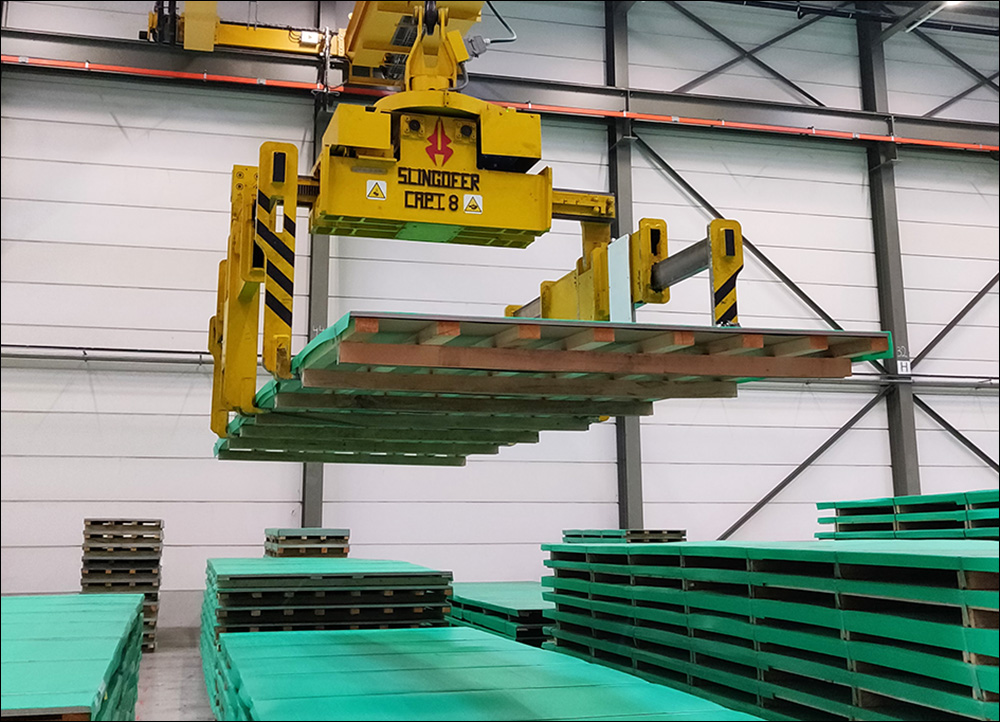
A bridge crane lifts tagged pallets.
Rolls of stainless steel are reprocessed into plates cut to size, which are then loaded onto pallets and stored onsite. Protective corrugated sheets are placed over each pallet, with a barcode label attached to it. The company also prints two UHF RFID tags encoded with the product ID, which it attaches to the protective wrap. A forklift picks up the pallet and transports it to a drop zone, where the bridge crane then places it in storage until customer orders come in. When a pallet needs to be loaded onto a vehicle destined for a particular customer, the process takes place in reverse: the crane picks up the pallet and delivers it to the drop zone, then a forklift then loads it onto a truck.
An RFID reader is mounted on each crane and forklift. The two tags are situated on the pallet in such a way that a tag read can be captured by either forklift or the crane. On the latter, the RFID reader antenna captures the unique ID number encoded on each loaded pallet’s tag as the crane picks it up, and the system links that data with its exact position, based on x and y coordinates determined by a laser-positioning system provided and installed by Aucxis.
Following confirmation by the equipment operator using a touch screen, the data is forwarded to the WMS, where the pallet’s location is stored and displayed. A forklift operator can view that information on the onboard tablet touchscreen via the Aucxis software, and he or she can then proceed to the drop zone to pick up the required pallet. The forklift reader captures tags on any pallets being picked up.
To help locate tagged pallets being transported by forklifts, Roba Metals installed UHF RFID tags in the floor concrete to create a grid pattern. The forklift reader interrogates the tags as the vehicle passes over or near them. Using the touchscreen on the forklift, the operator can view the drop-off location to which the pallet he or she has picked up needs to be moved. The location data is confirmed by the operator as he or she drops the pallet off, and the updated information is sent to Aucxis’s Hertz middleware via Wi-Fi. The middleware interprets the data and integrates it with Roba Metal’s own WMS.
“A thorough tag-selection process was indeed required,” D’hanis says, “but the biggest challenge lay in the combination of different ways of tagging and tracing.” With two tags on each pallet, the system ensured that pallet tags could be read by either the cranes or the forklifts. Aucxis also selected the appropriate RFID readers on the bridge cranes and forklifts, he adds. Altogether, the solution took about a year to implement.
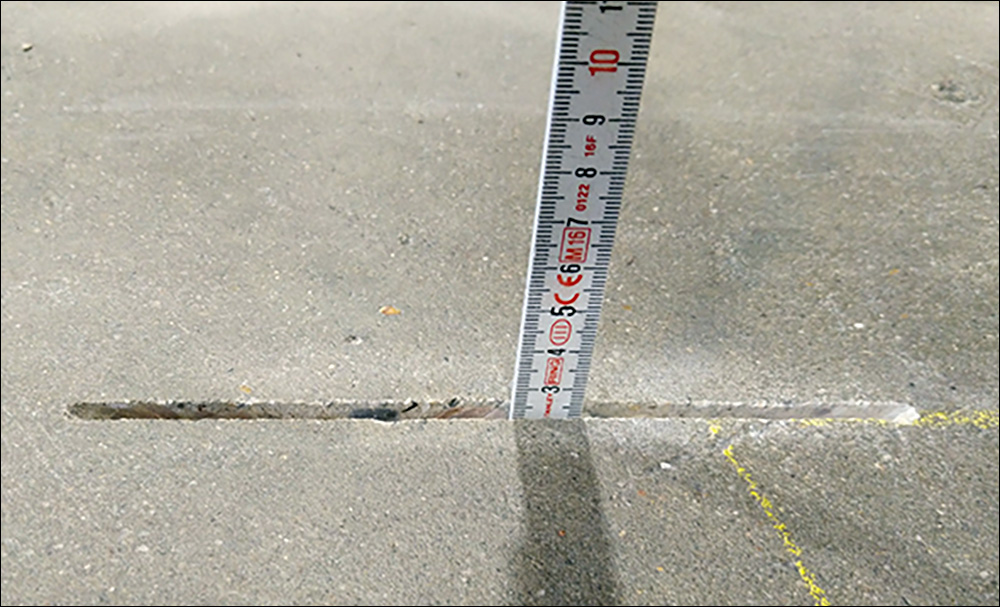
Roba Metals installed tags in the floor concrete to create a grid pattern.
At present, Machon says, “We read our tags every time a pallet is moved, to have a correct location. This can happen many times during handling, moving and loading.” With each pallet’s unique ID number captured automatically, he adds, “We are able to ship more goods in a bigger warehouse,” during the same number of work hours.
“Thanks to the ATLAS Forklift Track&Trace solution,” D’hanis reports, “every step of every pallet is monitored throughout the logistic flow, from storage after production to loading on trucks for transport.” In the long term, Roba Metals is considering implementing a feature by which RFID tags on pallets would be read as cargo was loaded onto vehicles departing for a customer site. That process would automatically update the cargo’s status in the WMS, he says, and could automate the printing of the transport documents, as well as prompt the accounting department to create and send invoices.