NASA has a weight problem. It costs $10,000 to lift a pound of payload—flight crew, scientific instruments and other cargo—into orbit. Every gallon of water carried to the International Space Station costs roughly $80,000. It’s estimated an astronaut consumes $28 million worth of water during a yearlong stint on the station.
Shipping all that water into space would be inefficient, so since 2008, station astronauts have been drinking water reclaimed from urine, via the Urine Processor Assembly (UPA). The Distillation Assembly (DA), a keg-size unit at the heart of the UPA, distills water from urine, which passes into the device from the station’s toilets. The rotating, electrically heated DA separates the water from the chemically treated waste; the water is then treated in another piece of equipment, the Water Processor Assembly. Astronauts report the water tastes no different from any other distilled water.
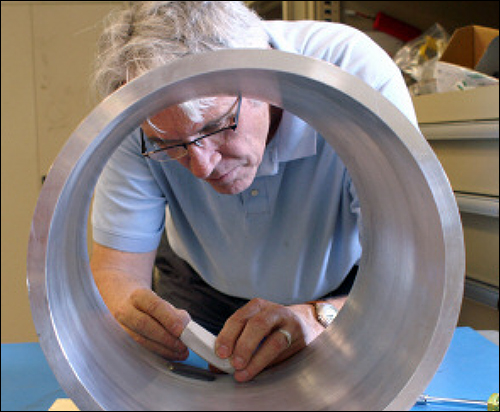
The UPA reclaims roughly 75 percent of the water from astronauts’ urine, saving NASA and its international partners millions of dollars annually. That figure is expected to go up to 85 percent this year. But it still costs NASA more than $40,000 to ship a 2-liter bottle of water to the station. An unmanned Russian Progress resupply ship sends up approximately $9 million worth of water every few months. NASA engineers at the Marshall Space Flight Center, in Huntsville, Ala., asked: How much more weight—and money—could we save if we made the UPA even more efficient?
To answer that question, the engineers at Marshall needed better data on the temperatures generated by the DA. To get that data, they had to place temperature sensors inside the unit, where the spinning inner drum, high temperatures, near vacuum and caustic liquids would destroy ordinary temperature probes. And even if the probes could survive such a harsh environment, gathering temperature data from them could prove equally challenging.
In October 2014, NASA’s engineers met these challenges with the help of Phase IV Engineering, an RFID and wireless sensor provider based in Boulder, Colo., and began collecting the data they need from a test DA at Marshall. The solution involves resin-encased passive RFID sensor tags attached to the device’s titanium inner walls, custom-designed antennas and an external reader. The data collected could lead to both increased efficiency for the UPA on the space station and improved urine-distillation designs for future spacecraft. Ultimately, better data on the systems used in space to recycle water could benefit water-reclamation efforts proposed or in use in drought-stricken areas on Earth.
An Out-of-the-Ordinary Solution
From the beginning, it was clear that current instrumentation would not work to collect data from the interior of the DA. The unit’s heated outer jacket remains stationary, but the inner drum rotates at 220 revolutions per minute, ruling out wired temperature sensors. That factor alone led the NASA engineers to conclude that only RFID technology could get the job done. “Wireless operation was essential for us, since running cables in the system would be practically impossible,” says Christopher Evans, an aerospace technologist leading the team.
In addition, with only an inch of clearance between the outer and inner drums, any data-collection solution the team put into place had to be compact. Finally, the solution had to be able to survive the high temperatures—up to 140 degrees Fahrenheit—as well as the caustic bath of urine and the chemicals used to treat it for extended periods of time. Passive RFID tags, with their low profile, seemed to fit the bill. Plus, once installed, battery-free passive tags would not need to be serviced. But RFID technology was outside the expertise of the NASA team.
“We needed a developer who could not only provide hardware, but also design, manufacture and install a complete sensing system that could be integrated into our setup,” Evans says. “Since our application was unusual, we expected from the start that many components would need to be customized.” After getting input from UPA experts, thermal and fluid physics specialists, computational and modeling experts, materials scientists and wireless sensing engineers, the team put out a request for quotation to find out if a solution was even possible.
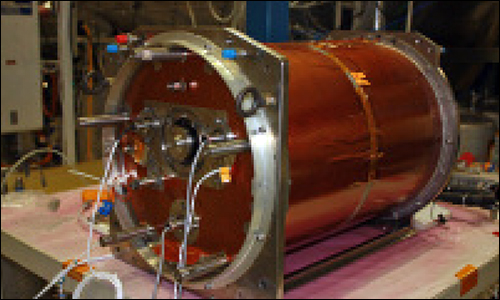
Among those responding to the RFQ was Phase IV Engineering. The company had a clear understanding of the challenge of crafting a purpose-built solution to meet NASA’s needs. To prepare their response to the RFQ, Phase IV engineers constructed a mockup of the DA out of sheet metal, and documented the process of rigging up RFID tags to demonstrate that the tags could be read even as they passed out of the line of sight of external readers. “That’s the way we operate,” says Phase IV CEO Scott Dalgleish. “Probably 80 percent of our projects start with an inexpensive proof-of-concept test, so we agree with the client: What’s the hardest, most challenging part?” That one-inch gap between the drums provided the biggest challenge for this project.
Satisfied that their requirements could be met, NASA put out a request for proposal to select a solution provider. Phase IV won the job in May 2014, and got to work putting together the hardware that would be used in the test UPA.
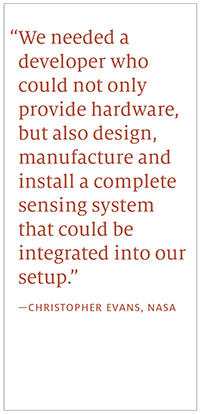
The Phase IV engineers designed a solution that included eight passive ultrahigh-frequency RFID sensor metal-mount tags, produced by their company. To be effective, the tags had to be mounted to both the inside and outside of the DA’s interior drum. Four tags would be affixed to each surface.
To attach the tags, they used an epoxy encapsulating material that could both mold the tags to the surfaces of the drum, and protect the tags from the sulfuric acid and other chemicals added to the urine. The shape of the epoxy surrounding the tags was critical, Evans notes. “We wanted to minimize the impact of the sensors on the fluid flow,” he says, “and we kept that in mind as we designed the shape of the sensors.” With specifications from Evans and his team that included the need for rounded edges as well as a very low profile, the Phase IV team came up with the ultimate design.
The Phase IV team also custom-designed antennas to be placed both inside and outside the DA to read the sensor tags. The shape of the DA’s interior dictated the exact placement and configuration of the antennas. “The shape of the DA hardware also posed some challenges as we worked out how to position the sensors and antennas to get readings in the areas we needed while also having clear sight lines to the reader,” Evans explains.
The team placed two antennas on the DA—one on the stationary shaft running through the inner drum, and one on the outside of the outer drum. The antennas were connected to a ThingMagic Vega UHF RFID reader to collect data at the rate of one pulse per second from each tag as it spun inside the DA. Phase IV’s own Sensor Reader Assistant software running on a Windows 7 PC computer would collect and display the data as well as output it to a comma-separated values (CSV) file on demand.

Going Where No RFID Tag Has Gone Before
The system worked well in theory, but in practice, molding the tags to the surfaces of the DA’s inner drum and installing the custom-designed antennas proved tricky. Phase IV engineer Bill Simms spent several weeks developing the right technique for installation. “We duplicated the cylinder here at Phase IV,” Dalgleish says, “and our senior mechanical engineer practiced and practiced and practiced molding the sensors onto the titanium drum.” That meant that when Simms and his colleague, Joe Letkomiller, arrived at Marshall to install the system on the DA test hardware, they wasted no time completing the job. “They had it up and running the next day,” Dalgleish says.
Besides mounting the tags and antennas in such a tight space, a major challenge was getting accurate and consistently strong reads from the tags as they spun around in the DA. “They would only be in view of the antenna for a short time during each rotation,” says NASA’s Evans. “Arranging components so reads could be completed in this short timeframe was a crucial task.”
“In order to read the tag, we actually have to bounce the radio energy between those two drums,” Dalgleish explains. He chalks up the project’s success to the UHF technology incorporated in the tags and readers. “We’re using UHF metal-mount antennas that are especially tuned to the titanium drum. That’s something new in the last year or two. In the past, RFID sensing was just done at low frequency and high frequency, and those fields are magnetically coupled.”
Tweaks are now in progress. “One challenge we’re still dealing with is working out the ideal process for operating the sensor system,” Evans says. “In our application, we want the sensors to provide continuous, real-time data, but there’s a tradeoff between the accuracy and frequency of measurement. We’re still working on finding the right balance as we experiment and gain experience with the new equipment.”
All told, Evans says, adding RFID-enabled temperature probes to the DA cost NASA less than $100,000, or the cost to send less than two gallons of water to the International Space Station. If the data collected can make the UPA on board the station even slightly more efficient, there’s potential to save much more in launch costs over the remaining life of the space station, which is projected to remain operational until 2024.
Down-to-Earth Benefits
“NASA was thrilled” with the results of the project, Dalgleish says. NASA’s Evans concurs. “The new sensors have already given us the first-ever temperature measurements from parts of the UPA that were previously considered inaccessible,” he says. “The readings from these sensors will give us much greater insight into the fine details of our process.” That insight could help the DA now on board the International Space Station run more efficiently, even though there are no plans to install RFID tags on that unit.
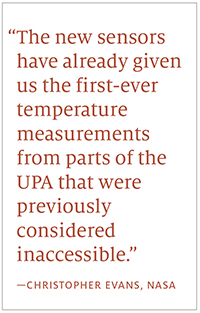
In addition, the data gathered on the ground should help NASA engineers design next-generation water-reclamation systems that are more efficient than the UPA for future space stations and deep-space missions, as well as for reclamation efforts here on Earth, Evans says. Those future designs might well include RFID sensor tags built in to gather operational data while in use, not just from ground-based test units. Wireless tags that don’t require batteries and that can stand up indefinitely to the environment inside an operational distillation system would require no maintenance by astronauts and could return valuable data for the life of the system.
Along with gathering data from the UPA, Evans also sees a benefit in increasing NASA’s experience with RFID systems in general. “There’s a lot of potential for using RFID sensors to take measurements in difficult places like the UPA, or to simplify sensor networks,” Evans says. “The space shuttles had a huge amount of cabling for the numerous sensors located throughout the spacecraft. Using a wireless sensor network instead is an attractive option to make maintenance easier, not to mention the weight savings from eliminating a bunch of cable.”
As for the future of RFID technology for the UPA sensing project, Evans sees additional possibilities. “There are many other locations in the system where we’d like to get data,” he says, “and as we gain experience operating the system, we’ll look into expanding the network with sensors in additional locations.” That might include installing tags to measure not just temperature, but other parameters as well. “A benefit of RFID is that with the infrastructure we have in place, adding sensors to the network is relatively simple.”