In South Korea, four companies, including those that sell books, health products or cosmetics, are employing RFID-enhanced pick-to-light (PTL) systems to fulfill orders from retailers and consumers. The so-called Multi-Purpose System (MPS), developed by Korean logistics firm CJ GLS, is designed to improve on PTL systems, which use LED readouts to direct staff members to determine the locations of goods, as well as the quantities required, based on data provided by warehouse-management systems (WMS).
Chris Yoon, the MPS project manager at CJ GLS, says changing customer demands have led to new challenges in stock picking and order fulfillment. “Order-fulfillment systems were traditionally designed for processing a small volume of large-sized orders,” he explains. “With smaller orders increasingly common, these systems are no longer efficient or effective, distribution costs have increased and customer service quality is lost. MPS eliminates all paperwork, and stock movements are controlled electronically. Information is transmitted to the warehouse, and the picker is directly notified of the work to be done at each of the shelves, and where the product is to be stored.”
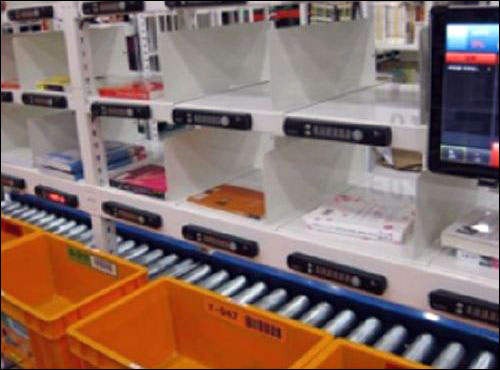
An MPS indicator (MPI) is an electronic device that can be installed anywhere within a warehouse or factory, to display instructions to employees. Typically, multiple MPIs are installed on shelves at each picking station. The devices can illuminate different colors to signal different instructions, and can flash an arrow indicating whether an operator needs to pick from the shelf compartment above or below the display. While traditional PTL systems also guide workers to the appropriate location to find stock, Yoon says, the RFID-enhanced system is completely automated, eliminating the need to manually scan bar codes on containers used to carry ordered items, and thereby saving the staff time.
Passive EPC Gen 2 RFID tags, supplied by Alien Technology and RFcamp and operating in the 908.5 to 914 MHz ultrahigh-frequency (UHF) band, are attached to the plastic buckets in which workers place products required to fulfill an order. RFID readers, supplied by Alien and Minerva, are installed beneath the conveyor belt at the point at which the order buckets are first introduced into the picking line, as well as at several other locations along the line.
When a bucket is inserted into the picking line, the readers detect its RFID tag, and order information from the WMS, or from MPS Manager middleware, is transmitted wirelessly to the MPIs. This causes each appropriate MPI to activate a light, pointing staff members to the corresponding item to be picked. Upon picking up the designated item, a worker presses a button on the MPI to let the system know that this action has taken place. Once finished picking items for the order corresponding to that bucket, the employee then informs the system of this status by touching the display screen on the T.Panel—an Apple iPad or a tablet PC mounted at his or her picking station.
The MPI transmits information back to the MPS Manager middleware, using the ZigBee communication protocol, based on the IEEE 802.15.4 standard. A visibility software application known as Visualizer can then display information, such as the real-time stock status, thereby allowing for real-time stock replenishment.
When the bucket arrives at an inspection and packing station, an RFID interrogator identifies it by automatically reading its tag, so the inspection worker need not scan a bar code to call up information pertaining to that particular order.
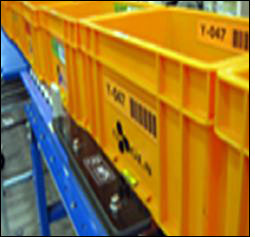
Cosmetics company Fresh Korea was the first to trial the MPS solution, installing five RFID readers and 2,000 tags at its warehouse in February 2010.
“[The department stores] that Fresh Korea distributes to wanted greater accuracy and lower costs,” Yoon explains. “We installed 1,000 MPIs, and the result was zero percent error rate by staff, reduced stock inspection time of 43 percent compared to manual inspection, and reduced picking time for each department store by 35 percent.”
CJ GLS then rolled out the solution at eBay‘s South Korean book-distribution warehouse, with 1,500 MPIs, six T.Panels (iPads) and 10 RFID readers installed, and 1,000 RFID tags used.
“It wanted fast picking for shipment to consumers and lower costs,” Yoon states. “The result of using MPS was zero percent error rate, reduced picking time by 200 percent compared to manual and PTL systems, and increased productivity per worker of 233 percent compared to manual systems and 115 percent compared to PTL systems.”
MPS has since been rolled out to health-products firm Olive Young and cosmetics company LG Household & Health Care, with similar success. According to Yoon, there are plans to roll out the system at up to six different businesses this year, including electricity, food distribution and fashion firms.
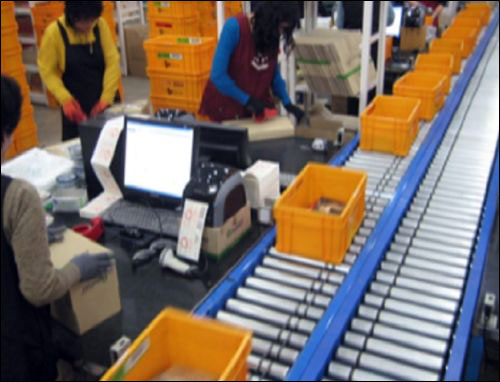
“The advantage of MPS is increased productivity by staff, increased accuracy, real-time information on order progress, real-time monitoring of stock and improvement in system management and customer service,” Yoon adds. “What really stands out about MPS is that it maximizes speed, productivity and efficiency, while reducing error rates to zero.”
CJ GLS claims its MPS technology is saving a company that spends almost $40 million per year on logistics approximately $1 million when compared with manual picking systems, and almost $300,000 compared with PTL systems. The savings is accrued through inventory picking, as well as order inspection and packing, and via a reduction in warehouse space, thanks to greater accuracy in stock requirements and replenishment.
“It is a visual method that is much more intuitive than paper-based systems,” Yoon says. “The simplicity of the system means that virtually no staff training is necessary.”
The Visualizer also supports a hybrid real-time location system (RTLS). CJ GLS trialed the tracking of a forklift throughout a warehouse, installing an EPC Gen 2 RFID reader on the vehicle’s roof.
“For RTLS tracking, we use tag data as geographical coordinate data inside the warehouse,” Yoon explains. “First, we encoded thousands of tags, each with its own unique EPC code. After that, we mapped each tag code with warehouse location coordinate data, so each individual tag can represent a specific location point of warehouse.”
As the forklift is driven, the vehicle’s RFID reader captures the ID numbers of nearby tags, transmitting that information to the Visualizer software via the warehouse’s Wi-Fi network.
“Visualizer analyzes the path of the forklift, based on the captured data,” Yoon says. “When the data capture has finished, Visualizer generates a report so we can know the operational efficiency of individual forklifts. For example, if popular stock is stored far from the picking and shipping zone, it can cause an inefficient forklift routing path.”
To coordinate mapping, Yoon says, CJ GLS initially tried utilizing metal-mount passive tags attached to metal fixtures within the warehouse, but found such tags to be too expensive to attach to thousands of locations. Instead, the company switched to ordinary EPC Gen 2 tags that were hung via magnets from various fixtures around the warehouse—a cheaper alternative that worked just as well as the metal-mount tags, he notes.