When Carl Closmore, the lab supervisor at Medtronic‘s Electronic System Design (ESD) division, in Mounds View, Minn., considered ways to help him locate any of the 2,600 electronic tools in use at his three laboratories, he visited other companies that similarly manage large numbers of tools, in order to view how they addressed the problem. What he found was that other labs had similar difficulties—determining a tool’s whereabouts was often done visually, by looking around engineers’ workstations and under papers, and sending out mass e-mails. Locating tools required for calibration or maintenance purposes could take weeks, and even then, not every item could be retrieved. It seemed to be an issue that plagued many labs, Closmore says, noting that the “inability to locate equipment in a timely manner decreases productivity and morale.”
Therefore, Closmore began working with enterprise software platform provider Stratum Global and automatic-identification systems integrator AbeTech, to design an RFID solution that he could use to track down items within the labs, as well as know when any equipment is removed from one of the three sites—and by whom. The solution, which utilizes handheld and fixed RFID readers and software purchased from Stratum Global and AbeTech, has been in place for three years, Closmore says. During that time, the system has saved thousands of hours that would otherwise have been spent searching for the missing equipment. A separate Medtronic department has recently adopted part of that solution at its own location, using handheld readers only, while another is currently preparing to do the same.
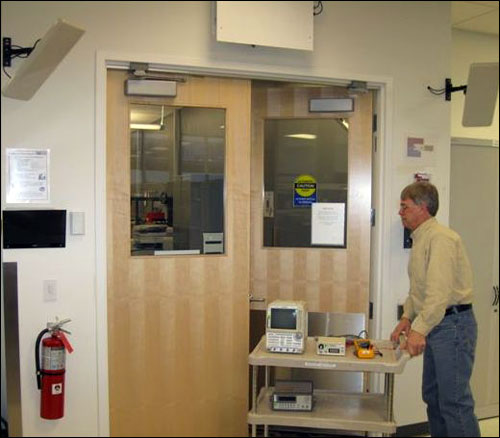
Medtronic develops medical technologies and equipment used worldwide. The three ESD labs employ 38 technicians and 47 engineers who design and test all implantable cardiac pacing systems and defibrillator devices that the company provides. The labs comprise a total of more than 100 workbenches in approximately 15,000 square feet of space. Not only do technicians and engineers need to know where its equipment—such as handheld meters, analyzers and oscilloscopes—is in order to use it, Closmore also needs to find about 150 items per month that are due for calibration. Although he had initially considered a bar-code solution or a manned tool crib (in which equipment not in use would be stored and made available to technicians and engineers), those methods still required extra labor hours to check the tools out to individuals, and to manually find any missing items. What’s more, the company wanted a system that would not require staff members to sign for a specific piece of equipment, and to then feel responsible for that item until it was returned to a designated area.
Closmore settled on a solution employing EPC Gen 2 passive ultrahigh-frequency (UHF) tags, as well as ThingMagic Mercury fixed readers installed at the doorways to three laboratories. At each portal, one interrogator is wired to four antennas, two are mounted on the wall near the ceiling at the front side of the doorway and two are mounted on the wall near the ceiling at the back side, enabling the Statum Global TagNet software to ascertain whether equipment is entering or leaving a room. He also placed motion detectors and cameras above the doorswired . Stratum Global’s TagNet software manages data from the RFID readers, as well as from the motion detectors and cameras, and interprets that information. The AbeTech software then integrates that tag data with Medtronic’s back-end management system so that it can be viewed by employees on Medtronic’s database. The lab also has several Motorola MC9090-G RFID handheld readers with a Geiger-counter function that emits a beep at greater frequency upon nearing specified RFID tags, so that Closmore can more easily locate tools that require calibration.Each month, Closmore turns on the handheld reader and uses a Wi-Fi connection to Medtronic’s existing management software to access a list of equipment requiring calibration, inspection or maintenance. The handheld then begins reading tags within the vicinity, and when a tag ID number matches one on the list, the device begins beeping. As Closmore picks up the item to which that tag is attached, he acknowledges it on the handheld by pressing a prompt. That object is then removed from the list. If the reader detects multiple items in the vicinity, he must select each one on the handheld display as he picks it up and places it on a cart destined for the company’s metrology department, which calibrates and repairs the test equipment. Once all items have been located, the system is updated to indicate that all necessary equipment has been retrieved.
When the cart is rolled toward the lab’s exit, the portal’s motion detector determines that someone has approached the doorway. The Stratum Global TagNet software then directs the reader to capture each tag’s unique ID number, and instructs a camera to photograph Closmore (or any other employee moving the equipment). If the cart continues through the doorway, the TagNet software determines the tags’ direction (in this example, out of the lab), and logs that information in the TagNet software. In that way, the software stores not only detailed records indicating what has been removed from the lab, but also a picture of who removed it, which can later be used if ESD’s managers need to determine which employee removed an item from the lab.
If a piece of equipment is carried near the doorway, but not through it, the motion detector will also prompt the TagNet software to trigger the taking of a photograph. However, if the item is not detected again by the second set of antennas on the other side of the door, the system determines that the object has not been removed, and the picture is thus not saved.
Upon being returned from the metrology department, the items pass through the portal once more, and the software is updated to indicate that all of the equipment is back in that lab.The staff can utilize the software to determine whether a particular piece of equipment is in one of the labs—and, if so, which one—or whether that device has been taken out of the labs for servicing. If the software indicates that the tool in question is in a certain lab, the handheld’s Geiger-counter function can then be used to pinpoint that item’s location.
Equipment is tagged with various RFID tags, depending on an item’s size. The smallest tag Closmore uses is Confidex‘s Steelwave Micro metal-mount tag, which is approximately the size of a stick of Trident gum, and is attached via an adhesive. One challenge he faced involved ensuring a high read rate when the antennas were mounted close to the ceiling, rather than at the level of the carts that typically carry equipment through the portal. That ceiling installation was required by the company to maintain aesthetics, Closmore explains. The tags have a read range of three to four feet, he says, adding, “We’re about 93 percent accurate” with tag reads at the portal.
Prior to using an RFID system, Closmore estimates that searches for equipment due for calibration or inspection required about 40 man-hours every month. Since the system’s installation, however, the task has taken an average of only about two to three hours. Previously, locating equipment that has left the lab took days or weeks, while only 20 minutes or less are required for RFID. The system cost $100,000 for hardware, software and installation, Closmore says, though the lab has recovered about 100 hours of engineering time per month. “There’s no doubt about getting our money’s worth,” he states.
Most recently, the RFID-enabled handheld portion of the system is being deployed in Medtronic’s Neurological Therapies division (where the system is already in use), as well as in the firm’s Environmental Health and Safety division. Both departments will use the RFID handheld readers to locate tagged equipment.