South African company Much Asphalt reports that it has reduced errors and labor time at its collection sites, thanks to an RFID solution that automatically identifies the trucks that remove product from its site and links them with the volume of asphalt collected. The solution, provided by South African integrator Milestone Integrated Systems, captures the identity of each entering truck as it is weighed while empty, then again as it exits after being loaded, thus creating an automated record of which company received each product, as well as how much and when this occurred.
Milestone installed Keonn‘s AdvanReader UHF RFID readers and Advantenna SP12 antennas at two sites, with the technology slated to be deployed at all 16 Much Asphalt locations later this year. Each truck that reports to the asphalt sites has been assigned a passive UHF RFID tag, attached to its windshield, which transmits data to readers at the entrance and at the departure weigh bridge. With the technology in place, Much Asphalt says it has been able to eliminate human errors related to manually inputting data regarding vehicles and their loads as they travel through the company’s facilities.
Much Asphalt is the largest commercial asphalt producer in southern Africa. It is owned by AECI, a solutions provider for mining, water treatment, agriculture and other industrial uses. The company operates 16 plants throughout South Africa, where it makes hot and cold asphalt products, according to Brad Straiton, Much Asphalt’s business analyst.
Construction firms and other customers enter the company’s sites to collect asphalt, for which they are then billed according to weight. Each site sees varying amounts of traffic, Straiton says, though the RFID technology was initially deployed at one site in Cape Town, where approximately 30 trucks report on a daily basis. The second test site, also located in Cape Town, receives up to 170 trucks per day.
Prior to deploying the RFID technology, the company utilized a manual process of data collection that required human labor. A weigh bridge operator would identify each vehicle entering and leaving the facility, and would record the truck’s details, along with information about the load being purchased. The workers would then enter the data into the computer system, Straiton says. This process, however, was vulnerable to the manual operator making mistakes during data input, which could lead to incorrect billing, thus resulting in losses for the company.
In addition, Much Asphalt needed to boost efficiency at the weigh bridge. With a large amount of traffic at each site, Straiton explains, speed is important to prevent queuing at the entrance. To that end, the company began working with Milestone in 2019 to create a solution. Testing commenced last year at the first site, where tags were applied to truck windshields, and the truck company’s details were linked to the tag’s unique ID number in the software, using a handheld RFID reader to commission each tag before it was applied to a particular vehicle.
The company has two weigh bridge buildings, one at the entrance and the other at the exit. There is one fixed reader and antennas at each weigh bridge site, and Milestone used the existing structures to mount the RFID antennas. Jim Haantjes, Milestone Integrated Systems’ sales executive, says the read distance from the antennas was found to be sufficient. As trucks pull into the entrance, the drivers stop at the weigh bridge, where the antennas capture their windshield tag ID. The reader then forwards that data to Much Asphalt’s software, indicating that a specific vehicle has arrived. The tag ID is linked to the truck’s weight as it is measured at the scale, and the driver then proceeds inside.
After the truck is loaded, the driver takes the vehicle to the next weigh bridge, near the exit, where the RFID tag will again be interrogated. That ID number, along with the vehicle’s new weight, is forwarded to the software, where the full load weight is calculated. That action prompts the system to create an invoice containing all the relevant data. Typically, Straiton says, loads weigh between 7 and 10 tons at the first test site.
According to Haantjes, Much Asphalt’s software was modified to automatically receive the weigh bridge and truck ID data when the vehicle drives onto the entry weigh bridge. Software automatically computes all other information regarding the collected load, the company, the billing address, truck ownership and so forth. That posed a challenge for Milestone, Haantjes recalls. The software needed to be configured to accommodate the data supplied by the RFID tag reads using Keonn’s software, and to then link that data to the rest of the in-house software process, creating an invoice for the truck company. “This was done by Much Asphalt’s software specialists,” he says.
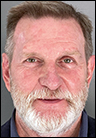
Jim Haantjes
The encoding process for the RFID tag being applied to each vehicle posed another challenge, Haantjes says. Therefore, the company built the system to capture numbers from vehicles’ license plates, and the handheld reader was used to interrogate the new tag being applied, thus linking the license plate data with the ID number in order to create a record in the software. Keonn assisted by creating an app on the handheld reader for encoding the truck’s RFID label, according to the vehicle’s license plate number. Much Asphalt’s IT department used Keonn’s application programming interface.
Following extensive testing at the first site, the system was expanded to a second facility to identify how the technology worked in a greater variety of scenarios. At the second test site, loads typically weighed between 10 and 14 tons per truck. Both sites were located close to the company’s head office in Cape Town, where personnel assisted in monitoring the RFID testing. Since the solution was taken live, Much Asphalt reports, the benefits have been near-100 percent accuracy of data regarding products purchased onsite.
Straiton says the system has ensured that the correct information is automatically captured when a truck arrives at a weigh bridge, and that human input errors are eliminated, thus preventing financial losses. The solution is working well so far, he reports, and it is expected to be rolled out to another 14 sites throughout South Africa. “We are also looking at other ways to utilize RFID in the business to gain further advantages,” Straiton states.