A company in Queensland, Australia, is using radio frequency identification to improve safety for its employees during construction of one of the country’s biggest road projects.
The North-South Bypass Tunnel Project is a $2 billion toll road that will link the two sides of Brisbane, divided by the Brisbane River. When completed in early 2010, the 6.8-kilometer road will be the longest road-tunnel in Australia.
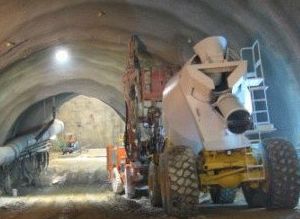
RiverCity Motorway, the firm overseeing and financing the project, awarded Leighton Contractors and Baulderstone Hornibrook Bilfinger Berger Joint Venture (LBB JV) the contract to design and build the bypass’s dual 4.8-kilometer-long tunnels (one for northbound traffic, the other for southbound). The joint venture turned to NLT Australia, a provider of underground lighting and digital communications solutions for the mining industry, to assist in developing and implementing a system that could locate any of its 1,700 staff in the tunnels.
NLT was contracted to install a digital network with an open standard Ethernet backbone capable of supporting two-way messaging, environmental monitoring and a real-time location system. It opted for an RFID system that transmits an employee’s location to a wireless node, which forwards the data to bespoke software.
The RFID system uses Wavetrend dual active and passive tags. The tags’ active transponders transmit at a frequency of 433 MHz and at a range of up to 8 meters, and can provide information according to location, time or individual details. The tags’ passive inlays operate at 13.56 MHz MHz and contain NXP Semiconductors‘ Mifare chips, complying with the ISO 14443-A standard.
“This is a high-profile project, and the company can not afford any incidents,” says NLT professional services manager Matt Macer. “It is a dangerous environment, with normal hazards of digging underground complicated by the presence of heavy machinery and lots of vehicle movements. The main benefit of an RFID system is that it allows the company to know who is in the tunnels, and where, at any time. The tunnel-boring machine [TBM] is more than 250 meters long, and there is a lot of work going on at any time across the length of the vehicle, so it is vital that the company can account for everybody underground.”NLT issued personnel tags to all 1,700 employees, as well as to any visitor to the site, and has installed Wavetrend 433 MHz RFID readers.
“We have also placed readers at the entrance and exit points, as well as muster points above ground, where staff gather in the event of an emergency,” Macer says. “But in addition to knowing where everyone is for safety reasons, the software can also track people by skills or qualification. So, if the company needs to find an electrician or a first-aid worker, it can search the database and find the person closest the situation. It allows the company to move its staff around more efficiently and effectively.”
David Sheldon, TBM lead electrical engineer with LBB, says RFID technology was chosen to ensure best-practice safety standards during construction of the tunnels.
“The tunnel can be a hazardous environment, and if something was to happen in the tunnel, then we must be able to locate our staff and get them out as quickly as possible,” he says. “RFID technology is a modern solution, and it has been very successful in locating our personnel.”
Sheldon says the tunnels currently extend more than 700 meters, with readers deployed every 250 meters along both the main tunnels and a secondary tunnel for pipes and cables. As construction work proceeds, LBB will install additional readers, positioned at 250-meter intervals in the tunnels and at key above-ground work areas. As the tunnels reach their full length, the company expects to have deployed a total of some 60 RFID readers.
While the digital network was initially installed to locate staff underground and provide information on tunnel air quality, Sheldon says it has already been expanded because of additional benefits.
In addition to placing readers above ground at emergency assembly areas and other key locations, LBB has placed tags on diggers, loaders and other construction vehicles and mobile plant, allowing accurate tracking of assets.
In addition, the tags’ passive 13.56 RFID inlays are being used to give staff access to the site buildings. The tags’ passive transponders, in fact, were developed specifically to work with the access control technology already in place at those facilities.
NLT’s Macer says the RFID technology was tested extensively in 2007 before being rolled out in January this year. After some early hiccups, it is now tracking staff and vehicles with greater accuracy, ensuring better efficiency and safety.
“The system will be in place for at least another two years until the project is finished,” he says. “However, it may be left in place to allow the company to track staff and vehicles during maintenance of the tunnel.”