The Italian arm of Swiss food company Nestlé is expanding a pilot employing active, battery-powered ultrahigh-frequency (UHF) RFID tags to track ice cream as it moves from production factories to distribution centers and on to retail stores.
At the beginning of 2007, Piergiorgio Marasi, a supply chain ice cream and frozen food project and quality manager at Nestlé Italy, asked Swiss integrator IP01 to design a system that would help the company achieve better control of its distribution process. Nestlé sought to ensure ice cream stayed frozen at prescribed temperatures as it changed hands among a variety of internal and external partners before being delivered to shops.
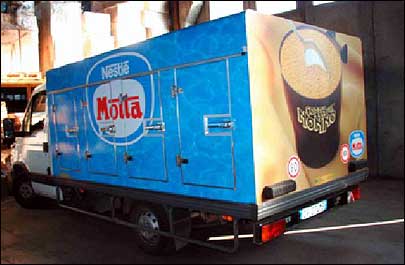
Marasi visited a Manor grocery store in Switzerland, which employs a system implemented and managed by IP01 (At Manor, RFID Keeps Food From Spoiling). The system features stationary interrogators that receive temperature measurements transmitted by active RFID sensor tags installed in the store’s freezers and refrigerators.
Marasi, however, wanted a system with mobile readers that could be mounted on delivery trucks or worn by delivery personnel so there would be no additional manual steps for workers.Therefore, he launched a feasibility study with the RFID Solution Center in Milan, and worked closely with IP01 engineers to design a custom solution.
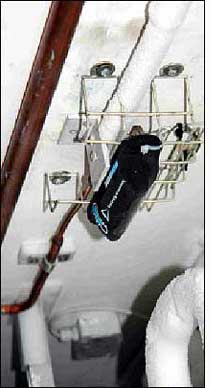
Nestlé Italy has a massive cold-chain network that includes dozens of production plants (some company-owned, others run by co-manufacturers); hundreds of trucks that move goods between the production plants and Nestlé’s three primary cold warehouses, as well as between primary cold warehouses to retailers’ cold warehouses; dozens of secondary distributors; and hundreds of small delivery trucks that transport ice cream to retail shops utilizing more than 100,000 Nestlé-owned freezers.
In April 2007, Nestlé and IP01 chose a representative number of sites to participate in the pilot. The partners placed temperature-sensing RFID tags in two cold storage areas and one at the dock door of a production plant, as well as on five delivery trucks, in two cold storage areas at a single primary distribution center, in two cold storage areas at a secondary distributor, in two ice cream delivery trucks and at 50 shops. Two interrogators were placed at a loading area in the production plant, and another was mounted in the distribution center’s delivery area. If sites were large and tags were out of the reader’s range, IP01 installed a repeater that expands signal range so that only one reader was necessary.
When a large truck carrying a sensor approached the production plant, the reader picked up the signal from the active tag inside cold storage at the production plant. The tag can transmit data up to 200 meters away indoors, and farther outside. The interrogator at the distribution center collected time and temperature readings—taken as goods were moved between sites—from the tag mounted within the truck. Each sensor tag carries a unique ID number (associated—in a database—with the freezer, dock, storage area or truck to which the tag is attached) and logs the temperature data and time the temperature was taken. No further information is recorded.
The final reading occurred when small trucks, also equipped with readers, approached shops and collected data from tags mounted within the shops’ freezers. When the truck returned to the depot, all data saved on the truck’s reader was collected by another interrogator, which then transferred that data to a database. “That’s the big innovation,” Marasi says regarding the automatic collection and transfer of field data to the database.
The RFID sensor tags transmit at a frequency of 868 MHz, using a custom air-interface protocol that minimizes the tags’ battery use to allow for three or more years of battery life. The tags can function at temperatures as low as -35 degrees Celsius (-31 degrees Fahrenheit).
Nestlé Italy has invested about €40,000 ($63,400) in the pilot, and says the system provides a wide variety of benefits. For one thing, quality control experts in R&D can use time-temperature readings to support their research. “The RFID system, in essence, provides these experts with a laboratory in the field,” Marasi says, “to determine the effect of temperature changes on the product.”
Another main benefit, according to Marasi, is precise, real-time information about the conditions under which goods are stored and transported: “We have the infrastructure under control, without any additional activity from people.”
In addition, the use of RFID time-temperature sensors can be a way to reinforce the high value and quality of the brand to consumers. What’s more, Nestlé can reduce the cost of maintaining its large number of freezers through timely repairs and punctual maintenance, based on the freezers’ temperature readings. It can also track freezers more easily—and because spoilage will be reduced, the company could possibly save money by potentially lowering the cost of insurance that partners carry to cover themselves if goods are damaged during delivery.
“Nestle pays the costs of insurance indirectly through the higher prices the distributor has to charge,” Marasi says. Distributors, he notes, are very happy because of the improved relationship with customers, as well as the automatic quality control.
Finally, Marasi sees big potential savings in energy costs and benefits to the environment. The exact temperature readings of shop freezers taken during the pilot revealed that some freezers were set too cold and were, thus, wasting energy and causing ice cream to be served too hard to customers.
“It’s a raw calculation,” Marasi states, “but we estimate that the cost for freezer energy across Italy is several million euros. If we just save 5 to 10 percent, this is a big savings and a boost to the environment.” This helps promote sustainability—which he says is a Nestlé priority.
This year, Nestlé Italy intends to expand the pilot to cover all production plants and the three primary distribution centers directly managed by Nestlé, as well as 150 primary large trucks and 150 freezers. “The company wants to give our partners the message that we care about the ice cream,” Marasi says, “from production up to their delivery point.” Nestlé is also considering an RFID sensor tag that could measure the electrical power consumed, so that it can better control energy use.
According to Marasi, Nestlé Italy is pleased with the system, though it wants to see improved software stability and better tag read rates, which he says presently average between 80 and 90 percent.
The system offers a number of other potential benefits as well, including substantial savings by reducing manual tracking tasks. The system could also be used to analyze data that can be the basis for business decisions. For instance, the company could make quicker decisions on quality management using real-time data, and it could also certify the cold chain and use that certification as a basis for advertising.