RFID tag maker Omni-ID has released a new line of high-temperature passive EPC Gen 2 ultrahigh-frequency (UHF) RFID tags for use in environments that reach 225 degrees Celsius (437 degrees Fahrenheit). The tags are intended to enable manufacturers, oil producers, hospitals and other companies to employ RFID in traditionally unfriendly environments in which extreme heat is used. The high-temperature tag family consists of the new Fit 100, as well as Fit 210 and Fit 400—high-temperature versions of the company’s existing Fit 200 and 400P models. Thousands of the heat-tolerant tags are currently being deployed in manufacturing and health-care settings, says Tracy Gay, Omni-ID’s marketing VP.
Each of the three tags is designed to be small, with a read range that reflects its name. With a fixed reader, the Fit 100 has a read distance of 1 meter (3.3 feet), the 210 has a range of slightly more than 2 meters (6.6 feet), and the 400 supports a read distance of 4 meters (13 feet). The tags are somewhat more expensive than the non-high temperature versions, according to Gay, though the specific cost will vary according to the volume of tags ordered.
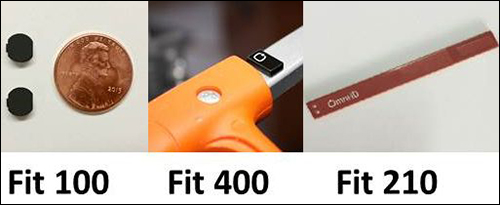
The new tags, Gay says, were developed throughout the past few months in response to requests from customers, who were finding the existing RFID tags to be ineffective once exposed to heat. Most other RFID tags on the market can be ruined in an autoclave oven, or during a vulcanization process or high-temperature washing and sterilization. This has made RFID technology an unrealistic option in some manufacturing, oil and gas, and health-care applications, Gay notes. While there are some high-temperature RFID tags currently offered by Omni-ID’s competitors, she adds, those tags tend to be too large and cumbersome for end users that need, for instance, to fit a tag inside a drilling tool, or to attach it to a pair of forceps used during surgical procedures.
Omni-ID offered custom-made high-temperature versions of its small Fit tags in the past, Gay says, when requested to do so by customers. This year, she adds, the company’s engineers began testing versions that could be released commercially at a reasonably low cost.
The Fit 100, which is smaller than Omni-ID’s previously released Fit tags, is designed for such uses as tracking small surgical tools. Measuring 6.8 millimeters by 6.4 millimeters by 2.1 millimeters (0.27 inch by 0.25 inch by 0.08 inch) and weighing 0.8 gram (0.29 ounce), the Fit 100 could best be used on surgical tools and other very small objects. The Fit 210, measuring 57.1 millimeters by 5.95 millimeters by 1.3 millimeters (2.25 inches by 0.23 inch by 0.05 inch) and weighing 1.0 gram (0.04 ounce), is designed for tracking hand tools, paint processes in the automotive industry, and equipment used in surgical and other health-care applications.
The Fit 400, measuring 13.1 millimeters by 7.1 millimeters by 3.1 millimeters (0.52 inch by 0.28 inch by 0.12 inch) and weighing 1.6 grams (0.06 ounce), works best in metal hand tools, metal IT assets (for such use cases as covert tracking) and applications in which the tag must be embedded in metal compounds. All three high-temperature tags come with an Alien Technology Higgs3 chip and 512 bits of user memory. In addition, all three have an IP68 rating and are recommended for use on metal.
“We’ve tested these for hundreds of hours to validate their stability—thermal cycling, exposure, thermal shock, etc.,” Gay says. The ceramic tags come with heat-resistant insulation for the RFID chip built inside; however, she declines to describe how the tags were developed or what materials were used to provide that insulation.
Several companies in the United States and Europe are already testing the tags. One example is an oil and gas firm that is attaching the tags to drill pipes in order to track their locations and usage, and thus when each requires maintenance, inspection or replacement to meet regulatory requirements.
An industrial tire manufacturer, Gay says, is applying the Fit tags to its new tires so that they can be monitored throughout the manufacturing process, to ensure efficiency and accuracy. After being tagged, each tire undergoes high-temperature vulcanization to bond the tag to its surface. The tags can then be read at workstations as the tires are manufactured and sent to customers. In the future, she says, the company also hopes to track the tags further through the supply chain for such purposes as verifying warrantees.
According to Gay, a health-care company is preparing to use the high-temperature Fit tags to track surgical implants when they arrive at that facility, as they are sterilized and when they are removed from the devices immediately prior to implantation into patients.
All companies using or preparing to use the tags have asked to remain unnamed, she reports.
The new tags’ pricing, Gay says, is intended to be affordable since most end users will require a large quantity. “There is a small premium for [our] high-temperature tags,” she states, “but it’s nothing that would make their use cost-prohibitive.”
While the tags are designed to withstand temperatures of up to 225 Celsius, Gay says, the amount of time that they can tolerate temperatures at 225 degrees will vary according to use case. “These tags were designed for specific cyclic applications, not prolonged exposure,” she notes. Such cyclical heat exposure, in which a tag might be repeatedly subjected to conditions that alternate between ambient or below-zero temperatures and extreme heat, is common, for instance, in industrial paint booths used for curing the paint on products being manufactured, as well as in the food industry, in which high-temperature cooking takes place. “Exposure is different in each one of the key applications,” Gay says.
The tags’ maximum operating temperature is 85 degree Celsius (185 degrees Fahrenheit). Therefore, after a high-temperature exposure, they would need to cool before they could respond to read and write commands from an RFID reader.
Most of the initial customers are new to Omni-ID, Gay says, because they were unable to use RFID technology at all until the new FIT tags were released—either because the existing high-temperature tags didn’t fit properly on their products, tools or assets; were too expensive; or had unreliable read rates.
Whether the adhesive that attaches a tag to an item can sustain such heat is another concern that end users have had to consider, Gay says. Omni-ID recommends adhesives to its customers based on their individual use case. Typically, she says, the company suggests using a permanent liquid adhesive. The tag comes with a temporary adhesive to hold it in place until the permanent one is applied.
Omni-ID has traditionally provided its rugged tags for the manufacturing and oil and gas industries, Gay says. The company has developed partnerships with several companies, such as systems integrators that sell and install solutions for health care, food preparation and other industries.