San Francisco-based Internet of Things (IoT) technology firm Safehub has released the latest version of its structural-integrity IoT system, with a wireless solution called Yure (pronounced “you-ray”). The company says it has a vision for its latest sensor-based system, named for the Japanese term for “tremor,” and the software platform in which sensor data is managed and shared. The company seeks to make the technology affordable for buildings in potential earthquake zones so that seismic activity and damage can be monitored, no matter where a building owner or manager is located.
Yure is the company’s third iteration of an IoT solution and the second to use cellular connectivity, so that building owners can track the conditions of their structures and any potential damage involving seismic events. The solution is aimed to democratize building intelligence, says Andy Thompson, Safehub’s cofounder and CEO, by serving as an affordable, easy-to-deploy system. A few sensors, attached to a wall and plugged directly into a building’s outlets, forward data to a server via cellular connectivity. Users then receive alerts and can view historical data using the software-as-a-service.
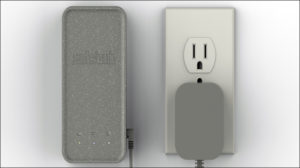
Safehub’s Yure sensor
According to Safehub, devices for this latest version provide longer energy storage with rechargeable batteries to store and transmit data, even if a building’s power goes out, or to store information for at least one month until cellular connectivity returns. Since the company’s first IoT offering was released three years ago, the system has been adopted by businesses in the United States and Canada with assets globally, and with several hundred sensors being used throughout multiple countries. Those employing the technology include Amazon and Fedex for their commercial buildings, as well as the California Joint Powers Insurance Authority and North Shore Emergency Management, located in Vancouver, B.C.
“This is going to be the sensor that we scale worldwide,” Thompson predicts. Unlike most natural disasters, he says, earthquakes catch people by surprise. Those who operate or own buildings in earthquake zones are familiar with the initial disruption, shock and need for information that follows once the shaking stops. The first thing building owners and managers need, he says, is usually timely, building-specific information. The problem becomes more challenging for large companies that may be headquartered in another part of the world.
A business that manages multiple buildings in an earthquake-prone city must assess which structures might have been hit the hardest, where a team of inspectors should go first, and where evacuations need to happen immediately. While working as the head of engineering consulting company Arup‘s Global Catastrophe Risk & Insurance practice, Thompson says, “I saw first-hand the need for and lack of building-specific information.”
Safehub was launched in 2015 to create a low-cost solution leveraging the sensors and cloud-based software required to provide information to customers’ smartphones. Typically, a single sensor is plugged in at the ground level of a building, says Clement Barthes, Safehub’s VP of engineering, while other sensors measure conditions toward the top of the building. Each sensor comes with an accelerometer to detect shaking, as well as a magnetometer that serves as an electronic compass to identify where the sensor is installed in the building, and a processor embedded with the Linux operating system.
A rechargeable battery in the latest version ensures that the device will continue to collect and transmit data without power or connectivity. The sensors come with sub-GHz modules for RF connectivity between multiple sensors, though that type of transmission is not currently being used. The device features 32 gigabytes of memory, enabling it to store up to a month’s worth of data in the event that the cellular network goes down. Processed data is sent twice daily, while raw data can be uploaded on demand, or immediately if an earthquake is detected.
While the device filters and processes data at the edge, the software correlates sensor data, such as the level of tremors, with how a building of a specific type—for instance, a concrete office tower built in the 1960s. The servers analyze those measurements and can query the sensors to upload raw data if necessary. All of that information, Barthes explains, provides an indication of whether the building has been structurally damaged. In addition to detecting earthquake impact, the sensor also measures the building’s natural frequencies. Sudden changes in natural frequencies may indicate damage.
Based on the results, users of the technology may receive a text message and an e-mail alert within approximately two minutes of an event. Upon receiving the alert, they can select the provided links and be connected to the software platform and dashboard analytics. They can also create PDF reports and forward them to their company’s management, or to insurers or other partners. What’s more, the software employs risk analytics and catastrophe modeling to help building owners identify problems in near-real time.
Although there are other sensor-based solutions available for building structural health monitoring, Thompson says, those sensor solutions may be highly complex and thus a costly alternative. “Our focus is different,” he states. “We aim to democratize. We say every building should have this technology.” As such, the system is designed to be low in cost and easy to install—as commonplace as a smoke detector, he claims. In return, the solution provides basic information rather than details regarding the specific status of different parts of a building.
“We provide indicative understanding rather than detail-level information,” Thompson explains. The company views the solution as a tool to be used to assist “boots on the ground” structural engineers who will inevitably be needed to physically evaluate a building. “We aim to provide information to support those engineers, not replace them.” To date, the system has been deployed in buildings ranging from skyscrapers to warehouses, as well as big-box stores, apartment buildings and more.
The latest device’s upgrades, according to Safehub, include the use of cellular LTE Cat-M1 to mitigate data-collection interruptions, as well as a low-power MCU that allows most calculations to take place on a device, thereby reducing communications with the cloud server and increasing efficiency. In the future, Thompson says, the company may opt to provide additional services to track such events as flooding, hail storms and high winds, in order to address other natural hazards that buildings face.