Rittal, a manufacturer of enclosures for servers and other IT equipment, as well as climate-control and power-distribution systems, is employing radio frequency identification technology to manage the movements of its products through the painting process at its Rittershausen assembly plant. By using RFID, the company knows where each product is in the painting process, as well as how much paint has been used and when it will require replenishment. The company can thus ensure that it has up-to-date information about products that will be available for shipping, address any delays in the painting process and reorder more paint in a timely manner. The technology, provided by German integration firm IdentPro, includes Xerafy on-metal tags.
The painting takes place in what the company refers to as an environmentally friendly paint shop within its 485,000-square-foot factory. The factory features a 10-kilometer-long (6.2-mile-long) conveyor that moves products through the painting process, which involves pre-treating each item, followed by dip-priming and powder-coating.
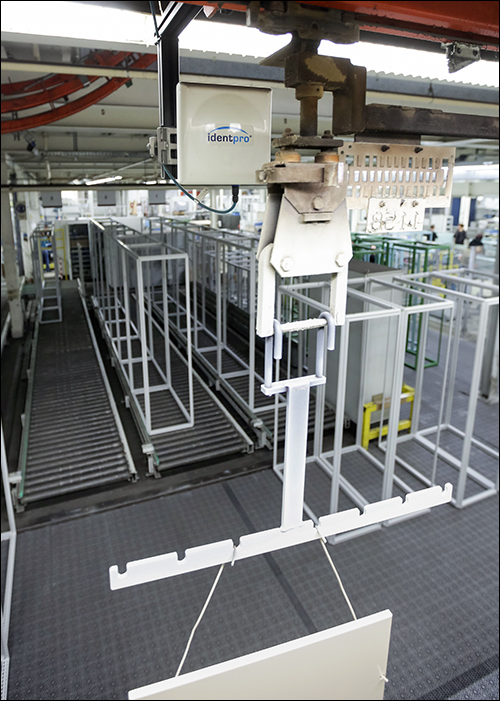
Prior to installing the RFID system, Rittal did not track specific units as they proceeded through the painting process. Because of the volume of goods moving through the conveyor system, as well as the length of the conveyor itself, Rittal had found it difficult to know which products were being painted at any given time, how soon they would be finished and how much paint had been used. Since the company did not track individual items, says Michael Wack, IdentPro’s founder and managing partner, “raw material purchase orders were based on historical data rather than actual need. Also, actual stock was known rather vaguely.”
Rittal first began working with IdentPro on an automated solution in October 2012, and conducted a proof-of-concept in February 2013. The permanent deployment began in August of that year and became operational in June 2014.
There were several challenges to consider as the companies developed the solution, Wack says. For instance, the tags would be attached to hangers on which the products are suspended from the conveyor, and those hangers are exposed to high temperatures and harsh chemicals due to the cleaning processes involved. The tags would also need to work in the presence of metal, and there were software challenges as well. Rittal wanted to receive the RFID-based location data to be managed on its existing SAP system, so integration between IdentPro software and the SAP system was necessary.
Additionally, Wack says, IdentPro would need to install the technology while production at the plant continued running normally, in order to prevent production downtime.
For the pilot, the company used a single reader and 100 hangers, each equipped with a Xerafy MicroX II RFID tag. Data was collected by IdentPro software and assessed to determine whether the reader and tags could operate in the plant’s demanding environment. The results were favorable, Wack says.
The permanent RFID system was deployed with 22 IdentPro identMX readers with integrated antennas, which were installed overhead to read the unique ID number on each tag attached to a hanger. That data is interpreted by IdentPro’s RFID Control Unit middleware, and is then forwarded to Rittal’s SAP system so that it can determine each item’s production stage.
All readers are connected via Ethernet, and the RFID Control Unit middleware that receives the read data is located on IdentPro’s RFID Enterprise server. The RFID server comprises a Web-based front end for managing and monitoring the RFID readers, Wack explains, including alerting functions, implementing the business logic, and providing information to workers and the interface to Rittal’s SAP system.
The products are suspended on hangers as they pass down the conveyor. Each hanger’s MicroX II tag has a unique Electronic Product Code (EPC) number encoded to it, and that ID is read and married to the production number each time a new product is attached to the hanger, thereby linking that tag with that particular product. The tags are designed for on-metal applications, to be heat-resistant up to 250 degrees Celsius (482 degrees Fahrenheit) and to be rugged enough to withstand the abuse they can experience during the painting process. The same tag can be reused for another product on the same hanger.
“The MicroX II paint-shop RFID tag is specially designed for paint-shop manufacturing applications and has been widely deployed in the field for such applications with many automotive companies,” says Dennis Khoo, Xerafy’s CEO and founder. “For this Rittal deployment… a general high-temperature-resistant tag may not be enough to do the job. The RFID tag must be durable enough to endure many cycles of extreme temperatures, as well as withstand repeated exposures to caustic fluids.”
With the full deployment, a MicroX II tag is screwed onto each of the factory’s 1,600 hangers, thereby ensuring that it cannot be knocked loose. When a worker attaches a product to a hanger, he or she scans the bar-coded ID number on the paper production order and reads that hanger’s RFID tag. The hanger’s EPC number is consequently linked to the bar-coded ID and forwarded back to the SAP software. As the product travels down the conveyor system, its hanger passes the readers, which capture the tag’s EPC number. Based on that ID and the specific reader that captured it, the IdentPro software identifies the product and its location, and then forwards that data to the SAP system.
The SAP software uses the collected RFID data in multiple ways. Rittal knows not only that a production order is being filled, but also approximately when it will be finished and then ready for shipment. This information ensures that any delays are prevented, and can be shared with customers if they seek an update regarding their orders.
In addition, by knowing how many products have passed through each phase of painting, Rittal’s software can track how much paint has been used and when more must be ordered. Purchase orders for additional paint are thus automatically created, ensuring that the shop never runs out of any material during production.
Installed around the paint shop are Web-based monitors that display the IdentPro software, allowing workers to view which production orders are coming next, based on the RFID tags scanned. “Via monitors, workers are informed about actual and next production orders,” Wack explains, which enables them to prepare the area for that work.
If the IdentPro software detects a delay in the paint process or the unexpected removal of a product from a hanger, the SAP system can issue an alert to the plant’s managers.
“RFID proved to be the perfect solution for tracking work-in-process,” Wack states. “Using a reader with integrated antenna and PoE [power-over-Ethernet] kept installation cost and effort to a minimum. Also, the system is maintenance-free, thus reducing the TCO [total cost of ownership].”
Rittal did not respond to a request for comment about the technology.