For the past year, Wellco, a Tennessee manufacturer of combat boots, has been ensuring the accuracy of its shipments, as well as complying with a U.S. Department of Defense (DOD) mandate, by applying radio frequency identification labels to every pair of boots that it ships to the U.S. Air Force. The company is reading the labels attached to those boots, as well as to the cases and pallets in which they are packed, in order to confirm that the shipments are correct.
Wellco has been a supplier of combat footwear since 1965. The present generation of combat boots come with a rubber-based sole and a rugged high-traction rubber tread. The company recently opened a new facility in Morristown, Tenn., where its boots are packaged prior to being shipped to military agencies.
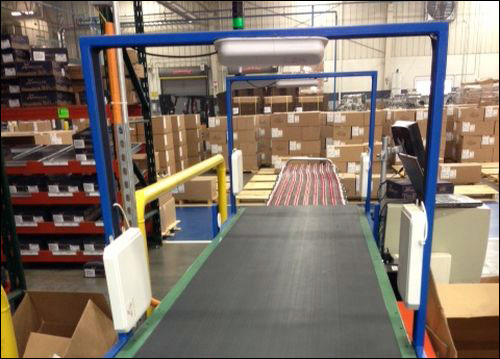
To track those boots, Wellco is employing a software and RFID hardware package supplied by defense commerce solutions company Odyssey. As part of that package, Odyssey is providing Avery Dennison ultrahigh-frequency (UHF) RFID tags, Zebra Technologies R110Xi printers and a Printronix SL4M printer to encode the tags. Odyssey’s cloud-based hosted RFID software, known as Visual Shipment Builder, then stores data regarding each order, and about every pair of boots being packed in that order that is linked to a tag number. The information can be accessed by the supplier, and can be submitted electronically to the DOD’s Wide Area Workflow (WAWF) system. The RFID-based system also includes Alien Technology readers to interrogate tags attached to cases loaded with goods filling a specific order, according to David Mason, a senior network administrator at Tactical Holdings Operations, Wellco’s parent company.
Odyssey has been providing software solutions for the DOD’s textile and clothing suppliers since 2006, says James Lusk, the company’s director of sales and marketing. “RFID is at the core of what we do,” he states. Without the Odyssey software and RFID data, Lusk explains, suppliers received orders and filled them manually, electronically entering data that they could then send to the DOD as an advance shipping notice.
The DOD contacted Wellco in early 2012 with a request to modify its existing contract for boots sold to the Air Force, by applying RFID labels to every pair of boots in the form of a hangtag, as well as affixing an RFID label to each case in which the boots are packed, and the pallets on which they are shipped. According to Mason, the company was able to implement the Odyssey solution within three months of receiving that request. The system now tracks approximately 1,200 pairs of boots shipped to the Air Force on a monthly basis.
With the RFID technology in place, Wellco’s workers first log onto the Odyssey server with a password, and pull up any new contract. Based on that data, they then begin building an order.
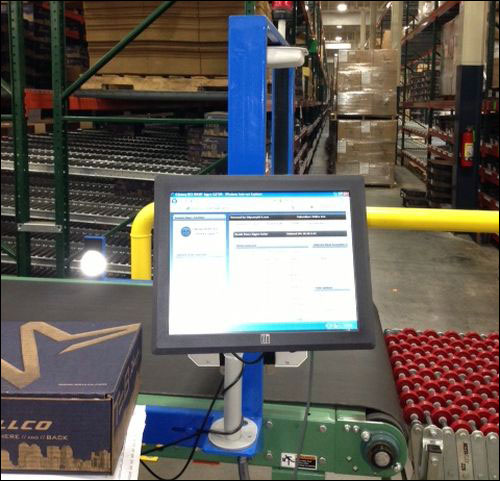
While the boots are assembled mostly offsite, the products undergo final manufacturing processes onsite, and are then shipped out to the Air Force. At four workstations, operators apply laces, visually confirm the size and style to match the order, and press the prompt in the Odyssey software to print and encode the labels on the Printronix printer. The workers then take those labels and attach one to each pair of boots, on its laces, after which the pairs are placed in individual boxes, with six such boxed pairs loaded into a case.
The case passes down a conveyor, where a laser sensor identifies its arrival and awakens an Alien reader. The reader then captures the tag ID numbers of all six pairs of boots and forwards those IDs to the software, which confirms that the footwear is appropriate for that order. In the event of an error, an alert is displayed on a screen mounted at the end of the conveyor.
The case passes a second Alien reader for the sake of redundancy. If the ID numbers are a match for that order, the system prompts a Zebra printer to print an adhesive label for that carton. The software then stores that carton label ID number and marries it to the ID of each pair of boots packed within.
Staff members load the cartons onto a pallet, with a total of approximately 16 cases per pallet, and another Zebra printer prints and encodes an RFID label that is then attached to the pallet. At that point, Wellco’s employees scan the bar code printed on the pallet’s label, and the system can then update the boots’ status as being loaded onto a pallet and prepared for shipping.
The conveyor can also be used for auditing, Mason says. For example, if Wellco’s workers want to know what is inside a sealed carton that has been separated from an order, they can simply pass it through the conveyor. In the future, he adds, the company may acquire a handheld RFID reader to enable this function as well.
The solution not only enables Wellco to comply with the DOD’s RFID requirements, Lusk says, but also reduces the incidence of errors and increases efficiency. Mason confirms that the technology has reduced the number of errors, which can be expensive. For example, he says, in some instances, Wellco must recheck shipments and relabel them if mistakes are discovered, either before or after the shipment leaves the facility. With the use of RFID, he reports, the need for this practice will become less common.
In addition, suppliers can utilize Odyssey’s service bureau to create the RFID tag serial numbers that are encoded on the shipping labels, or on each item, by making selections from a pull-down list in the software. The system then directs the encoder at the Odyssey service center to begin printing and encoding the labels, after which Odyssey express-ships them to the customer.