Maruhachi Ceramics of America (MCA) is employing a radio frequency identification system to track the locations of 50,000 pallets loaded with products, and has thereby reduced its inventory checking time from three days for eight staff members (a total of approximately 190 hours) to only four hours for a single person. The system—consisting of TracerPlus software provided by Portable Technology Solutions (PTS), passive ultrahigh-frequency (UHF) RFID tags from Alien Technology, and a Zebra Technologies handheld RFID reader and printer-encoder—also ensures that personnel know where a product is located when they need to load it onto a truck. Since the system was taken live in the yard in February 2015, MCA has expanded it to include supplies and tools, to better ensure that components and materials required for manufacturing can be found when needed.
MCA manufactures approximately 18,000 different types of tiles, varying in shape, style and size, typically for roofing. Its customers are worldwide, predominantly in the Sun Belt areas of California, Arizona, New Mexico and Texas, as well as in Hawaii and Guam. An order could include 100,000 tiles, which are made in the California company’s own kiln, and are then loaded onto pallets to await shipping.
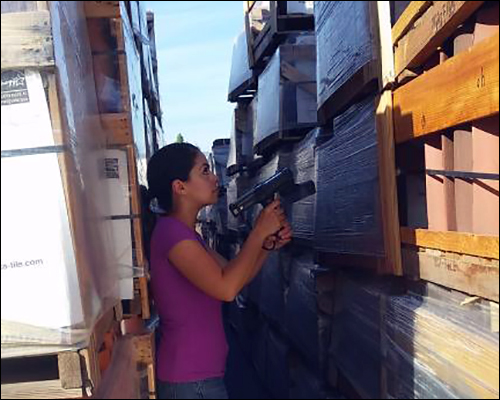
Because it is very expensive to turn the kiln off and on again, the company typically operates the machine around the clock. Once current orders are complete, workers make other commonly ordered products for future orders, all of which are stored in the yard. The tiles, in fact, can be stored there for years without suffering any damage, though the pallets do not last as long as the tiles do when exposed to harsh weather.
Consequently, the eight-acre yard is packed with such a large variety of products that the firm must conduct frequent inventory counts. Historically, it has done so by having employees visually identify each pallet load and record this information manually using paper and pen, or via bar-coded labels attached to pallets. However, says Linda Hanson, MCA’s CFO, since the bar-code system it used was obsolete, replacing scanners or updating software became impossible. The bar-code solution also had shortcomings, since it was slow—staff members had to scan each pallet’s bar-code label, and then input the quantity of tiles on that pallet. Bar-code labels could be difficult to find and, in some cases, were worn off the pallet entirely.
Hanson says she had looked into RFID to resolve the inventory issues, but found that the technology was too expensive. That changed, however, when she discovered the PTS system that enabled the scanning of tags via mobile handheld readers, and the management of the collected data via TracerPlus Mobile Data Collection software operating on the handhelds and on the company’s database. The system was installed in just two months, she reports.
PTS provided its TracerPlus software and developed an app for the handhelds specific to MCA’s data-collection requirements, according to Brad Horn, Portable Technology Solutions’ CEO. TracerPlus also provided the adhesive labels with embedded Alien ALN-9629 Square inlays made with Higgs 3 chips.
First, the tile company had to tag the pallets. It used a Zebra printer to print and encode each RFID label, which was then applied to a pallet. Workers utilized the TracerPlus software running on a Zebra MC9190-Z handheld reader to link the unique ID number encoded on the tag with details about the product to which it was attached, including its product code, quantity and date of manufacture, as well as the row in which it was being stored.
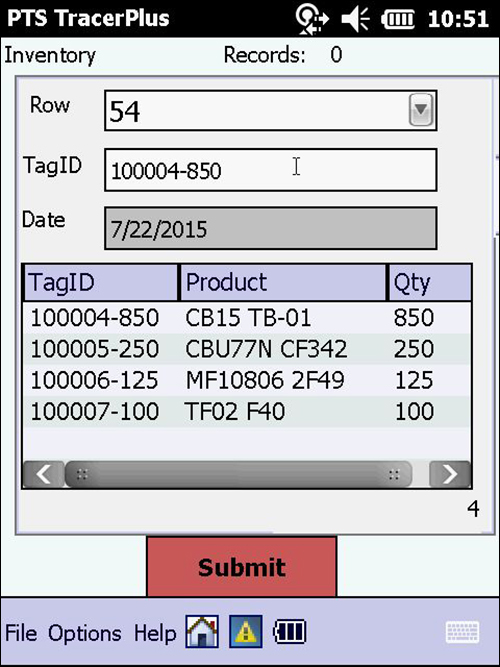
It took several months for the company to tag all of the pallets, Hanson says. Each time a pallet’s load of tiles is broken down to smaller pallets, she adds, an RFID tag must be applied to each new pallet, while data linked to an existing pallet tag must be updated to reflect the changed quantity of product it holds.
The TracerPlus software running on the handhelds and on MCA’s database collects the latest location data, along with any additional information input by personnel during inventory counts. That data can then be imported to the company’s existing yard-management inventory software on its enterprise resource planning (ERP) system.
If yard workers need to locate specific pallets in order to put them onto trucks, they can use the data in the TracerPlus software to identify the row where those pallets are located. They can also determine how much product is loaded on each pallet.
While bar-code-based inventory counts were conducted approximately once a month, Hanson says, the RFID process can be carried out weekly or daily, if the company so desires. A staff member carries the handheld reader into the yard and, at each row, enters the row number. He or she then walks down the row, reading tags along the way. The number of tiles on the pallet doesn’t need to be input since that data is already stored in the RFID system. Typically, the worker waves the device up and down in order to ensure the capture of every tag ID, including those of pallets stacked on top of others.
The reader could interrogate tags without being waved, Hanson notes, but since the device can pick up stray reads from tags located on pallets in other rows, it is a more foolproof process to sweep it up and down. This differentiates the row’s local tags, she explains, which will be read numerous times compared with any tags in neighboring rows.
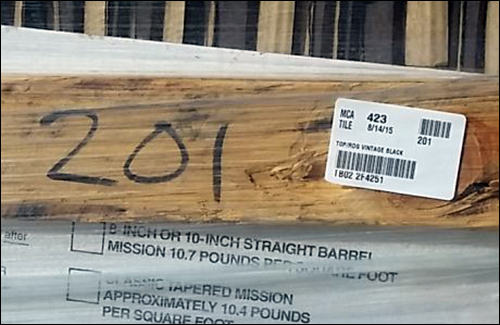
“PTS has developed software tools that work across our [reader and printer] portfolio,” says Carrie Angelico, Zebra’s senior RFID channel business development manager. The industrial-class reader comes with a linear antenna for a long read range, she says, and is designed to be rugged enough for use in locations such as MCA’s storage yard. MCA uses the reader in batch mode, Angelico explains, storing data and uploading it when the device comes within range of a Wi-Fi node or is cradled to a computer.
Early this past summer, MCA expanded the system to include the RFID-tagging of parts and supplies, such as bearings and various modules that go into the kiln, as well as glaze and some other materials. Managing these items in the past was a difficult task, Hanson says, since it required that a staff member move throughout the manufacturing area to conduct counts of various objects, which could take weeks before the task was completed. Now, Hanson says, with RFID tags attached to about 500 items, she can walk the manufacturing area herself, using the handheld reader to perform a complete inventory count.
In the future, Hanson says, her company might look into making the RFID tag reads more automatic. This could be accomplished by installing fixed readers in the yard or manufacturing area, mounting readers on forklifts, or attaching an interrogator to a drone that flies over the yard daily. However, the budget does not yet allow for such upgrades. “We’re taking baby steps now,” she states. “What I like about the TracerPlus technology is that it’s scalable.” Down the line, Hanson adds, her company could use a fixed or other reader option with the same software.