An international maker of plywood and particleboard, Switzerland’s Krono Holding, is employing an RFID-based navigation system at its warehouses in Hungary and Slovakia, with a third system slated to become operational at a German warehouse in July. More than 1,600 passive low-frequency (LF) tags, embedded in the floors of each warehouse, track the movements of forklift trucks and the materials they load and unload.
The system was installed in a new warehouse at each of the three locations, but the company plans to expand it to existing facilities at a still-undetermined time. The system is based on technology from two Bavarian companies: SEP Logistik, a Weyarn-based provider of commissioning and warehouse management software, and Indyon, a supplier of real-time tracking systems headquartered in Pöcking, near Starnberg.
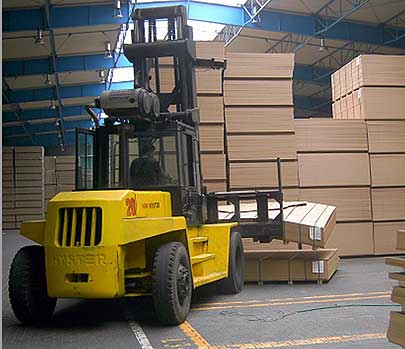
The first warehouse to utilize the system was the Kronospan-Mofa Hungary Farostlemezgyártó factory. Managers wanted to create a more efficient system for locating particular pieces of plywood and particleboard, as well as for conducting quality tests on batches and ensuring that the oldest goods are sold first. The factory had been tracking such tasks by hand, relying on lists and employees’ memories. Kronospan-Mofa Hungary stacks about 200 types of plywood and particleboard on blocks of pallets that can measure 5 meters high and 15 to 20 meters long.
When Kronospan-Mofa Hungary began planning the new warehouse, it contacted SEP Logistik, and the two firms developed a concept together. SEP Logistik proposed its RELAG software application, which features an RFID-based navigation system.
Kronospan-Mofa Hungary has been using the system since August 2007, when construction of the new warehouse was completed. It installed the 134 kHz tags in glass capsules in the concrete floor. The tags, made by Texas Instruments, comply with the ISO 11784 standard. Each tag is encoded with a unique serial number, which is stored in a database, where it is associated with the tag’s warehouse location.
As soon as they are produced in the adjacent factory, the boards are stacked on a pallet. The front of the pallet is affixed with a label encoded with a bar-coded ID number and a product description. A driver picks up the pallet, using one of five forklifts outfitted with bar-code scanners and RFID interrogators. The forklift’s bar-code scanner reads the pallet’s label and notifies the warehouse management system that it has been picked up.
The system then sends a message to the forklift’s touch-screen monitor, instructing the driver to place the pallet in a particular stack. The forklift driver heads toward the stack in the warehouse—which encompasses more than 7,500 square meters of space—driving over some of the RFID tags embedded in the floor. The forklift’s RFID reader interrogates the tags, and the computer system is updated immediately with the vehicle’s location.
The location information is used to confirm that the right batch of goods is placed on the correct storage stack. If a driver were to head in the wrong direction, the system would use this data to alert the driver to the impending error, thus saving time. Upon reaching the appropriate storage stack, the driver places the pallet on the stack and confirms delivery via the vehicle’s touch screen. By reading the RFID tag in the floor in front of the stack, the system double-checks that the pallet has been delivered to the proper storage stack.
When it’s time to load trucks, the same process occurs in reverse. The forklift driver picks up the pallet from a particular stack, as instructed by the vehicle’s monitor, and takes it to the specified truck. Instead of having to read a paper list while at the wheel of the forklift, the driver relies on the electronic cues generated via RFID to indicate where to drop off the load. Once the pallets have been loaded onto the back of the truck, the warehouse management system records the exact time of loading and automatically produces a shipping receipt without the worker having to request it.
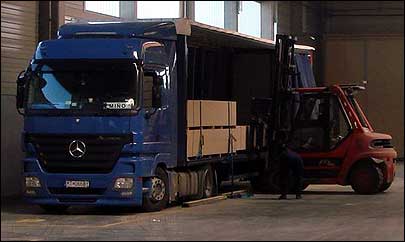
Dietmar Rinne, head of Krono Holding subsidiary Kronospan IT GmbH, says there were no technical problems during the system’s installation, and that there have been no problems operating it. However, the company did need to invest significant time and resources in training employees in the system’s use—it took about eight weeks to train 25 workers, he says.
Rinne oversaw the integration of the RFID application with the company’s custom ERP software. He says Kronospan Hungary invested €200,000 ($312,000) in the system, but has not yet calculated an ROI since his firm lacks specific data for comparative purposes on the costs of doing the process manually.
According to Rinne, Kronospan is satisfied with the system and its main benefit—that it allows workers to find stored products faster than in the past. Based on this improvement, he notes, Kronospan is now able to conduct more quality checks since each check—which involves locating specific items—can be performed quicker. What’s more, since it can find specific items without using paper lists and relying on the memory of its employees, Kronospan is able to ensure that it ships the oldest goods first, so that its stock doesn’t age.
Krono has already rolled out the same system at its warehouse in Zvolen, Slovakia, featuring more than 4,000 tags embedded in the floor and eight RFID-enabled forklifts. The training process in Slovakia was faster and smoother, Rinne says, thanks to the company’s experience in Hungary. A third identical system is currently being installed in Bischweier, Germany.