German heating technology manufacturer Vaillant Group is employing radio frequency identification to track work-in-progress as it produces residential boilers at its U.K. plant in Belper, Derbyshire. The system, provided by CoreRFID, has been installed at one of the factory’s four assembly lines, and has proven, in the year since installation, to reduce production errors six-fold, the company reports, thereby increasing the quality and efficiency of the assembly process. The technology will be installed over the coming years on all four of the site’s assembly lines, according to Richard Sainsbury, the plant’s industrial engineering manager.
The Belper plant makes more than 400,000 heating units annually that are sold in the United Kingdom and the Netherlands, with the amount of production per month varying according to seasonal demand. Vaillant Group has made high efficiency and high-production volume a priority at all of its plants, Sainsbury says, including the Belper site. In an effort to achieve greater efficiency, the company sought a system that would instruct staff members about the production steps for each piece of equipment, as well as create a record of work-in-progress and halt the system if mistakes are made.
The production process begins with a boiler chassis on a wheeled cart that passes through 15 separate stages until the boiler is fully assembled, with a single employee building each individual unit. The system monitors workflow to ensure that each step is completed properly, and the boiler continues on to the next step as quickly as possible. Six to 12 carts are in progress on each production line at any given time.
Vaillant Group’s focus is on improving the efficiency of moving carts from one station to the next, by instructing employees as to where the product needs to go as soon as a step is finished. Different boilers typically require different assembly processes, and each assembly-floor worker has to make decisions regarding when a task is complete, and when to take a boiler being built to the next station for further assembly. Mistakes are sometimes made, though they might remain undetected until much later.“The greatest priority was controlling the process,” Sainsbury states. If a mistake were made (for example, if a step in the assembly was skipped), it would be caught only at the end of assembly, when the product was tested. Rectifying that error would require taking the piece of equipment back through the assembly station where the slip-up occurred, and making the necessary corrections—which, he says, was a time-consuming process. “If one element [in the assembly process of a piece of equipment] was missed, and it wasn’t found until the final test, we lost time and efficiency—time that could’ve been used for assembling.”
With the RFID system—which was installed in February 2010—the Vaillant Group has been able to reduce errors by removing the decision-making process from the assembly staff’s responsibilities. Instead, the company utilizes an RFID-enabled automated system to track when each task is completed, and to allow the next station to become operational only if all tasks have been completed at the prior station. Electronic tools that provide feedback to the company’s back-end management system are used in conjunction with RFID readers, so only the correct boiler can activate the subsequent station. In addition, the system can detect mistakes and ensure that no further assembly takes place, by showing a failure in the process to the station’s operator and not allowing progression until all necessary work at that station has been carried out.
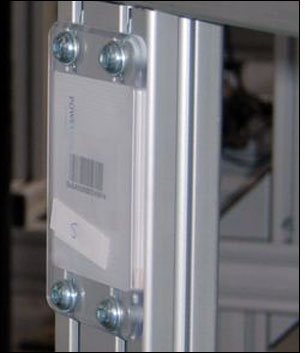
With the RFID system, the company attached a battery-assisted passive ultrahigh-frequency (UHF) EPC Gen 2 tag, provided by Power-ID, on two opposing legs on each of 20 trolleys. Vaillant Group needed the system to read tags quickly and send data to the assembly-management system (AMS), which would then permit the powering of tools only if the trolley ID number indicated the proper chassis had arrived at the station. The battery-assisted tags provided that quick response time from the reader. The company had tested passive, active and battery-assisted systems, Sainsbury explains, and had selected the battery-assisted solution as the most accurate. “We found passive tags did not provide a high read rate in the highly metallic environment,” he says, “while active tags were capturing stray reads from carts passing through other parts of the assembly line.”
All boiler variants can automatically be accommodated through reading the RFID tags and cross-referencing against the components being assembled. When a boiler chassis is placed on a trolley, the ID number encoded to the trolley’s RFID tags is read and forwarded to the AMS database, where the tag ID is linked to the chassis’ serial number. The trolley’s tag is coupled with the chassis’ serial number for the duration of the assembly process. In addition to the serial number, the AMS database also contains other information, such as the assembly worker’s bar-coded ID number, and component items installed on the boiler.Workers follow lines marked on the floor as they transport the carts from one station to the next in a U shape. The AMS software tracks the tasks completed at each workstation by capturing information regarding which electronic tools were used at the stations, and in what order—enabling screw counting, as well as torque and angle measurements governed by tolerance limits. When a task is completed at one station, that data is stored on the AMS system, and the software then instructs the next workstation tools to power on, once the specific RFID tag for that boiler chassis cart is read.
There are two workstations for most of the 15 stages of the production process. A ThingMagic Astra RFID reader was installed at each station, culminating in the deployment of approximately 28 interrogators, some as close as eight feet apart. As soon as the work at one station is completed, the software triggers the next station to look for that tag. A video monitor then instructs the assembly-floor worker to wheel the cart to the next appropriate station. Because the readers seek an RFID tag ID only when triggered to do so by the AMS software, the company is able to reduce the risk of false reads (reads of tags in the neighboring area), since not all readers are active simultaneously.
What’s more, the system stores information regarding the time at which each piece arrived at each station, thereby providing the engineering team with greater details as to where bottlenecks occur, as well as where any boiler (and corresponding operator) is in the assembly process at any given time.
Now that the RFID system has been installed at the Belper facility, the company plans to introduce a similar system at its other sites across Europe. “We have become a showcase for the group, and it will become group standard across all products when new versions are launched,” Sainsbury states, noting that the Belper plant intends to expand the RFID system to all of its lines over the course of four to five years. “We will have a second implementation [on a new production line] in the second half of this year, then roughly every 18 months until they are all completed.”