Healthcare and pharmaceutical distribution company AmerisourceBergen has released an app-based version of its Medication Tray Solution to help hospitals more easily manage their pharmaceutical products wherever they may be within a facility. The updated version of the solution, with the app, coincides with the company’s adoption of RAIN Alliance standards to ensure that each UHF RFID tag has a unique, standards-based ID beginning with a company identification number (CIN).
The Alliance recently introduced the new ISO numbering system to simplify the encoding of RFID tags and reduce what it calls tag clutter, the stray reads from various tags used by different companies for a variety of purposes. Adoption of the RAIN standard, AmerisourceBergen explains, enables greater consistency and ease of use for its customers in the healthcare market.
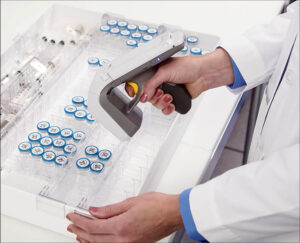
AmerisourceBergen’s medication tray solution
The app enables users to capture and manage data regarding their products via a handheld Bluetooth-based device. In that way, those employing the company’s AB Medication Tray Solution can manage information about drugs on crash carts anywhere within a hospital, as well as view expiration dates, locate recalled products and ensure that each carton tray is properly stocked. The solution includes passive UHF RFID tags applied to each product AmerisourceBergen sends to its customers.
AmerisourceBergen provides a touchscreen kiosk connected to a handheld RFID reader, and now additionally a mobile app. The wholesale drug distribution company has a long history with RFID and other automatic identification technologies. “About 15 years ago, we started looking at technologies for auto ID,” says Dustin Roller, the firm’s VP of innovation product development, with the goal of capturing data automatically to understand inventory utilization at customer sites.
The company provided its RFID tags for use on high-cost medications, and the technology has since been adopted to track drugs and devices at hospitals physicians’ offices, veterinary clinics, clinical trials, warehousing, logistics and surgical theaters, “all circled around the need for serialized and highly precise inventory management using automation technology,” Roller says. In that way, he adds, the company aims to take manual or barcode tracking out of the hands of customers, enabling medical facilities to prevent errors and achieve accuracy that could not be accomplished without the technology.
These days, the company has a variety of RFID solutions in use by hundreds of its customers. One of the most common solutions is being employed by physicians’ offices for the management of medications stored within smart refrigerators or cabinets. The system includes a touchscreen, a lock and built-in RFID inventory-management capability to ensure only authorized personnel can remove a product, as well as track what that item is and for which patient it is being used.
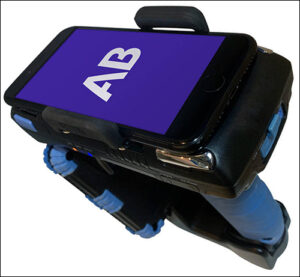
The company’s new mobile application
The smart tray medication system, first piloted in August 2020, was commercially released this past May, Roller says. “There’s a very manual process in hospital pharmacies associated with refurbishing or reviewing and auditing OR kits and trays on crash carts,” he explains. Trays containing 20 to 70 units of such products as vials and syringes are used during patient care, after which those trays are placed onto a cart and sent back to the pharmacy for inspection. This process helps pharmacy employees identify what has been used, while detecting any approaching expiration dates or recalls.
Without RFID, this task must be performed visually, which requires individuals to remove each item and look at every label closely. The items are also compared against a fill list to identify if anything is missing from any given tray. That manual process typically takes 30 minutes per tray to complete, and it introduces the opportunity for human error. With the RFID system in place, each vial or syringe has a tag encoded with a unique ID number that is linked to data including the lot and serial numbers, as well as the expiration date.
A healthcare company would purchase AmerisourceBergen’s software, kiosk and handheld reader, then begin receiving RFID-tagged products from AmerisourceBergen. As goods are received, they can be placed in trays. The handheld device, tethered to the kiosk via a Bluetooth connection, can then read each tag ID and identify which items have been received.
When a tray is being prepared for patient use, it typically is loaded with the items needed, after which the handheld reader interrogates all tag IDs. The user views the software on the kiosk to confirm that no products have expired and that all are correctly packed, and those trays are then placed on a crash cart and transported to the appropriate area of the hospital. If a drug is found to be expiring or has been recalled, workers could identify that product as the trays are read and the system will prevent the release of that tray for patient use.
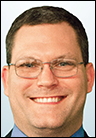
Dustin Roller
With the release of the mobile app, employees can use a handheld reader with a Bluetooth-connected mobile device attached to capture data about each vial or syringe, from anywhere within a hospital. For instance, users could input the items they seek and use the app in Geiger-counter mode to be alerted if they come within range of those products. The handheld device could read all tagged items on a tray or cart to capture data regarding what is loaded there. They could also choose a setting that would simply detect items that have reached their expiration dates.
AmerisourceBergen provides RFID readers it has developed, which are manufactured by a third party. A variety of readers could be used, Roller says, adding, “Depending on the workflow and use case, we change out that hardware.” Several of the company’s customers are now testing the mobile app. The firm is using the RAIN Alliance’s standardized IDs, including company identification numbers. The organization was appointed an issuing agency code by ISO, according to Steve Halliday, the Alliance’s president, enabling it to issue the CINs.
As a result, AmerisourceBergen has a CIN that precedes the rest of the unique number on each tag. That makes it simpler for readers to be set to identify only the relevant tags that might be mingling with other tagged items. “Today, more and more RAIN tags are being applied to more and more products,” Halliday states. That can include tags in clothing or on other equipment, or components built into equipment, commonly used in hospitals or elsewhere. “So what we want do is make it easy for people to find their tags among all the tags that are being interrogated, and then filter out the tags that aren’t relevant.”
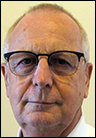
Steve Halliday
By employing the standard, the AmerisourceBergen solution will only interrogate relevant tags, while others who might also be using the new standard could screen out AmerisourceBergen’s tags if they are not part of the tracking solution. The company says it is among the standard’s early adopters, with other businesses expected to follow suit. “We hope to see many more companies taking advantage of this,” Roller states. Halliday adds, “They were one of the first, but we have inquiries from both small and big companies” to adopt the standard as well.
The benefits extend beyond healthcare, Halliday notes. A postal service at which boxes are tagged could employ the standard to ensure only its own boxes are read in a crowded RFID environment. A carrier might have tags in clothing, as well as potentially dozens of tags in a vehicle that were applied during manufacturing. “The postal service company needs to be able to distinguish the tags quickly,” he says. Additionally, since each ID is unique and never duplicated, “They can be assured that other people are not encoding the same numbers on their tags. We need an effective standardization method to be able to deliver this kind of capability to our customer marketplace.”
There are other UHF RFID standards, including GS1‘s EPC standards and IATA‘s standards for tracking airline baggage. The CIN is likely to be used in applications in which closed-loop systems are in place or for systems not using another standardized system. While there may be specific applications for the CIN, when GS1 EPC standards are used in RAIN RFID tags, they provide for open, global supply chain implementations and can be used for company-internal numbering applications as well, according to Robert Beideman, GS1’s chief product officer.
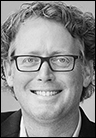
Robert Beideman
GS1 standards offer a globally unique identity in an established language of data exchange across data carriers, ranging from barcodes to UHF RFID tags. The RAIN Alliance’s goal is to work with GS1, Halliday says, “and to recommend that people use the GS1 system where it is applicable to their application. If GS1 does not work for the application and there is no other standardized system that will do the job, then the RAIN system gives the user the chance to operate in a standardized system.”
The key is interoperability, whether GS1 standards or the CIN are used. “Interoperability between global trading partners means more visible supply chains, improved product provenance and information transparency, Beideman explains, along with the ability for companies to future-proof their RFID investments in case they expand deployments beyond their own four walls or across multiple use cases.
“There is a vast amount of data being shared today,” Beideman states, “and it simply happens more efficiently within a standards-based framework that also allows for the encoding of more granular levels of identification into RAIN RFID tags—even the ability to link products to other trusted sources of data. The GS1 system is flexible and can grow as a company grows.”
For AmerisourceBergen, Roller says, “There [are] tremendous efficiency gains that are achieved by using this technology, but we can also improve safety by ensuring that none of the [medication] products have expired and are circulating out there, where they might potentially be administered to a patient.”